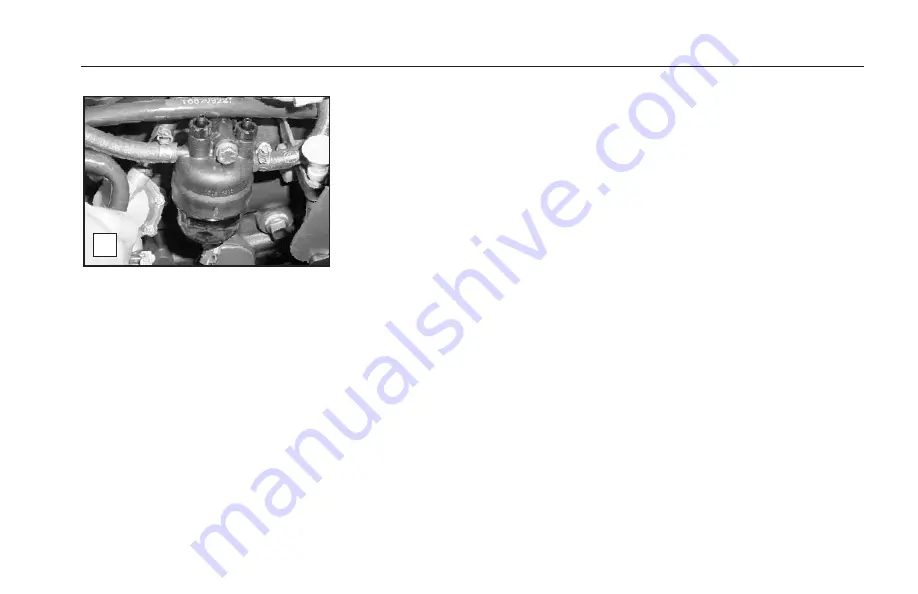
19
Water Separator
The water separator (photo B, located on
the left side of the hyd. reservoir)
removes water from the fuel supply as
the engine runs. Drain the water separa-
tor daily to maintain proper function.
To drain the water separator:
1. Loosen the twist valve on
the bottom of the separator.
2. Retighten the valve once all of the
water has been drained from the
catch bowl.
Undercarriages
The undercarriage assemblies typically
operate in harsh working conditions.
They work in mud, gravel, debris and
various other abrasive materials during
operation. ASV recommends a daily
inspection of the undercarriage assem-
blies and cleaning if necessary.
Materials that are particularly sticky or
abrasive like clay, mud, or gravel should
be cleaned from the undercarriages
often to minimize component wear. A
pressure washer works well for cleaning
materials from the undercarriages. At
times when a pressure washer is not
available, use a bar, shovel or similar
device to remove foreign materials.
When cleaning, pay particular attention
to the drive motors/sprockets and the
front and rear wheels where debris is
likely to accumulate. If working in scrap
or debris, inspect the undercarriages
more often and remove foreign objects
that may wrap around or lodge them-
selves between components causing
premature wear and damage.
Operation on sand, turf, or other finished
surfaces may require less frequent
cleaning, but daily inspection is still
advised.
M
MA
AC
CH
HIIN
NE
E M
MA
AIIN
NT
TE
EN
NA
AN
NC
CE
E
B