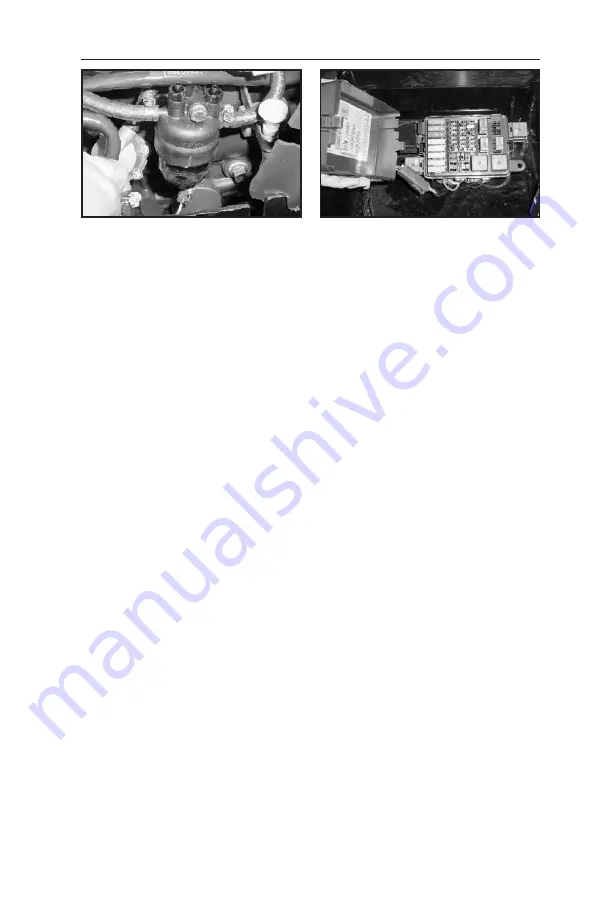
MAINTENANCE
Engine/Electrical
36
Water Separator
The water separator removes
water from the fuel supply as the
engine runs. Drain the water
separator daily to maintain prop-
er function.
To drain the water separator:
1.
Loosen the twist valve on
the bottom of the separator.
2.
Retighten the valve once all
of the water has been
drained from the catch bowl.
Accessory Belts
The engine uses a belt to drive
accessories like the alternator,
water pump, and cooling fan.
Belts typically stretch and wear
during their service life. As a
result, the accessory belt on the
ST-50 should be visually
inspected daily for tension, con-
dition, and presence prior to
operating your machine.
To check drive belt:
1.
With the engine off and cool,
remove the key from the igni-
tion to avoid accidental start.
2.
Remove the engine cover
from the machine.
3.
Visually inspect the belt to
make sure it is present, tight
on the pulleys and and in
good condition.
Fuse Panel
The electrical system in the ST-
50 is equipped with fuses that
protect the electrical compo-
nents from damage. They can
be found in the fuse panel locat-
ed beneath the passenger seat.
In the event of an electrical mal-
function, the most logical place
to start is the fuse panel. Check
the fuse(s) related to the prob-
lem you are having and inspect
it. If the fuse filament appears
broken, black or burned, it
needs to be replaced. Replace
fuses with the correct amperage
replacement fuse only.
Replacing a fuse with one of a
higher amperage rating may
burn out the electrical compo-
nent the fuse was meant to pro-
tect. See the troubleshooting
section of this manual for an
additional resource to aid in
tracking suspected electrical
problems.
Summary of Contents for ST50 Scout
Page 6: ...5 ...
Page 11: ...SAFETY Warning Decal Locations 10 A B B F D C C G E ...
Page 48: ...47 ...
Page 56: ...SERVICE LOG 55 Hours Service Performed Notes ...
Page 57: ...SERVICE LOG 56 Hours Service Performed Notes ...
Page 58: ...Hours Service Performed Notes SERVICE LOG 57 ...
Page 59: ...SERVICE LOG 58 Hours Service Performed Notes ...