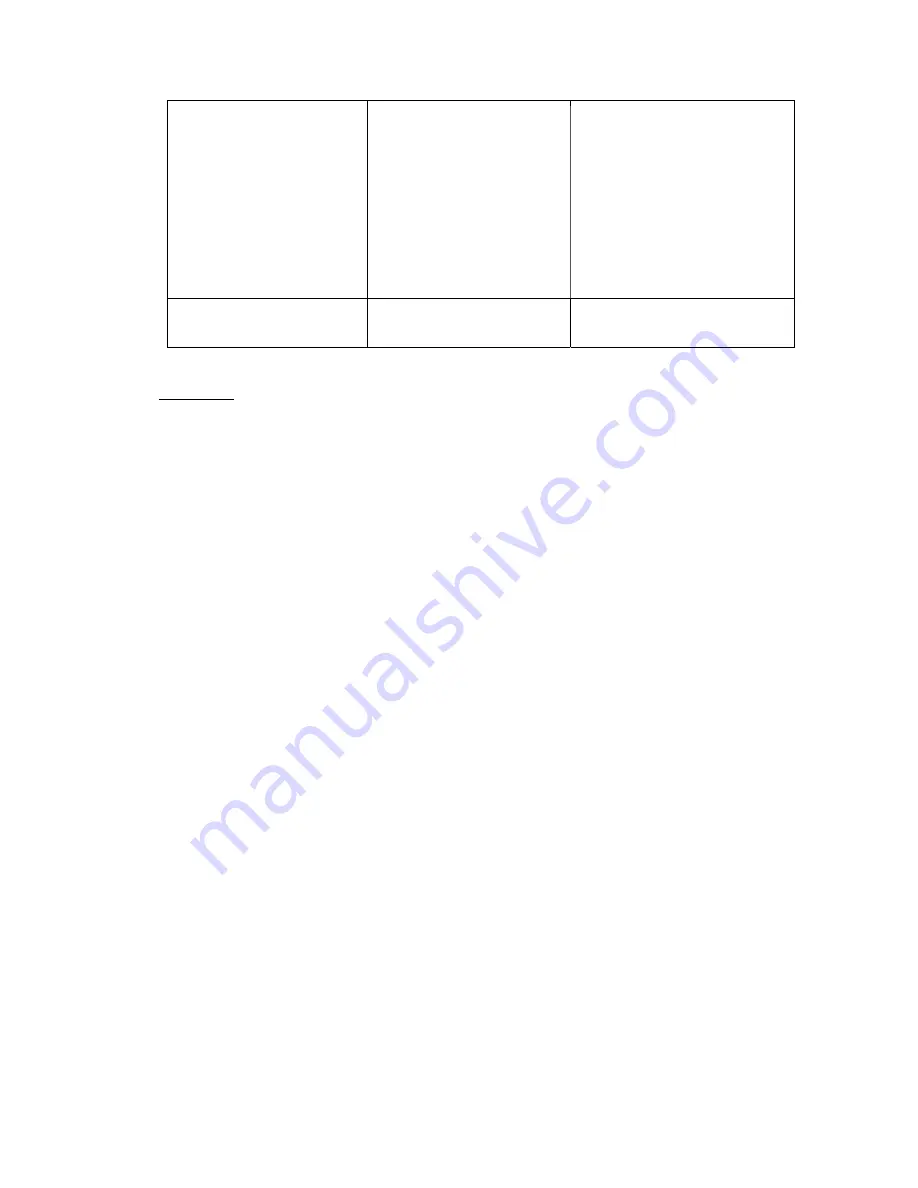
19
No lubrication.
It may be related to the oil amount,
oil fluidity or valve.
Check the oil level.
Observe the oil hose in the oil.
Open the valve.
Be sure to use the appropriate oil.
Blow air into the end of the hose
inside the drum with an blow gun.
Lubrication is less.
It may be related to the sprayer.
Open the dimmer on the sprayer.
12.
COMPONENTS
1.
ELECTRIC COMPONENTS
2.
HYDRAULIC-PNEUMATIC COMPONENTS
PART NAME
QTY
ELECTRIC MOTOR 1
SERVO MOTOR
2
POWER CABLE 5x2,5 mm
3,5 m
PART NAME
QTY
FRC 1/4 D MINI CONDITIONER
1
PNEUMATIC CLAMPS
6
KSØ50 x 5 PNEUMATIC CYLINDER
2
KSØ50 x 3 PNEUMATIC CYLINDER
2
KSØ63 x 5 PNEUMATIC CYLINDER
2