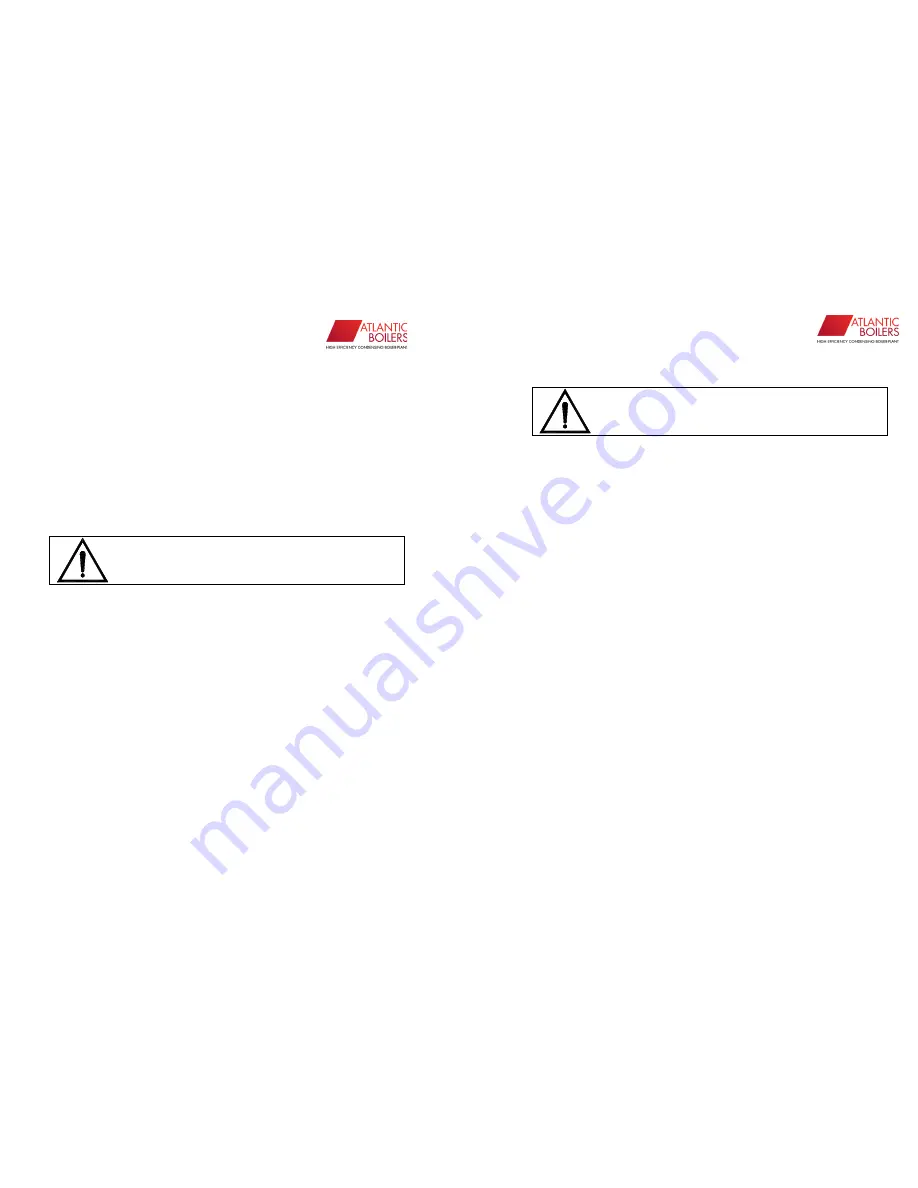
erensan
°
“
The Heating Engineer
”
06042007
19
FUEL SELECTION AND STORAGE:
•
Fuel complying with the characteristics indicated in the burner user
manual or burner vendor catalogues should be obtained.
•
Fuel transfer lines should conform to current technical specifications,
regulations and standards. The fuel tank-burner axis levels should not
exceed figures specified in the burner user manual.
•
Fuel tanks should conform to standards. A wall must exist between the
fuel tank and the boiler.
•
If fuel-oil is being used (especially of a heavier group), the necessary
arrangements (RING LINE) and heating installation should be prepared
for flow of fuel from the tank to the burner.
FILLING THE SYSTEM WITH WATER
The boiler should be filled with water before operation. The boiler should
not be operated before it is filled with water.
To fill the boiler with water, the main distribution and collection pipes,
the boiler feeding pipes, installation column valves should be opened
fully, water should be let in from the filling/discharge tap and it should
be filled slowly until water starts coming from the monitor pipe of the
Expansion Tank. In closed expansion systems, during water filling from
boiler filling/discharge tap, the air discharge tube valves and mechanical
purgers should be opened and then closed when it is observed that the
incoming water does not have bubbles. When the air tube at the top
most level of the installation or at the roof is completely filled with
water, filling will be completed.
BEFORE OPENING THE FRONT DOOR,
SHUT OFF THE BURNER AND SHUT
DOWN BURNER ELECTRICITY !
erensan
°
“
The Heating Engineer
”
06042007
20
The circulation pump should not be operated during the filling process.
The expansion tank connections should conform to the installation circuit
diagram.
PREPARATION OF BOILER FOR OPERATION
The boiler room must be designed to meet the combustion air requirements
of the boiler.
The boilers should be completely cleaned from internal and external dust,
soot, etc.
The smoke channel, smoke pipe and chimney cleaning doors should be
checked and leakages should be prevented.
The fuel heaters (when used with liquid fuel) and burner fuel connections
should be checked for leakage. In gas fuel applications, the conformance of
the provided pressure to the relevant burner and boiler, and if it has a seal,
the functional operation of the control system should be checked.
The fuel filters should be cleaned, heater thermostats should be set to
correct value, fuel valves should be set full and open.
The fuel combustion system should be reviewed with respect to the system's
working principles and each element should be controlled for proper
operation.
The boiler explosion door should be checked for proper operation.
Boiler safety devices (manometer, hydrometer, safety valve, visual and
sound warning system etc.) should be reviewed to ensure proper operation.
DO NOT OPERATE BOILER WITHOUT
WATER.