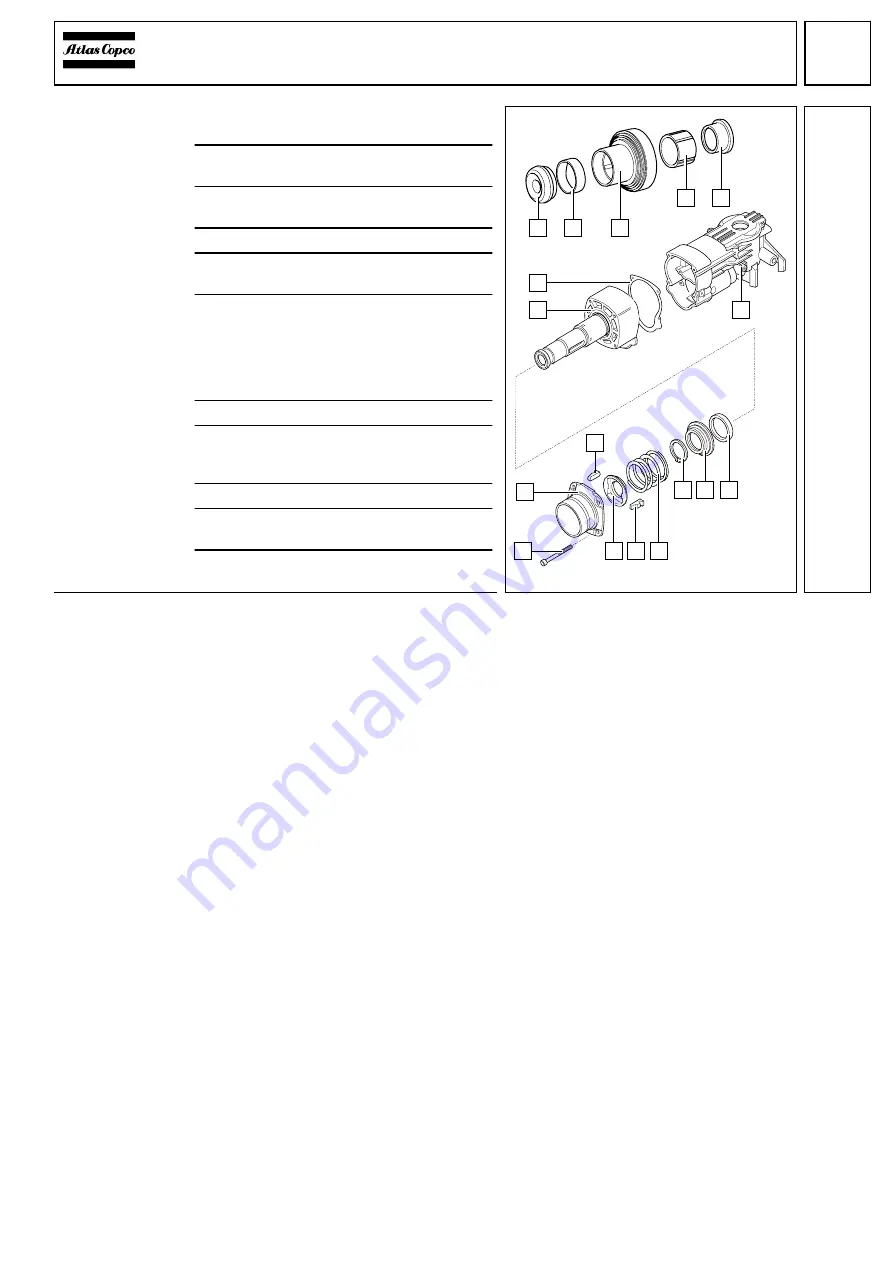
4
PAGE
Repair Instructions No.178.06/97
PN 6000 S
Detaching the
bearing end plate
1
Lever off the cap (3) with aid of a screw-
driver.
2
Remove the distance sleeve (4) and the
sleeve (5) from the machine.
3
Loosen the four screws (F). They are fas-
tened very tightly.
4
Remove the flange (G).
5
Remove the distance sleeve (6) and the
sleeve (7).
6
☞
Remove both locking levers (D) by
depressing the retaining plate (E)
against resilience. Remove the retaining
plate (E).
7
Remove the pressure spring (C).
8
Remove the bearing end plate (1) com-
pletely with the spindle sleeve from the
crankcase (8).
9
Remove the gasket (2).
10
Remove the locking ring (B) with aid of
special pliers.
11
Remove the backing flange (A) and the
felt washer (9).
1
6
5
4
3
2
7
8
9
A
B
C
D
E
F
G
D
8
Summary of Contents for PN 6000 S
Page 1: ......