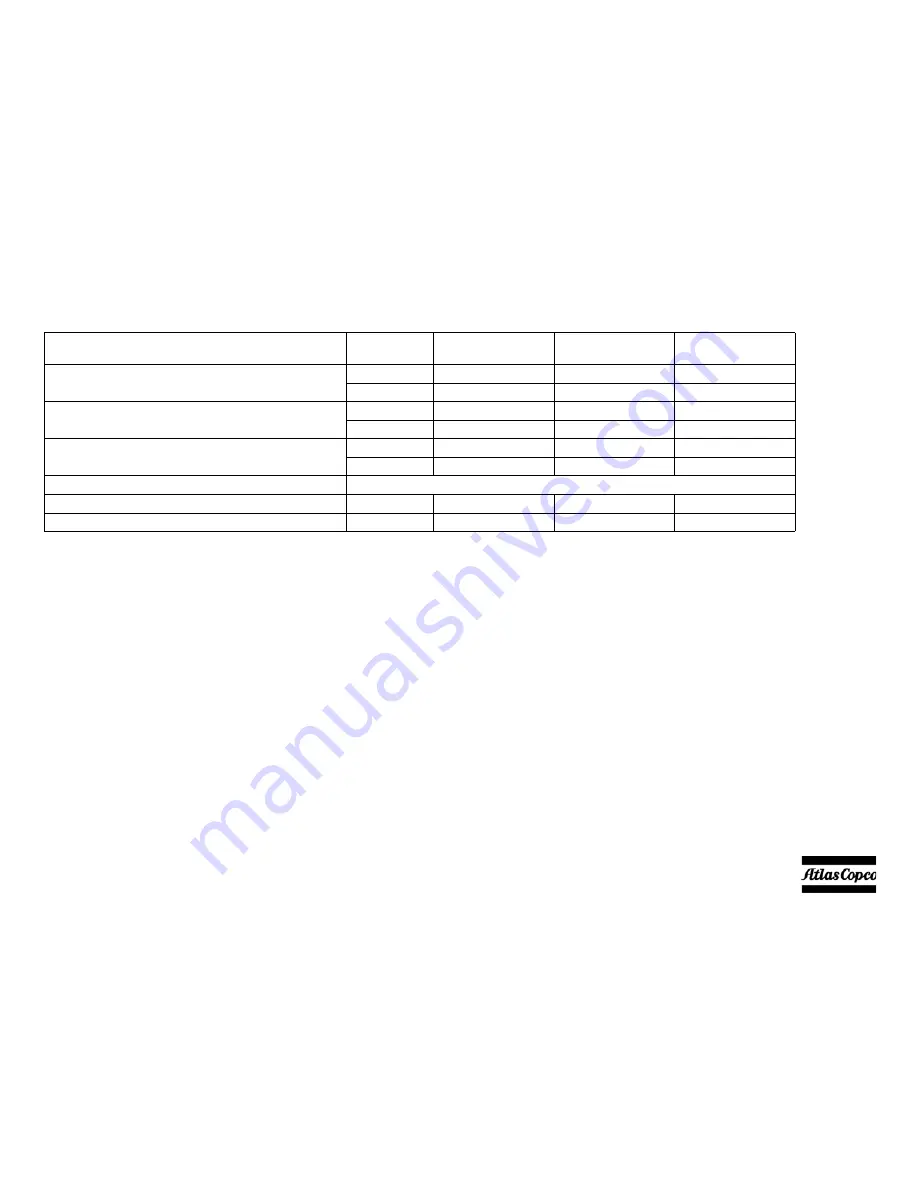
- 55 -
SETTINGS OF SHUTDOWN SWITCHES AND SAFETY VALVES
Designation
XA(S) 137 DD -
XA(S) 300 DD7
XA(S) 137 DDG -
XA(S) 300 DD7G
XAHS 107 DD -
XAHS 250 DD7
Engine oil pressure
bar(e)
6
6
6
psi
87
87
87
Engine oil temperature
°C
120
120
120
°F
248
248
248
Compressor temperature
°C
120
120
120
°F
248
248
248
Safety valve opening pressure
- EC type
bar(e)
10
10
15
- ASME type
psi
150
150
218
Summary of Contents for XA(S) 137 DD
Page 2: ......
Page 20: ... 18 CONTINUOUS REGULATING SYSTEM BOV UV UA VH RV AR CE SVa SR ...
Page 70: ... 68 Notes ...
Page 71: ......
Page 72: ...www atlascopco com ...