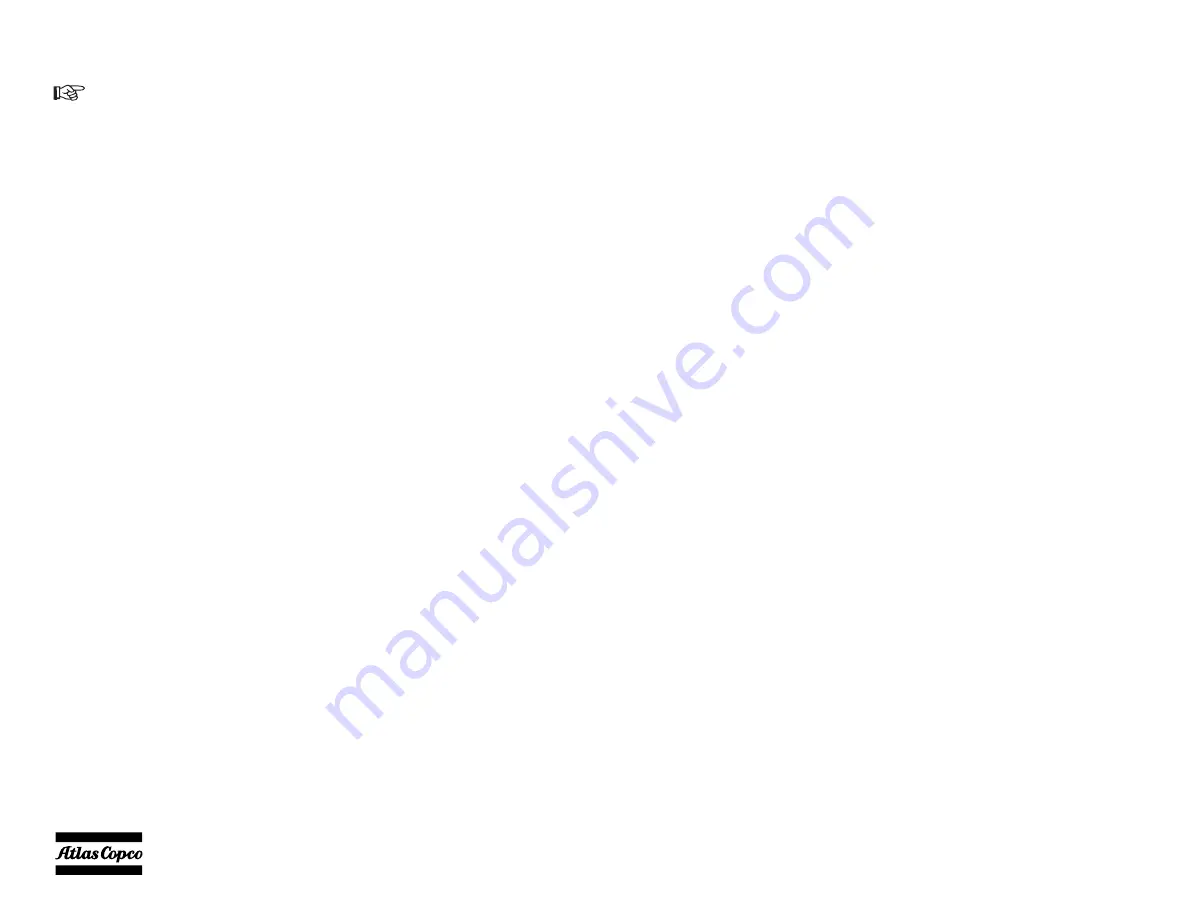
- 6 -
Safety precautions for portable compressor
Introduction
The policy of Atlas Copco is to provide the users of their
equipment with safe, reliable and efficient products.
Factors taken into account are among others:
- the intended and predictable future use of the products, and
the environments in which they are expected to operate,
- applicable rules, codes and regulations,
- the expected useful product life, assuming proper service and
maintenance,
Before handling any product, take time to read the
relevant instruction manual. Besides giving detailed
operating instructions, it also gives specific information
about safety, preventive maintenance, etc.
These precautions are general and some statements will
therefore not always apply to a particular unit.
When handling, operating, overhauling and/or
performing maintenance or repair on Atlas Copco
equipment, the mechanics are expected to use safe
engineering practices and to observe all relevant local
safety requirements and ordinances. The following list is
a reminder of special safety directives and precautions
mainly applicable to Atlas Copco equipment.
This brochure applies to machinery processing or
consuming air. Processing of any other gas requires
additional safety precautions typical to the application
and are not included herein.
All responsibility for any damage or injury resulting from
neglecting these precautions or by non-observance of
ordinary caution and due care required in handling,
operating, maintenance or repair, also if not expressly
mentioned in this instruction manual, is disclaimed by
Atlas Copco.
If any statement does not comply with local legislation,
the stricter of the two shall be applied. Statements in this
manual should not be interpreted as suggestions,
recommendations or inducements that it should be used in
violation of any applicable laws or regulations.
General safety precautions
1 The owner is responsible for maintaining the unit in a
safe operating condition. Unit parts and accessories
must be replaced if missing or unsuitable for safe
operation.
2 Use only lubricating oils and greases recommended or
approved by Atlas Copco or the machine manufacturer.
Ascertain that the selected lubricants comply with all
applicable safety regulations, especially with regard to
explosion or fire risk and the possibility of
decomposition or generation of hazardous gases.
3 The supervisor, or the responsible person, shall at all
times make sure that all instructions regarding
machinery and equipment operation and maintenance
are strictly followed and that the machines with all
accessories and safety devices, as well as the
consuming devices, are in good repair, free of
abnormal wear or abuse, and are not tampered with.
4 Maintenance, overhaul and repair work shall only be
carried out by adequately trained personnel; if
required, under supervision of someone qualified for
the job.
5 Whenever there is an indication or any suspicion that
an internal part of a machine is overheated, the
machine shall be stopped but no inspection covers shall
be opened before sufficient cooling time has elapsed;
this to avoid the risk of spontaneous ignition of oil
vapour when air is admitted.
6 Maintenance work, other than routine attention, shall
only be undertaken when the machine is turned off.
7 Before dismantling any pressurized component, the
compressor or the equipment shall be effectively
isolated from all sources of pressure and be completely
vented to atmosphere. In addition, a warning sign
bearing a legend such as "work in progress; do not
open" shall be attached to each of the isolating valves.
8 Before a machine is being repaired, steps shall be taken
to prevent inadvertent starting. In addition, a warning
sign bearing a legend such as "work in progress; do not
start" shall be attached to the starting equipment. The
battery shall be disconnected and removed or the
terminals covered by insulating caps.
9 Normal ratings (pressures, temperatures, speeds, etc.)
shall be durably marked.
10 Never operate a machine or equipment beyond its rated
limits (pressure, temperature, speed, etc.).
11 Maintenance and repair work should be recorded in an
operator's logbook for all machinery. Frequency and
nature of repairs can reveal unsafe conditions.
12 The machinery and pneumatic equipment shall be kept
clean, i.e. as free as possible from oil, dust or other
deposits.
13 To prevent an increase in working temperature, inspect
and clean heat transfer surfaces (cooler fins,
intercoolers, water jackets, etc.) regularly. For every
machine establish a suitable time interval for cleaning
operations.
14 All regulating and safety devices shall be maintained
with due care to ensure that they function properly.
They may not be bypassed.
15 Care shall be taken to avoid damage to safety valves
and other pressure relief devices, especially to avoid
plugging by paint, oil coke or dirt accumulation, which
could interfere with the functioning of the device.
16 Pressure and temperature gauges shall be checked
regularly with regard to their accuracy. They shall be
replaced whenever outside acceptable tolerances.
17 Parts shall only be replaced by genuine Atlas Copco
replacement parts.
18 Safety devices shall be tested as described in the
maintenance schedule of the instruction book(s) to
determine that they are in good operating condition.
19 Never use flammable solvents or carbon tetrachloride
for cleaning parts. Take safety precautions against
toxic vapors when cleaning parts in or with cleaning
products.
20 Observe scrupulous cleanliness during maintenance
and repair. Keep away dirt by covering the parts and
exposed openings with clean cloth, paper or tape.
21 Protect the engine, alternator, air intake filter, electrical
and regulating components, etc. to prevent moisture
ingress, e.g. when steam-cleaning.
To be read attentively and acted accordingly before towing, lifting, operating, performing maintenance
or repairing the compressor.
Summary of Contents for XAS 185 KD7 IT4
Page 1: ...XAS 185 KD7 IT4 Instruction Manual for AC Compressors English Engine Kubota V2403 M DI E3B ...
Page 2: ......
Page 13: ... 13 Main Parts ...
Page 15: ... 15 Compressor regulating system Load Condition ...
Page 19: ... 19 Electric system CIRCUIT DIAGRAM 1310 3200 71 ...
Page 27: ... 27 ALTITUDE UNIT PERFORMANCE CURVE ...
Page 33: ... 33 Adjustments and Servicing Procedures Adjustment of the Continuous Regulating System ...
Page 40: ... 40 ...
Page 41: ......
Page 42: ...www atlascopco com ...