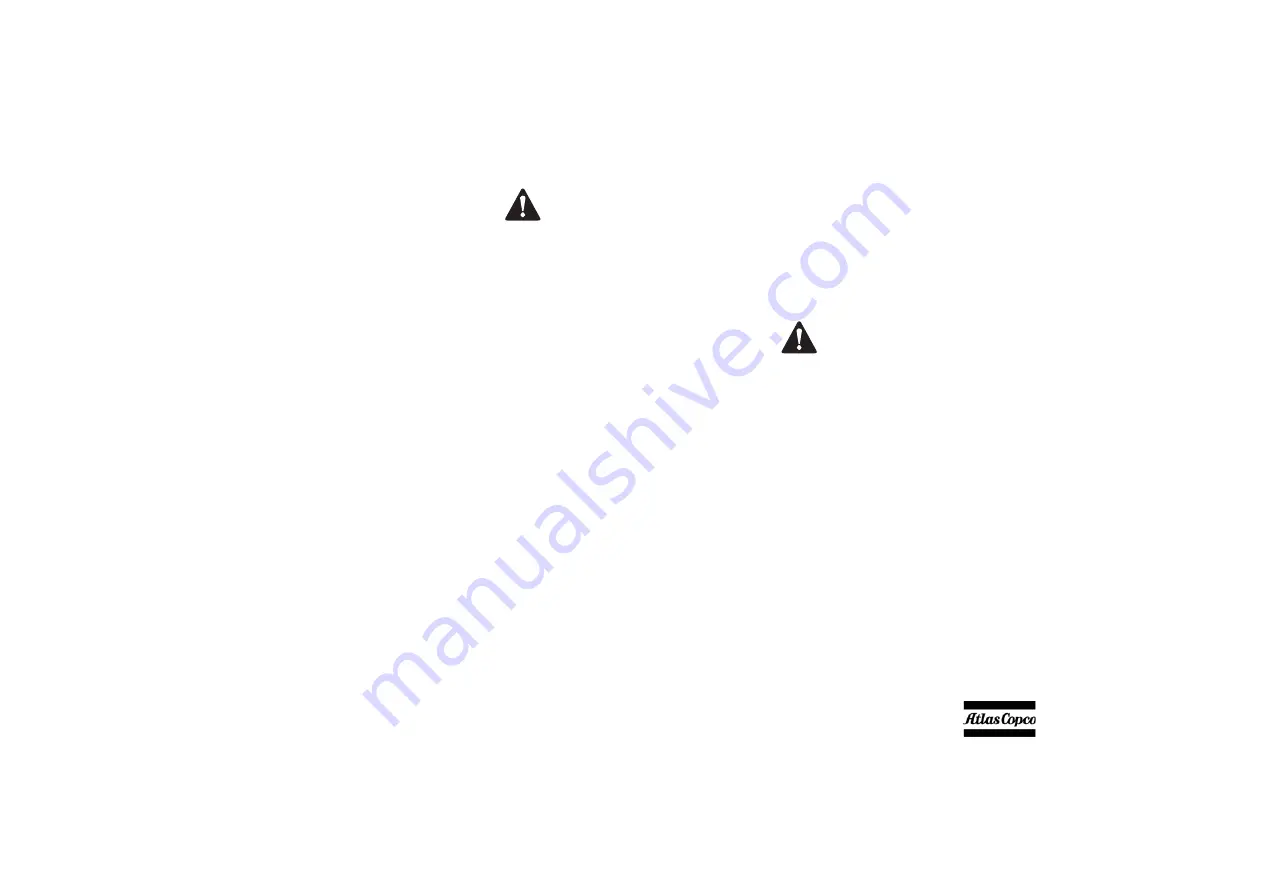
- 65 -
HANDLING PARCOOL EG
PARCOOL EG should be stored at ambient
temperatures, while periods of exposure to
temperatures above 35 °C (95 °F) should be
minimized. PARCOOL EG can be stored for a
minimum of 5 years in unopened containers without
any effect on the product quality of performance.
PARCOOL EG is compatible with most other
coolants based on ethylene glycol, but you only get
the benefits of 5 years protection when its used on its
own. Exclusive use of PARCOOL EG is
recommended for optimum corrosion protection and
sludge control.
For simple density-measuring of Ethylene Glycol and
Propylene Glycol in general the standard available
‘density’ measuring devices are used to measure the
concentration of EG. In case a device is used to
measure EG, no PG can be measured afterwards as a
result of the difference in the density. More specific
measurements can be done by the use of a
refractometer. This device can measure both EG and
PG. A mix of both products will be show unreliable
results!
Mixed EG coolants with identical glycol type can be
measured by use of a refractometer as well as the
‘density’ system. The mixed coolants will be
considered as one product.
The use of distilled water is recommended. If you
have exceptionally soft water it would be acceptable,
as well. Basically, the engine metals are going to
corrode to some extent no matter what water you use,
and hard water will encourage the resulting metal
salts to precipitate.
PARCOOL EG comes as a pre-mixed coolant to
safeguard the quality of the complete product.
It is recommended that topping up of the cooling
system is always done with PARCOOL EG.
COOLANT CHECK
In order to guarantee the lifetime and quality of the
product, thus to optimise engine protection, regular
coolant-condition-analysis is advisable.
The quality of the product can be determined by three
parameters:
Visual check
•
Verify the outlook of the coolant regarding colour
and make sure that no loose particles are floating
around.
pH measurement
•
Check the pH value of the coolant using a pH-
measuring device.
•
The pH-meter can be ordered from Atlas Copco
with part number 2913 0029 00.
•
Typical value for EG = 8.6.
•
If the pH-level is below 7 or above 9.5, the coolant
should be replaced.
Glycol concentration measurement
•
To optimise the unique engine protection features
of the PARCOOL EG the concentration of the
Glycol in the water should be always above 33
vol.%.
•
Mixtures with more than 68 vol.% mix ratio in
water are not recommended, as this will lead to
high engine operating temperatures.
•
A refractometer can be ordered from Atlas Copco
with part number 2913 0028 00.
TOPPING UP/REPLACING COOLANT
•
Verify if the engine cooling system is in a good
condition (no leaks, clean,...).
•
Check the condition of the coolant.
•
If the condition of the coolant is outside the limits,
the complete coolant should be replaced (see
section Replacing the coolant).
•
Always top-up with PARCOOL EG Concentrate /
PARCOOL EG.
•
Topping up the coolant with water only, changes
the concentration of additives and is therefore not
allowed.
Never remove the cooling system filler
cap while coolant is hot.
The system may be under pressure.
Remove the cap slowly and only when
coolant is at ambient temperature. A
sudden release of pressure from a heated
cooling system can result in personal
injury from the splash of hot coolant.
In case of a mix of different coolant
products this type of measurement
might provide incorrect values.
Summary of Contents for XRVS 1300 CD7
Page 2: ......
Page 20: ... 20 PNEUMATIC REGULATING SYSTEM AR RV CEhp CElp BOV TV UA ...
Page 95: ...Dataplate 95 ...
Page 100: ... 100 ...
Page 101: ......
Page 102: ......