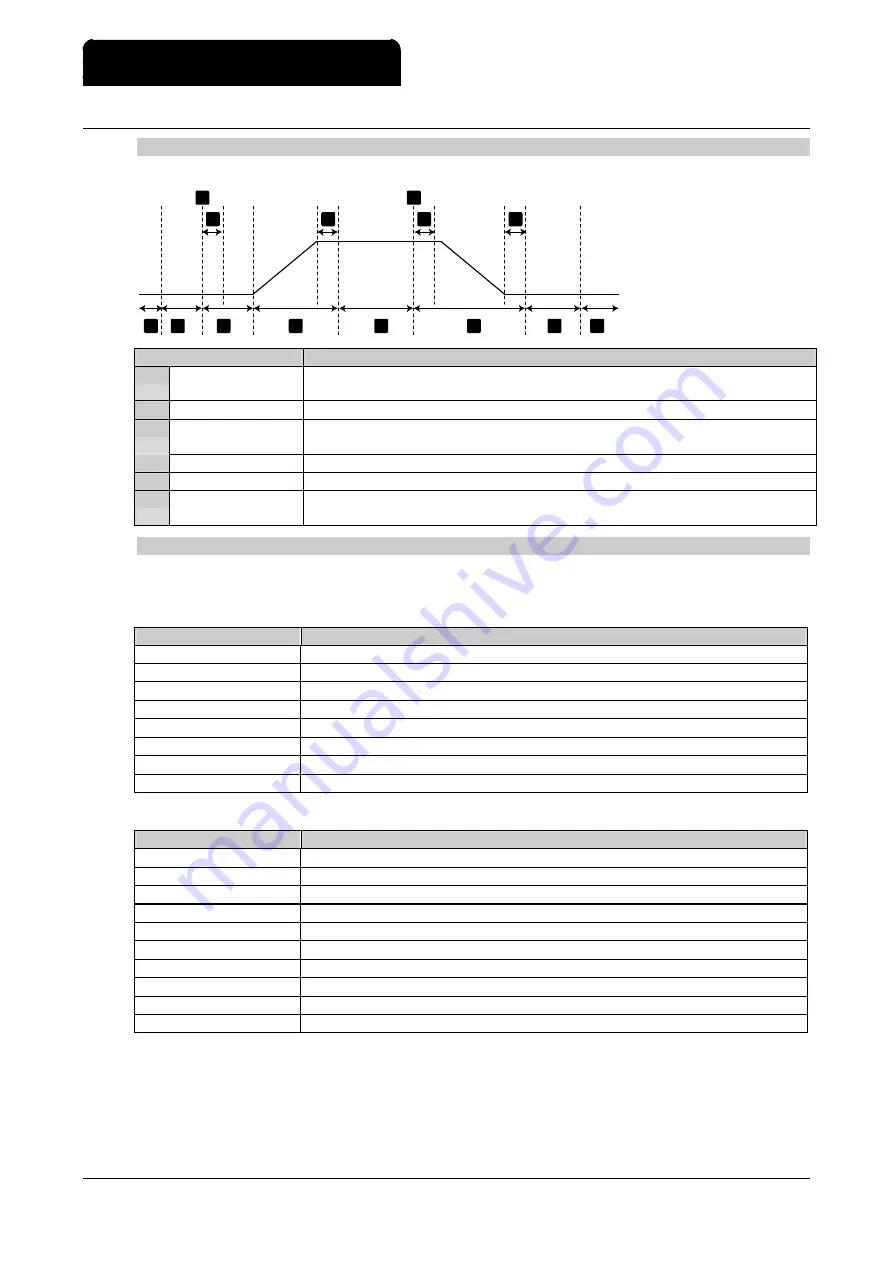
OPERATION
Page 50
MVS User Manual
710-13019-00A
9.3
Operating States
Start and Run States
The MVS soft starter has six operating states, and performs the following actions in each state:
State
Starter actions
1 Not ready
Control power is on and the starter performs system checks. The starter may be waiting
for the motor to cool before allowing a start.
2 Ready
The starter is initialised and waiting for a start command.
3 Pre-start checks
A start command has been received (a). The main contactor closes (b) and the starter
performs connection checks.
4 Starting
The starter ramps the SCRs up to full conduction and closes the bypass contactor (c).
5 Running
The motor is running normally.
6 Stopping
A stop command has been received (d). The starter opens the bypass contactor (e), ramps
the SCRs down to no conduction, then opens the main contactor (f).
Trip States
The starter's response to a trip depends on the starter's state when the trip occurs.
Trip while starting (bypass contactor not yet closed)
State
Function
Not Ready
Perform system checks.
Ready
Wait for start command.
Start command received
Main contactor closes.
Pre-start checks
Perform connection checks.
Starting
Ramp up SCR firing angles.
Trip command
Turn SCRs off then open main contactor.
Tripped
Wait for reset command.
Reset command received
Trip cleared and starter returns to Not Ready state or Ready state.
Trip while running (bypass contactor closed)
State
Starter action
Not Ready
Perform system checks.
Ready
Wait for start command.
Start command received
Main contactor closes.
Pre-start checks
Perform connection checks.
Starting
Ramp up SCR firing angles.
Full conduction
SCRs at 100% conduction. Verify current is < 120% FLC then close bypass contactor.
Running
Normal motor run state (bypassed mode).
Trip command
Open bypass contactor. Turn SCRs off then open main contactor.
Tripped
Wait for reset command.
Reset command received
Trip cleared and starter returns to Not Ready or Ready state.
Instantaneous Overcurrent Stage 2 trip
The main contactor opens immediately, regardless of the starter's state.
0
7717.A
3
2
1
4
6
5
b
a
d
c
f
e
1
2