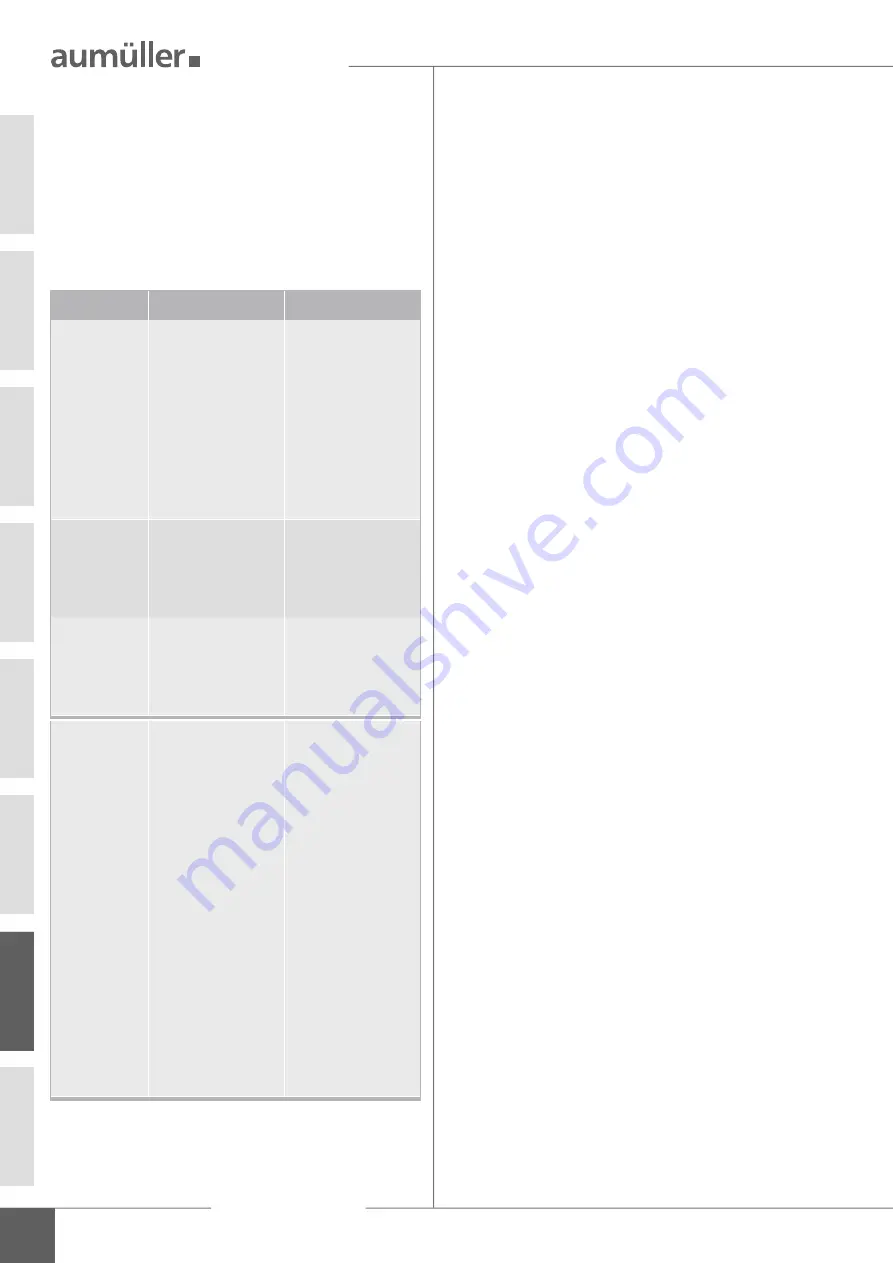
26
Assembly Instruction
OFV1
Problem
Possible causes
Possible solutions
Locking drive
does not start
• Duration of mains
power supply too short
• Drive run direction from
the opening drive is not
correct
• Connecting cable not
connected
• DIP switch is wrong
setting
• Adjust supply voltage
as specified in the
technical documen-
tation
• Check drive cables
change polarity
• Check all connection
cables
• Setting the DIP switch
properly
Opening drive
does not ope-
rate correctly
• DIP switch is wrong
setting
• Setting the DIP switch
properly
• If the locking drive is
connected to an
USKM
,
DIP switches
3
and
4
must be set to
ON
Locking drive
does not unlock
in direction OPEN
and/or does not
lock in direction
CLOSED
• DIP switch is wrong
setting
• Setting the DIP switch
properly
LED-1 red
LED-1 red
blinking
LED-1 blinking
red / green
LED-2 OFF
•
OFV1
fault
short circuit / cable break
in the drive line
or
defect in the electronics
• opening drive fault
DIP 3 = OFF
opening drive is turned
off due to voltage over-
overload - caused by
short circuit in the drive
line or
defect in the electronics
DIP 3 = ON
opening drive is shut off
due to undervoltage -
caused by cable break
in the drive line or
defective opening drive
• power supply is <19 V
• none power supply
• Check the connection
form the
OFV1
and
check the
OFV1
• Check the connection
from the opening drive
and check the opening
drive
• correct power supply
• Check the connection
m
aintenanCe
anD
rePair
h
eLp
in
case
OF
m
aLFunctiOns
, r
epairs
and
m
aintenance
Professional repair of a defect drive can only be performed at the
manufacturer’s factory or manufacturer-certified specialist company.
Unauthorized opening or manipulation of the drive terminates warranty.
1. Exchange defect drives or have them repaired by the manufacturer.
2. In case of problems during installation or normal operation the
following table might be useful:
m
aintenance
and
mOdiFicatiOn
To ensure continuous function and safety of the drive periodic maintenan-
ce by a specialist company is required at least once a year (as mandated
by law for smoke and heat exhaust systems). Operational readiness must
be checked regularly. Frequent inspection of the system for imbalance
and signs of wear or damages of cables and fastening elements must be
performed.
During maintenance contaminations must be removed from the drive.
Fastenings and clamping screws must be checked for tightness. Test runs
during the opening and closing procedure of the devices must be per-
formed.
The drive itself is maintenance-free. Defect devices may only be repaired
in our factory. Only replacement parts of the manufacturer may be used.
When the connection cable of this device is damaged it must be replaced
by the manufacturer or his customer service or a similarly qualified per-
son to avoid endangerment.
It is recommended to conclude a maintenance contract. A sample main-
tenance contract can be downloaded from the homepage of
Firm Aumüller Aumatic GmbH
(
www.aumueller-gmbh.de
).
While cleaning the windows, drives may not have direct contact with
water or cleaning agents. Drives must be protected from dirt and dust
during the construction phase or renovations.
Maintenance process
1.
Open or extend power-operated casement completely.
2.
Completely disconnect the system from the mains and secure it
against automatic or manual activation.
3.
Check windows and fittings for damages.
4.
Check all mechanical fastenings (if required, observe information on
torques in installation instructions).
5.
Check electric drives for damages and contaminations.
6.
Check connecting cables (drive cable) for:
- tightness of the cable screw
- functionality of the strain relief
- damages
7.
Check the mobility of hinges and fittings and re-adjust or apply
lubricant, e.g. silicone spray (observe the instructions of the manu-
facturer of this window system).
8.
Check peripheral seal, remove contaminations or replace.
9.
Perform cleaning to maintain functionality (e.g. clean extending
elements of the drive, such as chains or spindles by damp wiping them
with acid or lye-free agents and drying them and, if required, lubricate
them with cleansing oil e.g., Ballistol).
10.
Turn on operating voltage.
11.
Open and close the power-operated window via the operating
voltage (functional test).
12.
If available, check and re-adjust protection systems of the safe guard
fixture.
13.
Check the intactness of the CE label at the power-operated system
(e.g. SHEV/Natural smoke and heat exhaust ventilators).
14.
Check the intactness of warning instructions and labels at the
respective drive.
15.
Perform a risk assessment in accordance with Machinery Directive
2006 / 42 / EG, if required, e.g. after modifying the machine.
07