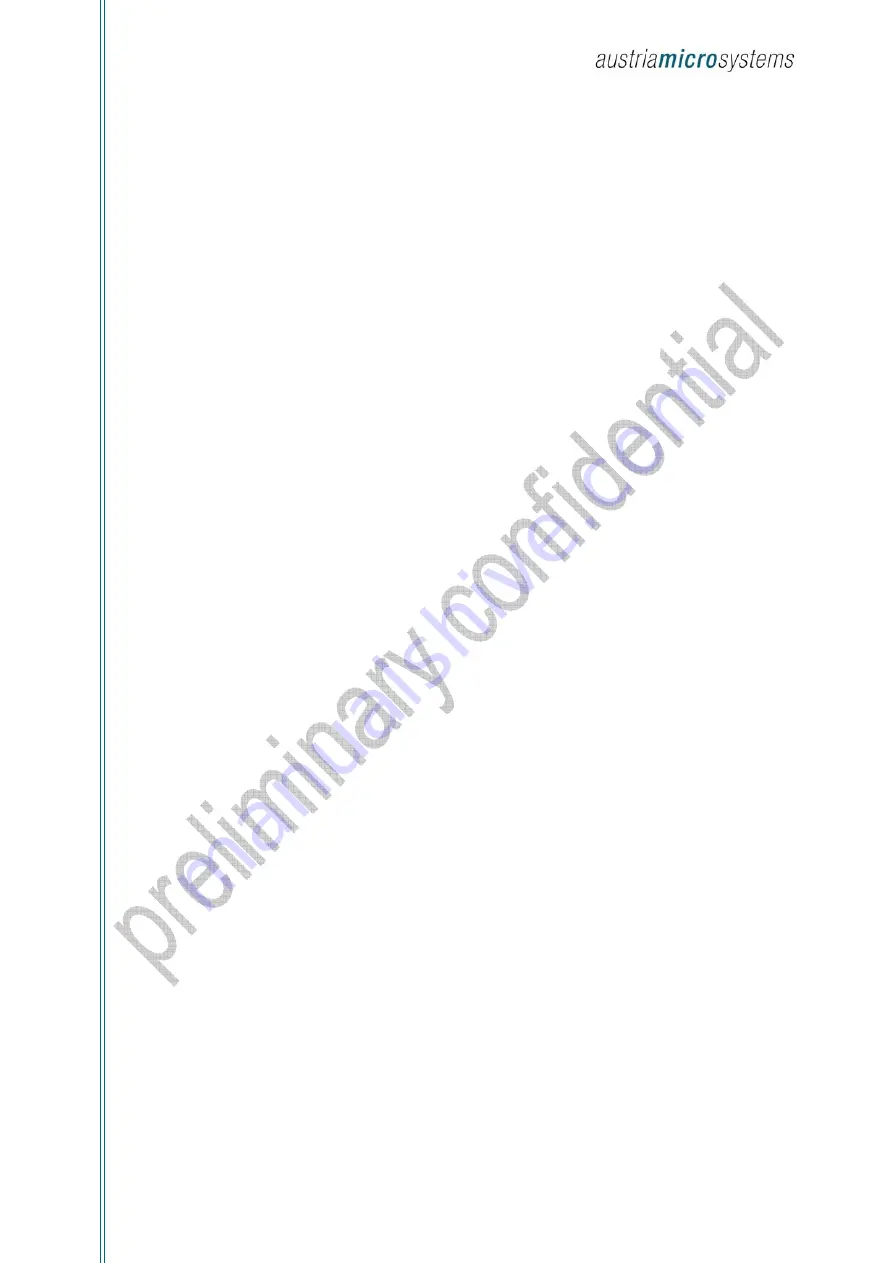
AS5130 8 bit high speed magnetic rotary encoder
Demoboard Operation Manual
Revision 1.0, 01-June-08 www.austriamicrosystems.com
Page 6 of 7
3.1.2
AS5130 Encoder
The AS5130 (U4) is running with the 5V source. The resistor R27 (0R) can be removed if the user wants to use his own
power supply for his own tests.
The SSI serial interface (DIO, CS, DCLK) is controlled by the microcontroller U5.
The LED D7 is directly connected to the AS5130 on the MagRngn pin on one side, and on U5 for the other side to make it
blinking if MagRngn = 5V (magnet too far away).
The PWM LED is directly connected on the PWM signal of U4.
The Test3..0 signals are connected to U5 but are not used.
3.1.3
Microcontroller
The microcontroller PIC 18F4550 (U5) from Microchip includes an on-chip USB interface.
The U1 switch enables the bootloader mode of the microcontroller, if pressed during power up.
In normal mode, pressing the switch makes the microcontroller writing the zero position value into the active AS5130.
The connector U7 is used for ISP programming of the microcontroller only.
3.1.4
J4 connector for external AS5130
An external AS5130 device can be wired to this connector. It allows the user to test his own board, and/or fuse the
configuration bits for the mass production.
•
Pin 1: ePROG.
Is the 8.5V source for fusing. The high voltage is switched only during the programming phase.
•
Pin 2: eCS
Is an independent CS signal provided by the microcontroller, only for the external sensor
•
Pin 3: eDIO
Is the same signal as DIO used for the on board sensor. Both are connected through the R14 resistor (0R). Only
one sensor, on-board or external, can be selected at the same time with the CS and eCS signal.
•
Pin 4: eDCLK
Is the same signal as DCLK used for the on board sensor. Both are connected through the R46 resistor (0R). Only
one sensor, on-board or external, can be selected at the same time with the CS and eCS signal.
•
Pin 5: 5V
Is the power supply of the external sensor
•
Pin 6: 3.3V
Not
used
•
Pin 7: VSS
•
Pin 8: eVOUT
Analog input. Not used
4
Troubleshooting
When operating the demo board and software it is advisable to proceed as:
•
Running the demo software
Before starting the demo software the demo board needs to be connected to the USB port of the PC.
1.
Connect to the USB port.
2.
Start the software.
•
Closing the demo software
After finishing the work with the demo board the software needs to be closed before disconnecting the demo board.
1.
Close the software.
2.
Disconnect from the USB port.
ams
AG
Technical
content
still
valid