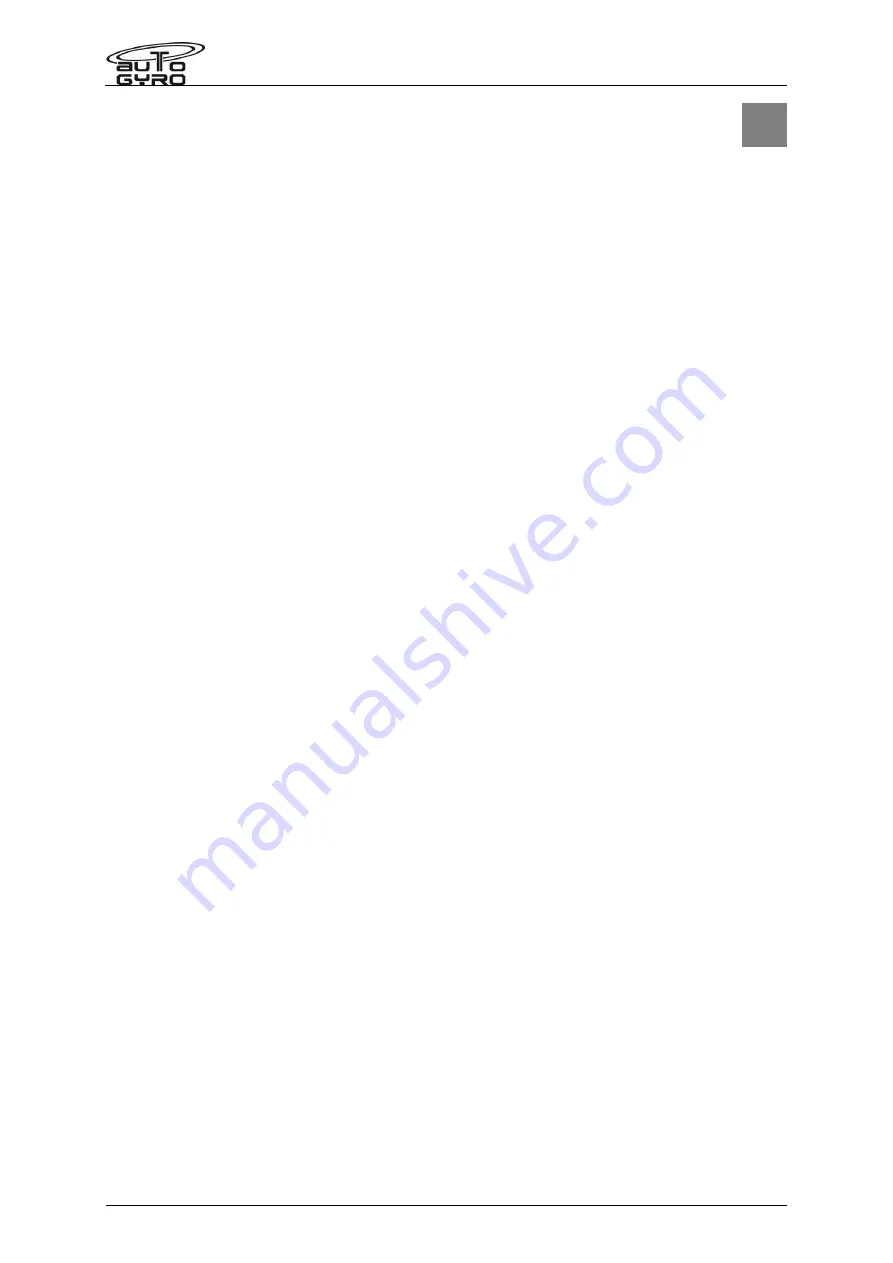
Manufacturer
Maintenance Manual
AutoGyro
MTOsport
MMM-CV-E_16-06-13
Part E - 07-00-00 2-2
Page 1 of 1
07-00-00 2-2 JACKING OF THE GYROPLANE
LNE
GENERAL, REFERENCES AND REQUIREMENTS
Task may only be performed by an organization or individual trained and entitled to do 'Line Maintenance'!
Secure gyroplane against unauthorized or unintended operation!
Gyroplane must be placed on level ground and restrained (blocks, chocks)
SPECIAL TOOLS AND CONSUMABLE MATERIALS
None
PRECAUTIONS AND SAFETY MEASURES
PROCEDURES
Unload nose gear
1
In order to unload the nose gear, load or lash-down keel tube in most aft position until gyroplane rests safely
on both main wheels and keel tube.
Unload main gear
2
In order to unload one of the main wheels carefully jack the gyroplane at the keel tube.
3
Let the gyroplane tip to the desired side and continue to jack slowly until the gyroplane rests stable on nose
wheel, one main wheel and jack.
NOTE: Sand bags or load may be used to add additional weight on the desired side.
4
Secure gyroplane adequately before commencing work and do not leave unattended in jacked position.
Summary of Contents for MTOsport
Page 1: ...Manufacturer Maintenance Manual Line Maintenance ...
Page 2: ......
Page 88: ......
Page 90: ......
Page 96: ......
Page 98: ......
Page 100: ......
Page 110: ......
Page 112: ......
Page 116: ......
Page 134: ......
Page 138: ......
Page 164: ......
Page 166: ......
Page 170: ......
Page 172: ......
Page 176: ......
Page 178: ......
Page 180: ......
Page 184: ......
Page 190: ......