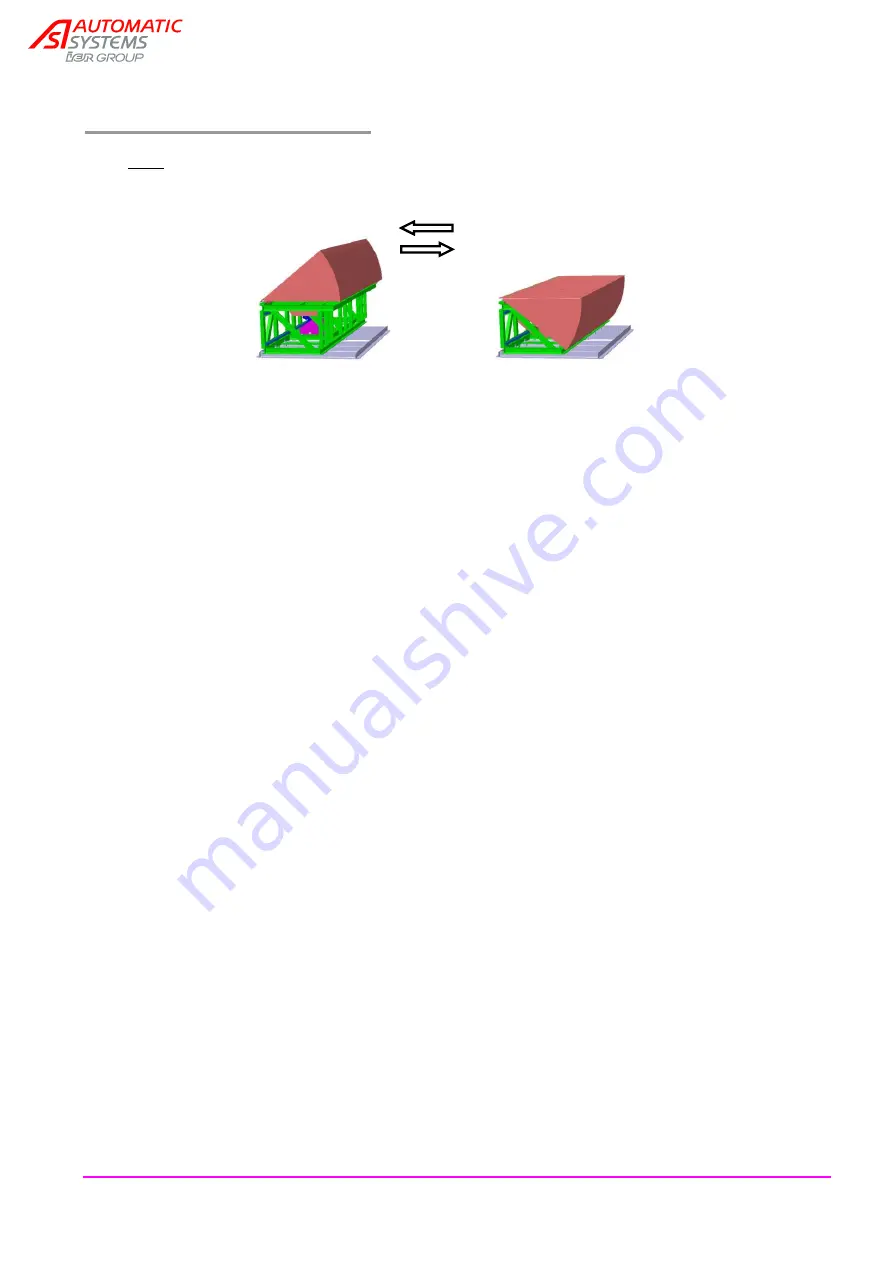
The informat ion conta ined in th is docu ment is the property of Automatic Syst ems and is conf ident ial . The recip ient shall refr ain from us ing it for any purpose
other than the use of the produ cts or t he e xecut ion of the projec t to wh ich it refers and from commun icat ing it to th ird parties w ithout wr itten pr ior agree m ent
of Automat ic Systems.
RSB76E-MT-EN
p. 7/33
2.2. Operating Principle
Note
: the obstacle is said to be
closed
when it is in the raised position (=> passage clos ed);
the obstacle is said to be
open
when it is lowered (=> passage free).
The opening
of the obstacle (3, p5) can be activated by a pushbutton box, presence sensors
(electric cells or inductive loops burie d under the roadway) or by an external device, e.g. card
reader (options).
The closing
is activated in the same way, or automatically at the end of a time -out.
The RSB can be operated as opening in both directions of passage, with, in this case,
automatic
permutation of the
opening and closing
sensors
(see p12).
The RSB will go
out of service
if its movements have not completed within the given time or if
it fails to close after several attempts.
The presence
sensors
(loops/cells) also make it possible to open, to stop immediately, to
reopen or close the obstacle in the event of detection of a user in the vicinity of the equipment.
→
The use of these presence sensors is strongly recommended by Automatic Systems!
The RSB is combined with a
traffic light,
which goes from red to green only when the obstacle
is completely open (opening limit switch reached). Upon the closing command, the light returns
to red before any movement of the obstacle.
Safety can be still further increased by cou pling the RSB with a Rising Barrier (see p 12).
The movement of the obstacle is transmitted from a
gear motor
to a
linear actuator
by a belt
and an endless screw.
A pre-loaded
spring
balances most of the weight of the obsta cle: it reduces the effort required
by the linear actuator when the obstacle is being raised and reduces its speed of descent.
The speed of the obstacle, controlled by a
variable speed controller
(26, p6), is adjustable
both on opening and on closing. The movements are parameterised in the factory to offer a
sharp acceleration and a soft deceleration at the end of the movement .
When the obstacle is descending, the engine functions as a generator and sends the current to
the variable speed controller. To prevent any damage to the latter, this current is automatically
dissipated into a
resistance
via the
braking
module
(24 and 25, p6).
An electric brake
locks the obstacle in the up or down position, by me chanically blocking the
motor’s axis.
In the event of an out-of-service condition or a voltage drop following a dysfunction, the RSB is
stopped and locked (equivalent to a Stop command). It can however be unlocked and
operated manually
(see p17).
At rest, the motor is kept under light voltage in order to create a little heat and to limit
condensation on the motor and the linear actuator.
A water level
detector
(6, p5) enables the equipment to be put out of service in the event of
the presence of water in the pit, fatal for the working of the motor. An alarm message is then
sent to the control board’s display unit (22, p 6) and a signal to the terminal strip (20, p 6) with
RSB closed
RSB open
direction B
direction A