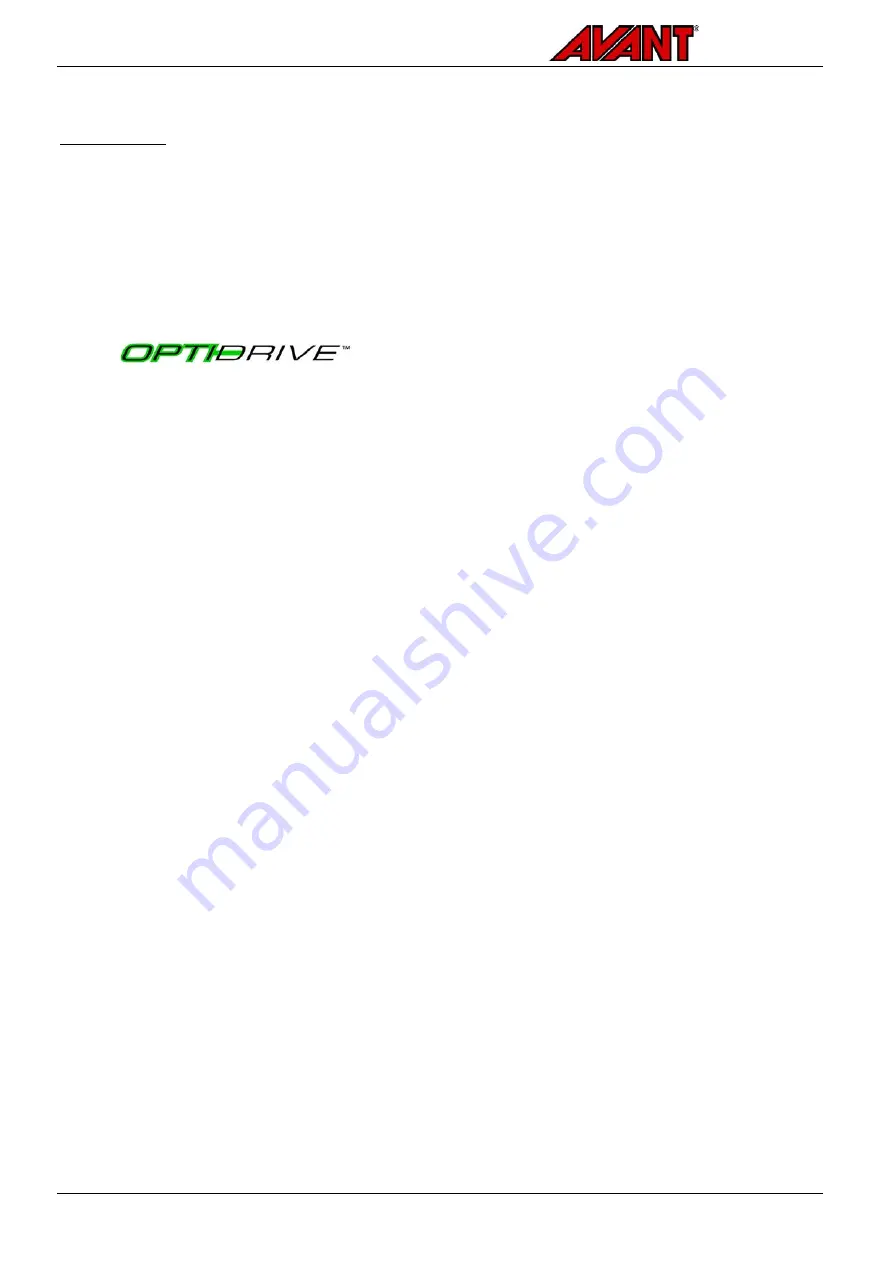
Operating instructions
Avant 850
76
.
OptiDrive®
The 850 loaders are equipped with the efficient
Avant OptiDrive
®
hydraulic drive system as standard.
The system is designed for optimal hydraulic oil flow,
which helps to conserve energy by minimising
losses. This is achieved with the use of integrated
high efficiency Avant valve blocks and EO3 type
hose fittings.
.
..
When you want to have a high pulling force:
1.
Choose low speed range
2.
Use high engine rpm
3.
Press the drive pedal only lightly to select slow
drive speed. This way the full output of the
hydraulic system and the engine can be used
for high pulling force.
If the engine is overloaded while pushing, the
pedal shouldn't be pressed further. Instead, use
higher engine revs and push the pedal only a
little.
Summary of Contents for Avant 850
Page 1: ...English Operator s Manual 2020 A441827EN 2020 1 2020 www avanttecno com...
Page 128: ...Avant 850 128...
Page 132: ...Avant 850 132 Notes...
Page 133: ...Avant 850 133 Notes...