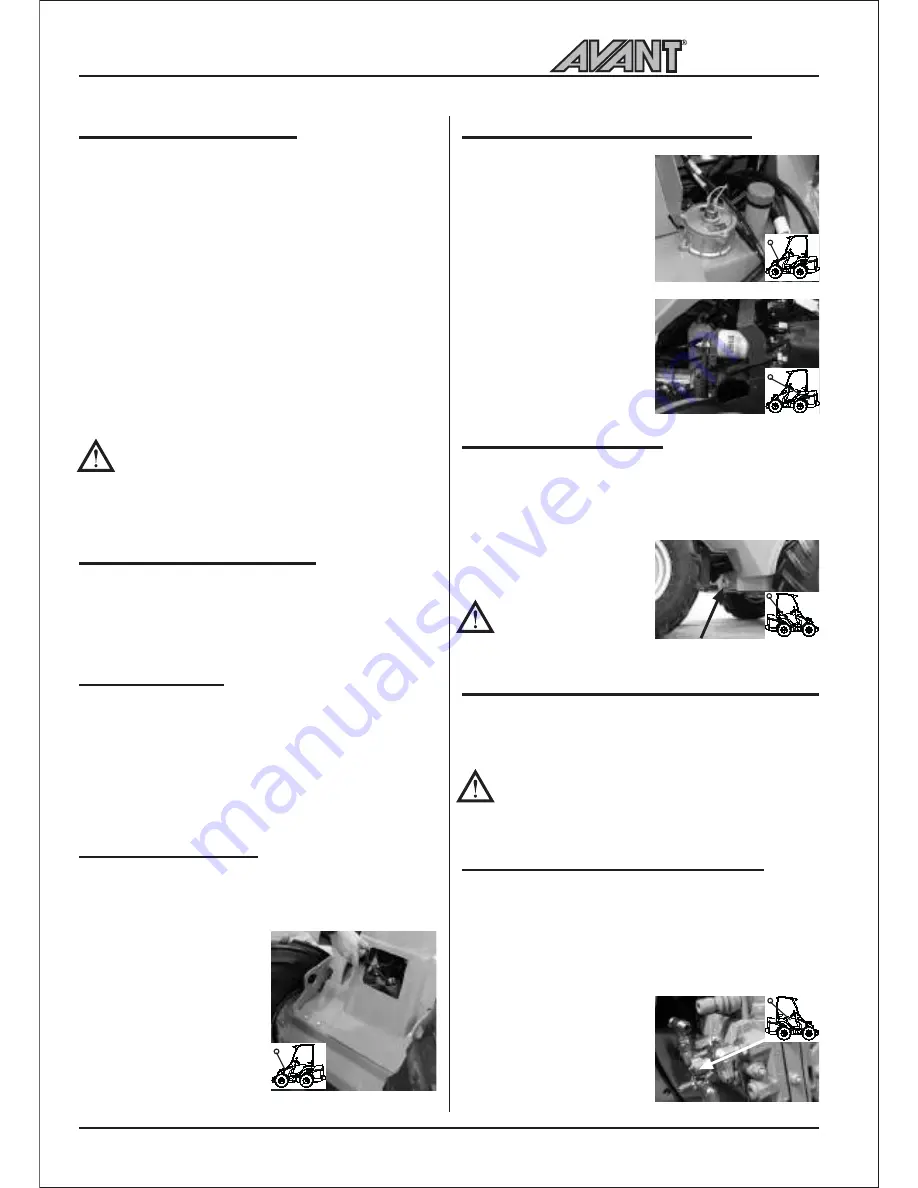
2. Cleaning of the loader
Cleanliness of the loader is not only a question of
outer appearance. All surfaces, painted and others,
will stay in better condition when they are cleaned
regularly. A clean machine also lasts longer. A dirty
machine will run hotter and will collect dirt into the
air cleaner, which is likely to damage the engine. Pay
special attention to the cleanliness of the engine, the
oil tank cover, the engine compartment and the
hydraulic pump compartment.
The loader can be washed with a pressure washer.
However, avoid direct spraying on hydraulic
components (hoses, cylinders) and decals. After
washing grease all greasing points, also the attachment
coupling plate and locking pins.
The loader is equipped with a hydraulic oil
cooler, which is located in the front frame on
the right side, make sure to clean the oil cooler
cell with compressed air every time you are
servicing the loader - and even more frequently
if the loader is being used in dusty conditions.
Take off the right side cover plate before
cleaning the oil cooler.
3. Greasing of the machine
Greasing of pivot points is very important in order to
avoid wear. Most of the greasing points are on the
loader boom. The picture on page 31 shows the
location of grease nipples.
4. Battery check
In order to secure the starting and safe operation the
battery of the loader must be checked regularly.
Checking the electrolyte level of the battery happens
by opening the filler caps.
NOTICE:
Clean the
battery before opening the caps so that dirt
cannot get in the battery.
Check also the contacts
and clean if necessary.
5. Hydraulic oil level
Hydraulic oil level can be checked with the dipstick
in the filler. Oil level should be at the lower mark of
the dipstick when the loader boom is up. Refill when
necessary. Do not let any
contaminents enter the
hydraulic oil tank during this
procedure. There is a
breather filter inside the
dipstick cap which should
be cleaned or changed once
a year.
Remember to use the
service support (page
26).
6.Changing of hydraulic oil filters
The hydraulic oil return filter
is located on top of the
hydraulic oil tank, under the
front cover. Take off the
cover and replace the oil
filter cartridge.
Remember to use the
service support (page 26).
The hydraulic pressure filter
is located in the back frame
beside the hydraulic pumps.
When unscrewing the filter
hold the screw in the
housing with a 12 mm allen
key and replace the filter.
7. Hydraulic oil change
When changing hydraulic oil, the oil can be removed
with a suction pump or by opening the drain plug on
the right side of the front frame, next to the articulation
joint. In both cases it is important to clean the magnetic
drain plug. Hydraulic oil tank
capacity is 38 litres. Use ISO
VG-46 certified mineral
hydraulic oil.
Use of synthetic
hydraulic fluids is not
allowed.
8. Check and tightening of bolts, nuts and fittings
Check tightness of bolts, nuts and hydraulic fittings
regularly.
NOTICE: Tighten wheel nuts after first 5
operating hours. Check tightness of wheel
nuts regularly. Wheel nuts shall first be
tightened to 120 Nm diagonally opposite
and finally tightened to 140 Nm.
9. Check pressure of hydraulic system
Pressure checking points and pressure settings for
different functions are as follows:
Boom lifting:
Pressure is checked from the
manometer fitting which is mounted on the main
control valve (or from the quick coupler of rear
auxiliary hydraulics if the machine is equipped with
rear aux. hydraulics outlet.)
Pressure is measured with
full engine revs and by
turning e.g. the bucket tilt
control to end position.
Pressure setting should be
240 bar.
Service and maintenance instructions
28
700 Series
https://tractormanualz.com