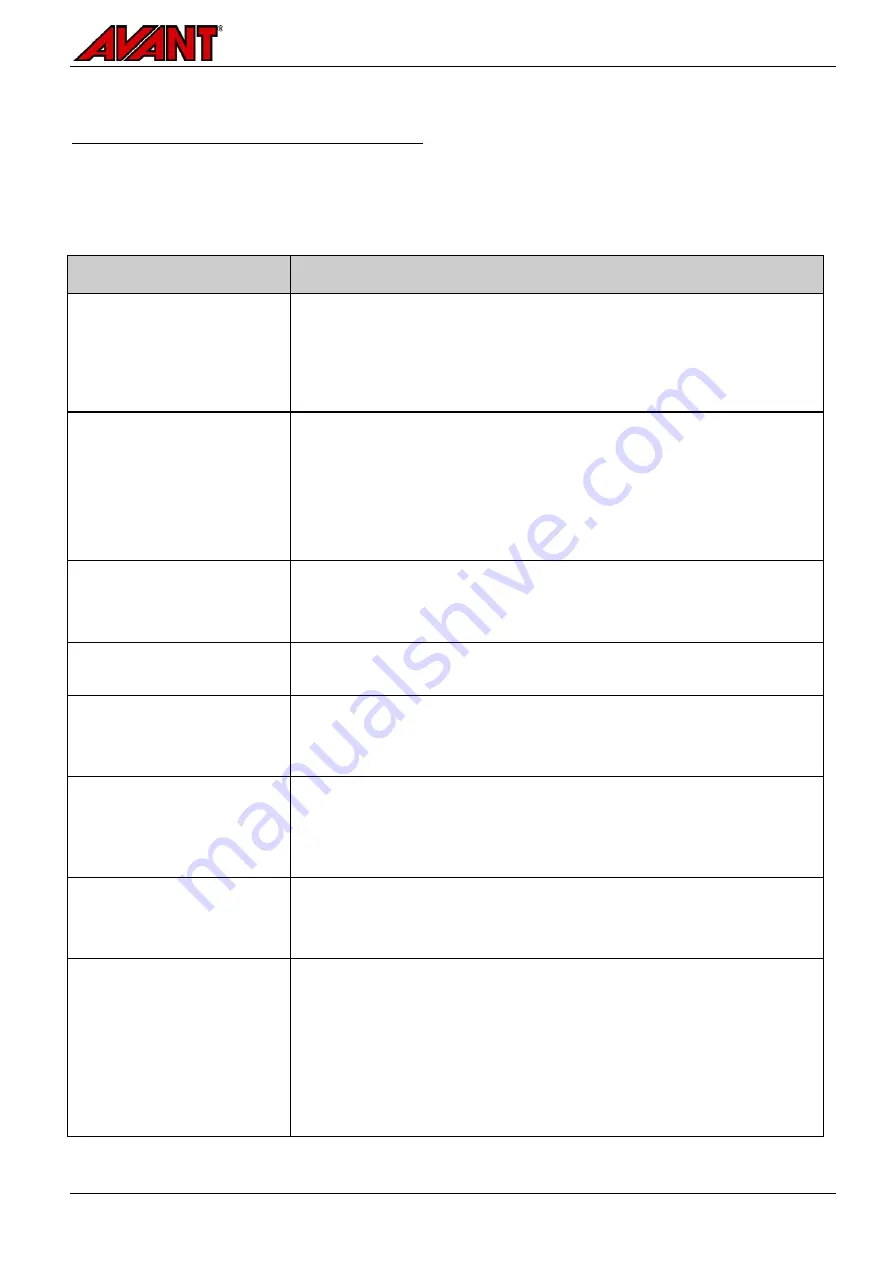
Avant 735
Lift capacity
45
.
How to estimate actual lifting capacity
The actual tipping load and stability of the loader depends on many factors that you must consider when you
handle heavy loads or attachments. Listed in the table below are many factors that influence the stability of the
loader.
Always keep in mind the conditions listed in the following table.
Influencing factor
How you should take it into account
Position of the loader boom
and telescope
Keep load as close to the ground as possible while you drive. Lift only when
ready to unload the bucket or attachment
See load chart and ROC table to estimate the lift capacity of the loader on
level ground. Reduce the indicated maximum load by always taking the
local operating conditions into account
The total load on the loader
boom
Estimate the combined weight of an empty attachment and load
Load chart is based on weight of pallet forks (90 kg)
If the attachment you use is heavier, subtract its weight from the listed
tipping load accordingly
See the operator's manual of each attachment for attachment weight and
possible information about permitted loads.
The distance of the load
from the front tyres
The further away the load is from the loader, the less stable the loader is
Keep the load as close to the ground and the loader as possible
Never drive while load is lifted more than just off the ground
Straight or articulated
position of the loader frame
If you turn the articulated frame, the loader will tip over more easily
Keep the loader in straight position when lifting heavy loads
Levelness of the ground
All listed values are applicable only on level, even ground
Drive slowly on uneven ground
Keep load close to ground and as close to the loader as possible
Installed counterweights
If counterweights are installed, the loader stability is better
Keep standard counterweights fitted
Consider the use of additional counterweights or ballasted tyres for
additional stability
Driver presence
Driver acts as additional counterweight
Load chart is calculated with a 75 kg driver present on driver's seat
If you leave the driver's seat, loader can tip forward.
Movements of the loader
and the load
Lifting of the maximum load is possible only when loader is not moving
Operate the controls of the loader slowly and in a smooth manner.
Dynamic loads can cause loader to tip over
Secure load on the attachment. If load moves or swings, the loader can tip
over
Use correct type of attachment for each type of load
Never lift swinging loads
Summary of Contents for 735 2020
Page 1: ...English Operator s Manual 2020 A442134EN 2020 1 2020 www avanttecno com ...
Page 130: ...Avant 735 130 ...
Page 134: ...Avant 735 134 Notes ...
Page 135: ...Avant 735 135 Notes ...