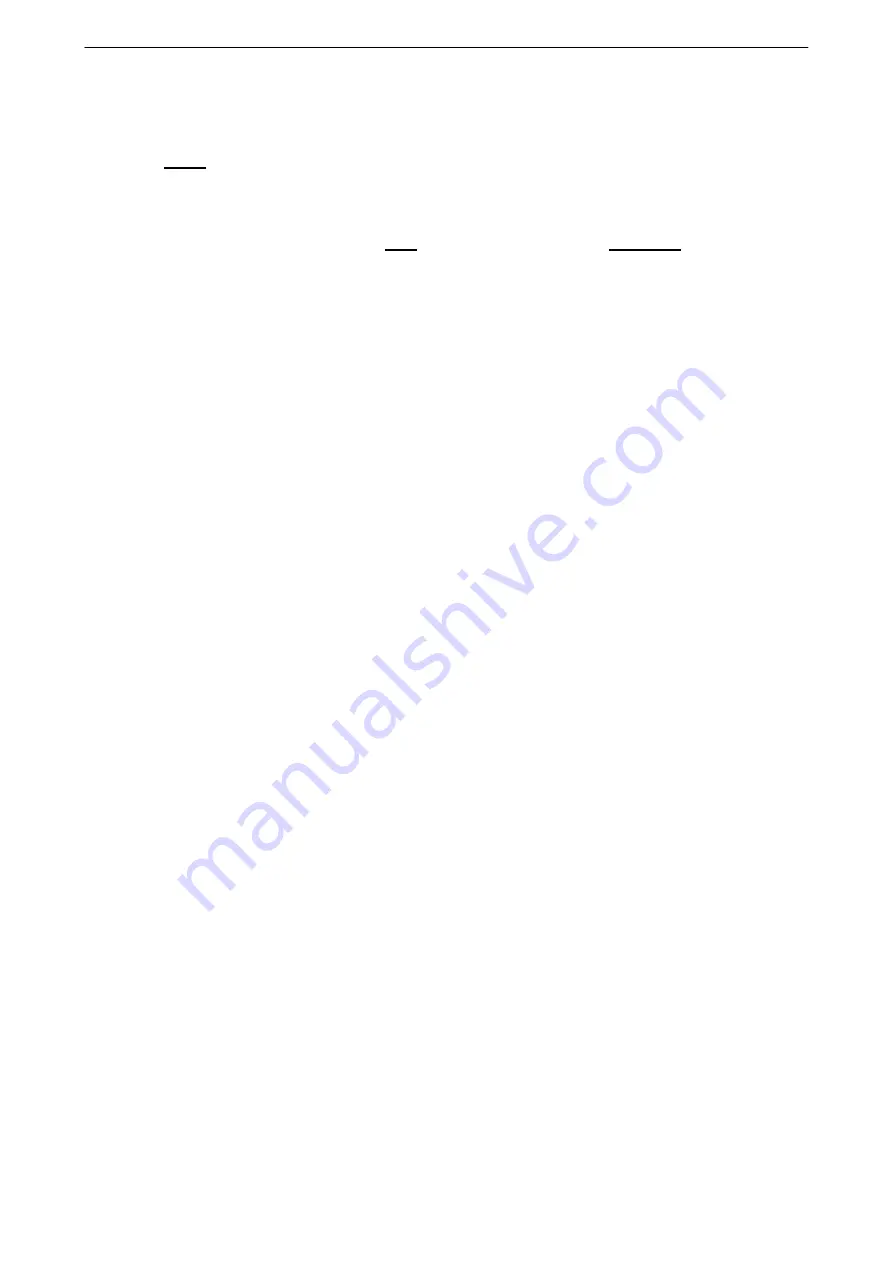
EN-1320
OPERATION AND INSTALLATION MANUAL
7.4.2.5.
Drilling holes for use with the AN3-( ) type bolts with self-locking nuts is acceptable.
NOTE:
Chadwick-Helmuth Manual AW-9511-2, „The Smooth Propeller„ specifies several generic
bulkhead rework procedures.
7.4.2.6.
All hole/balance weight locations must take into consideration, and must avoid, any possibility
of interfering with the adjacent airframe, de-ice and engine components.
7.4.3. PLACEMENT OF BALANCE WEIGHTS FOR DYNAMIC BALANCE
7.4.3.1.
The acceptable method of attachment of dynamic balance weights is to add the weights to the
spinner bulkhead to existing static balance weights.
7.4.3.2.
Record the number and location of dynamic balance weights, and static balance weights if
they have been reconfigured, into the Propeller logbook. Subsequent removal of the dynamic
balance weights, if they exist, will return the propeller to its original static balance condition.
The static balance weights are allowed to remove, if effective.
7.4.3.3.
Use only stainless washers or plated steel washers as dynamic balance weights on the
spinner bulkhead.
7.4.3.4.
Do not exceed maximum weight per location of 32 g. This is approximately equal to eight
AN970-3 style washers.
7.4.3.5.
Weights are to be installed using aircraft quality 10-32 inch screws bolts.
7.4.3.6.
Balance weight screws attached to the spinner bulkheads must protrude through the
self-locking nuts a minimum of one thread and a maximum of four threads.
7.4.3.7.
All propellers which have been dynamically balanced must install a decal on blade no. 1. This
will alert repair station personnel that the existing balance weight configuration may not be
correct for static balance.
7.5. BLADE REPLACEMENT IN THE FIELD
7.5.1.
Remove the blade from the hub.
7.5.2.
Install the new blade into the hub per Installation and Operation Instruction section in this
manual.
7.5.3
. The blades for each propeller are precisely matched. Subsequent replacement of one or more
blades in the field and setting the new blade in the same position as was the original blade, can
cause mismatch of the blades resulting in aerodynamic unbalance. To prevent this, follow
these steps:
a) Using the feathering pump, move the propeller to the low pitch. If the feathering pump is not
installed, start the engine and stop it with the propeller at the low pitch.
b) Using a protractor, measure the angle of all blades at the reference station. The reference
station is marked with red line on the blade face side.
61-10-20
MAINTENANCE
Page 7-2
2017-10-06