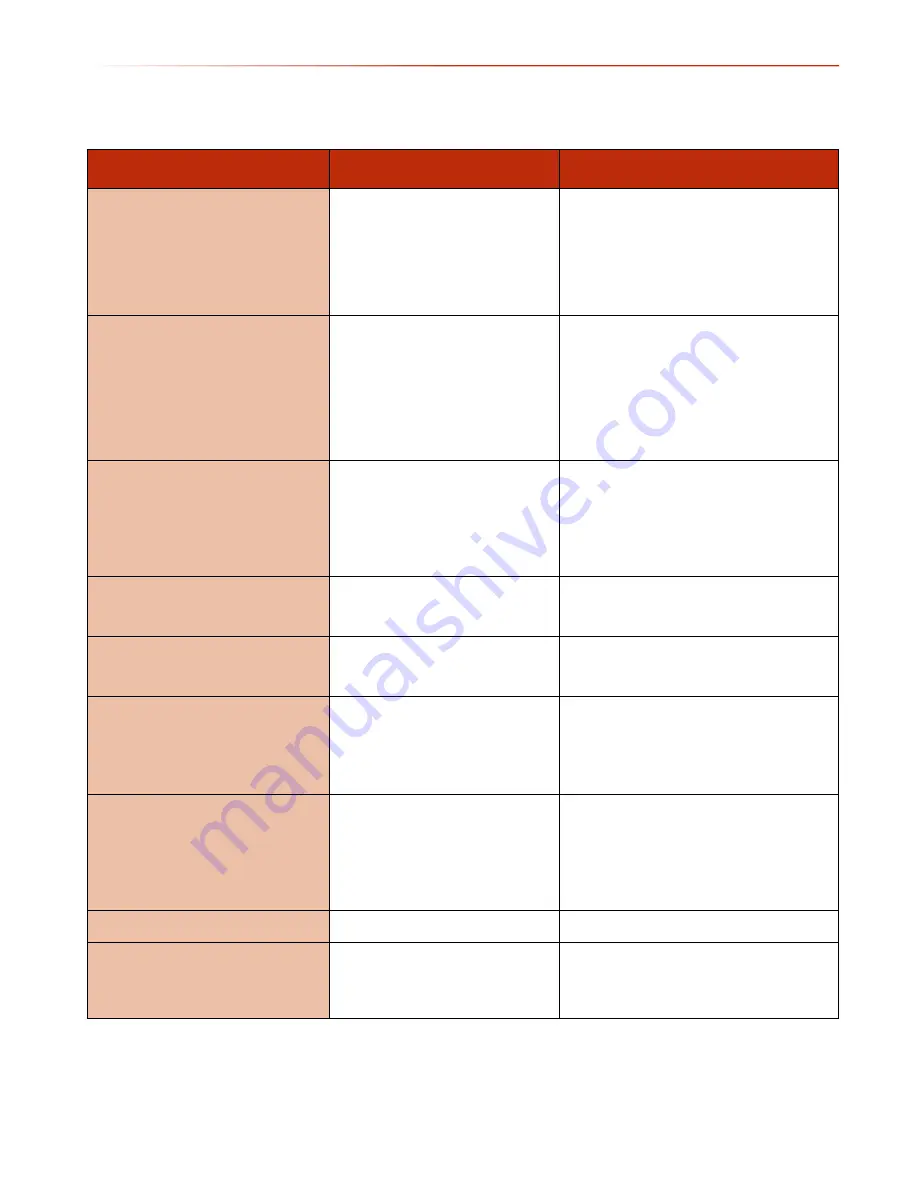
Troubleshooting
23
TROUBLE
PROBABLE CAUSE
REMEDY
Noisy Operation
1. Incorrect belt tension
2. Dry spindle
3. Loose spindle pulley
4. Loose motor pulley
1. Adjust the tension
2. Lubricate spindle
3. Checking tightness of
retaining nut on pulley,
and tighten if necessary
4. Tighten set screws in pulleys
Drill bit burns
1. Incorrect speed
2. Chips not coming out of hole
3. Dull drill bit
4. Feeding too slow
5. Not lubricated
1. Change speed
2. Retract drill bit frequently
to clear chips
3. Resharpen drill bit
4. Feed fast enough-allow drill
bit to cut.
5. Lubricate drill bit
Drill bit leads off hole not round
1. Hard grain in wood or lengths of
cutting lips and/or angles not equal
2. Bent drill bit
1. Resharpen drill bit correctly
2. Replace drill bit
Wood splinters on underside
1. No “back-up material” under
workpiece
1. Use “back-up material”
Workpiece torn loose from hand
1. Not supported or clamped
properly
1. Support workpiece or clamp it
Drill bit binds in workpiece
1. Workpiece pinching drill bit
or excessive feed pressure
2. Improper belt tension
1. Support workpiece or clamp it
2. Adjust tension
Excessive drill bit runout or wobble
1. Bent drill bit
2. Worn spindle bearings
3. Drill bit not properly
installed in chuck
4. Chuck not properly installed
1. Use a straight drill bit
2. Replace bearings
3. Install drill bit properly
4. Install chuck properly
Quill returns too slow or too fast
1. Spring has improper tension
1. Adjust spring tension
Chuck will not stay attached to
spindle it falls off when trying to
install it
1. Dirty, grease or oil on the tapered
inside surface of chuck or on the
spindles tapered surface
1. Make sure all surfaces are free of dust
and grease
Summary of Contents for AHDP13B
Page 4: ...What s Included 4 1 2 3 4a 2c 4 ...
Page 5: ...What s Included 5 2b 2e 2d 2a 5 6 10 9 7 8 13 11 12 2f ...
Page 24: ...Exploded Diagram Parts List 24 AHDP13B Bench Pillar Drill ZQJ4113A ...
Page 26: ...Exploded Diagram Parts List 26 AHDP16B Bench Pillar Drill ZQJ4116Q ...
Page 28: ...Exploded Diagram Parts List 28 AHDP16F Floor Pillar Drill ZQJ4116A ...
Page 34: ...Wiring Diagram 34 ...
Page 35: ...CE Certificate 35 AHDP13B Bench Pillar Drill ZQJ4113A AHDP16F Floor Pillar Drill ZQJ4116A ...
Page 36: ...CE Certificate 36 AHDP16B Pillar Drill ZQJ4116Q ...
Page 37: ...CE Certificate 37 AHRD16B Bench Radial Drill ZQJ3116 AHRD16F Floor Radial Drill ZQJ3116A ...
Page 38: ...Notes 38 ...
Page 39: ...Notes 39 ...