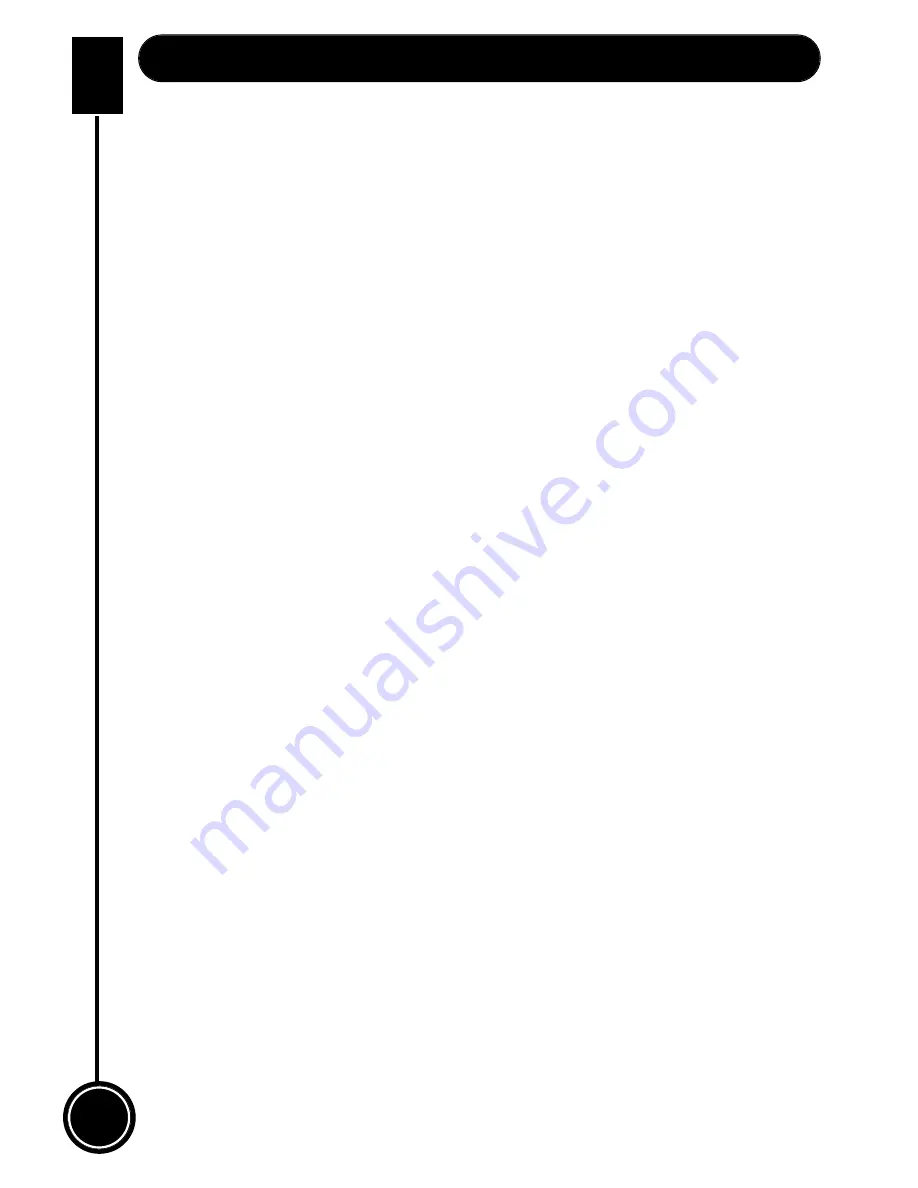
12
W H I T E
A X M I N S T E R
W
Parts Identification & Description...
Rise and fall
There is a housing machined on each side of the the Headbox support
mechanism
column which mounts a through shaft. A pinion gear is mounted on the
shaft inside the support column that meshes with a rack on the headbox.
Driving the pinion shaft will cause the headbox to rise and fall up and
down the headbox support column. The part of the shaft protruding from
the headbox has a hole through it to mount the operating lever.
Operating lever
This is the long arm which applies the down force to the chisel via the
(See fig 5)
headbox gearing. This consists of a tube,lever, which is mounted
through the rise and fall mechanism and clamped into place with a
capheadscrew. There is a grip sleeve that fits over the end of the lever
itself, to provide a firmer grip and some cushioning to the hand.
Base casting
This is a squat , hollow ‘T’ shaped casting which mounts all the
(See fig 6)
component parts of the morticer. The rear surface of the ‘T’ is machined
flat, with 4 No. M10 tapped holes whereby the Headbox Support column
is mounted. There are two raised slides machined across the front
section of the casting which accept the mounting slide of the work table.
There are housings machined in the base to support the traverse
mechanism, this consists of a pinion gear mounted on a shaft. The end
of the shaft protrudes through the front of the base. Into this shaft a
small lever handle is fitted to enable the shaft to be turned left or right.
This turns the pinion, which is engaged with a rack fixed to the mounting
slide, and causes the slide to be driven from side to side. Drilled and
tapped into the end of the rear slide rail (on each side) is a hole which
allows the distance stop rod to be mounted. (See fig 4a)
Morticing table
This is the casting that interconnects the worktable to the base, and
(See figs 5,5c,6)
enables the transverse and X-feed movements. It has two pairs of slides
machined into it, the lower pair engage with the slides on the base
casting. The upper pair are at right angles to the lower pair and are
machined to accept the slides machined into the underside of the
worktable. In both cases the fit between the slides is maintained by gybe
strips. The lower section of the casting has a rack mounted to it which
forms part of the transverse movement mechanism, (with the pinion gear
in the base). The front upper section has a housing with a drilled and
tapped hole, into which the screwed shaft of the X-feed mechanism of
the worktable is engaged.
Worktable
This is an oblong casting, with a pair of slides machined on the
(See fig 6)
underside across its width. These slides engage with the slides on the
upper side of the mounting slide. At the rear of the work table is an
upright fence, against which the work piece is clamped. The front of the
table has a small rectangular platform which has two drilled and tapped
holes machined to enable the mounting of the clamp using two bolts
and washers. The underside of the platform is machined to support a
captive threaded bar that is the worktable part of the X-feed mechanism.
The end of the bar protrudes from the front of the table and is fitted with
a small hand wheel to enable the shaft to be screwed in or out to drive
the X-feed of the worktable.