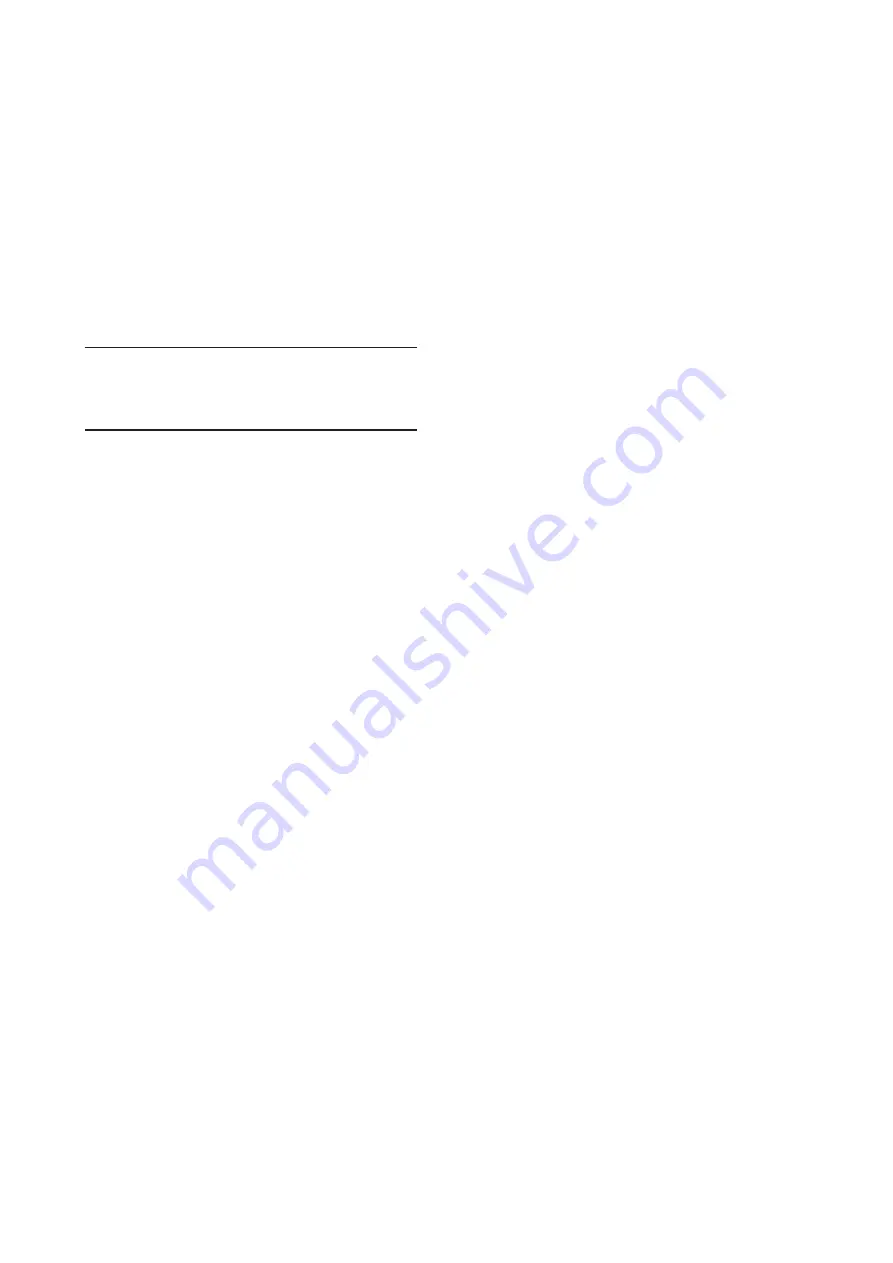
x
Check the span point and perform span adjustment.
(1) Set the input signal to the span point (URV). (Zero ad-
justment can be performed if the input signal is adjusted
to the zero point, and span adjustment can be performed
if the input signal is adjusted to the span point.)
(2) Using a flat-blade screwdriver, turn the external zero
span adjustment switch on the upper part of the case in
the UP direction (clockwise) to cause the valve to move
such that the feedback lever rises upward, or turn it
DOWN (counterclockwise) to cause the valve to move
such that the feedback lever drops downward.
5. Operation confirmation
Vary the input signal, and check the zero point and span
point.
6. If suitable adjustment was not accomplished
[1] If auto-setup does not operate
•
Check whether the input signal is 18 mA ±1 mA.
•
Check whether the A/M switch is set to automatic. If it is
set to manual, switch it to auto. See 5.2, “A/M Switch,” in
this document for information on operating procedures.
•
Check the duty value of the electro-pneumatic module.
Regarding the confirmation method, see “EPM (electro-
pneumatic module) operation confirmation procedure” on
page 3-9 in this document.
•
Check whether the electronics module (terminal block) is
installed correctly in the case on the body of the device.
[2] If hunting occurs
Using the setup device, either change the actuator size
(Param) or change the individual PID settings that control
the AVP’s degree of opening. Regarding the configuration
method, see 4.4.4, “Control configuration,” in this document.
[3] If the zero point floats or span adjustment cannot be
performed
Referring to Table 3-1, “Integral type setting,” in 3.1, “Auto-
setup,” in this document, check whether valve action is
configured correctly. If not, it will be necessary to change the
valve action (the direct/reverse setting). Referring to 4.4.3,
“Valve system,” in this document, configure the valve action
correctly.
[4] If linearity characteristic is poor
•
Check whether, when the attachment position of the feed-
back lever is the 50 % opening position, it is attached hori-
zontally. If not, refer to 2.2, “Installation Method,” in this
document and correctly attach the feedback lever.
•
Check the flow rate characteristics data. If equal %, quick
open, or the like has been specified, and these are funda-
mentally unnecessary, refer to 4.4.6, “Flow Type,” in this
document and change this setting to linear.
Summary of Contents for AVP200
Page 30: ......
Page 66: ...2 28...
Page 80: ...4 4 Menu Tree...
Page 120: ...5 16...
Page 128: ...6 8 For models those date of manufacture are before September 2017...
Page 130: ...6 10 For models those date of manufacture are before September 2017...
Page 132: ...6 12 For models those date of manufacture are before September 2017...
Page 136: ...6 16 For models those date of manufacture are after October 2017...
Page 138: ...6 18 For models those date of manufacture are after October 2017...
Page 184: ...Appendix A Specifications A 25...
Page 185: ......
Page 188: ......
Page 190: ......