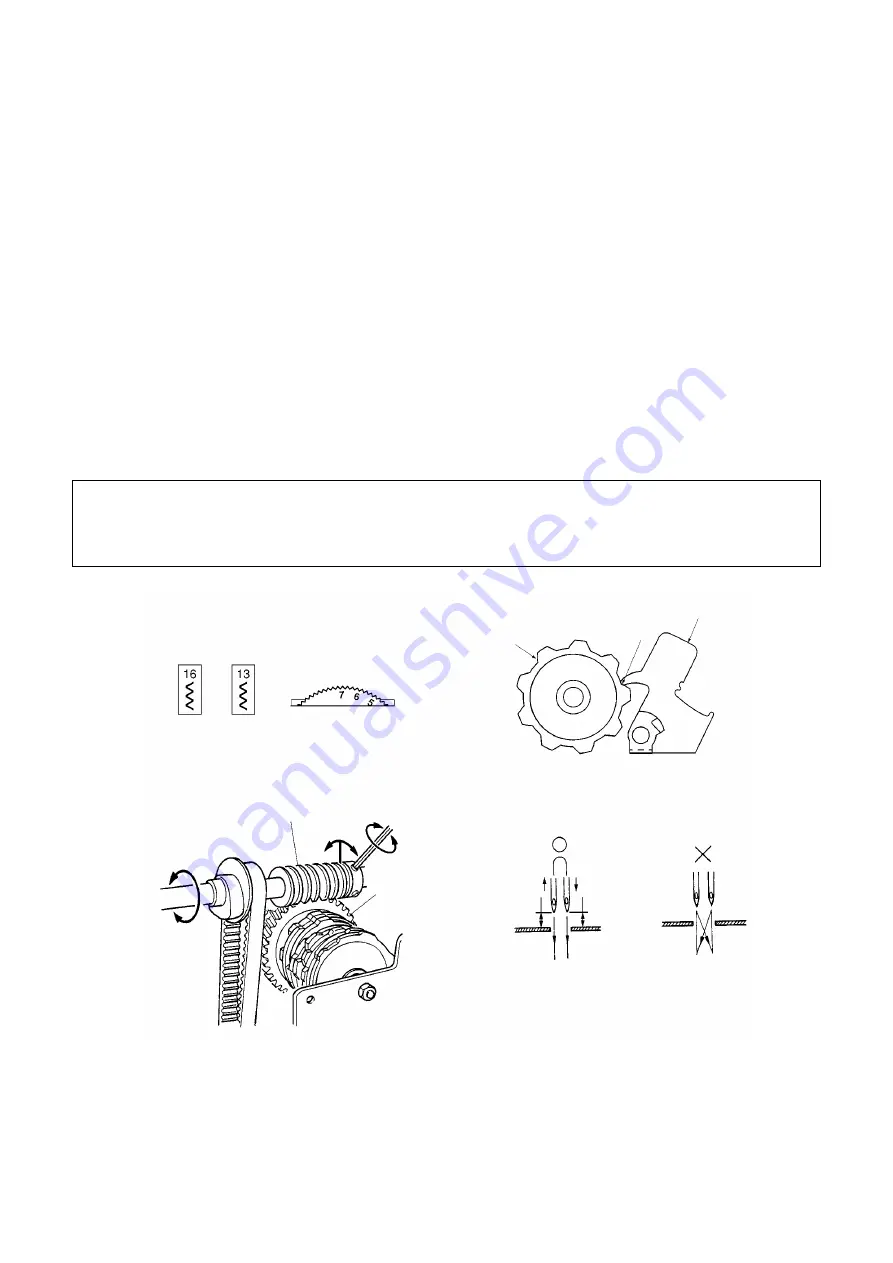
-36-
5.
NEEDLE FLOW
STANDARD
For zigzag sewing, the distance from the needle plate upper surface to the tip of the needle (#14) when the
needle bar starts oscillating movement should be 5.6
±
0.4 mm. Also, the distance from the needle plate top
surface to the needle (#14) tip when the needle bar oscillating movement stops must be 7.8
±
0.4 mm.
ADJUSTMENT
1.
Turn the selection dial to select zigzag sewing.
2.
Turn the Zigzag dial to the maximum.
3.
Loosen the three screws securing the worm gear.
4.
Turn the balance wheel, raise the needle bar from bottom dead center, and fasten the needle bar at a
position where the distance from the needle plate top surface to the needle tip (#14) is 5.6 mm.
5.
Turn the worm gear or pattern cam to put the Z finger and pattern cam in the state shown in Figure A.
6.
Tighten the three screws securing the worm gear.
7.
Turn the balance wheel and check how the needle flows.
Adjustment Points
6.
At this time, adjust the meshing of the worm gear and pattern cam gear. Adjust the meshing so that the
play on the pattern cam is no more than 0.1 mm at the outer edge of the cam and so that the balance
wheel turns freely by hand.
Pattern
cam gear
Worm gear
Figure A
Z finger
Contact
Pattern cam
7.8
±
0.4 mm
(Oscillation stop)
5.6
±
0.4 mm
(Oscillation start)
∗
When the needle flows from left to right
(BL6300)
(BL6800)