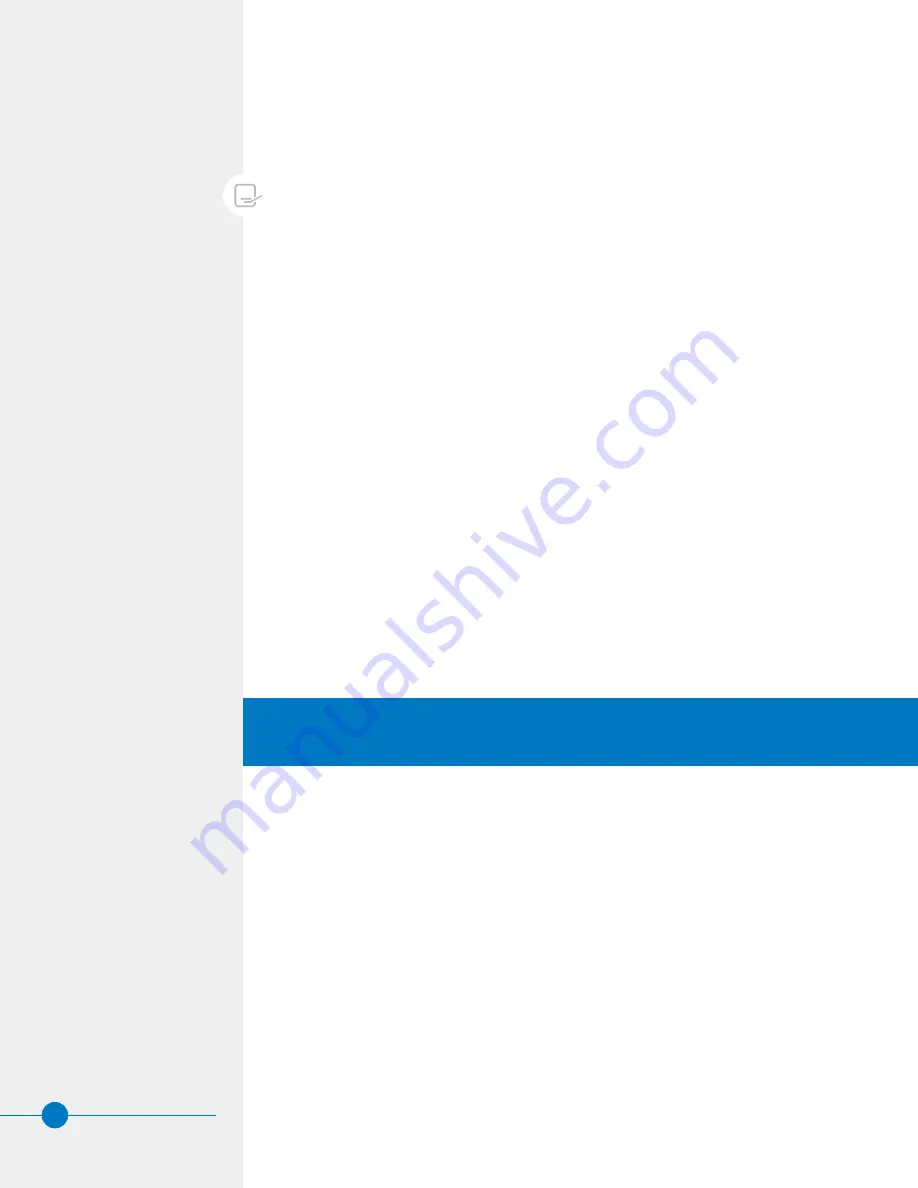
30
Fan Control
Reduce the unit capacity with the load by cycling the fans, thus modulating the airflow through
the unit. Rapid on-off cycles can cause the fan motor to overheat. Set the controls to allow a
maximum of six on-off cycles per hour. Periodically, cycle the fans off to prevent ice
formation and/or to melt ice that accumulates on the combined inlet shields.
The following are fan control methods:
•
Variable Frequency Drives
: VFDs offer the most precise method of capacity control by
modulating fan motor speed. When using VFDs, avoid operating at or near resonant
speeds. Units with VFDs require premium efficient/inverter duty motors.
•
Fan Cycling
: Cycle the fan off for five minutes every 15 to 20 minutes for each cell.
If ice continues to build on the air intake, decrease the on-time. Observe the
air intake
of the unit at least every four to eight hours.
•
Multi-Speed Motors:
If the unit is equipped with 2-speed motors or BALTIGUARD™ Fan
System, operation at a lower speed may be sufficient to prevent icing. The motor starter
should include a minimum 15 second time delay when switching from high to low speed.
•
Fan Reversal:
This procedure should be used only after the other methods of fan control
fail. If utilized, the fans should be run in reverse for no longer than 20 minutes and the
unit should be observed during this time. Operate the fans in reverse at 20-30% fan speed.
If water is observed exiting the air inlets, reduce the speed until no water is observed.
Before returning to normal operation, visually inspect the fan blades for ice formation.
Dry Operation
The HXV Hybrid Cooler provides high switch points for dry operation. One method to prevent
icing is dry operation. Dry operation of the HXV unit protects fans from ice formation due to
mist and splash from the cold water basin. The water in the cold water basin must be
drained for dry operation in freezing ambient conditions. For dry operation switch points and
recommendations, contact your local BAC Representative.
Basin Water and Internal Piping Freeze Protection
Cold Water Basin Protection
It is important to protect the basin and internal piping. The basin water could freeze when
the unit is shutdown and exposed to subfreezing ambient temperatures.
•
Basin Heaters
: On applications without a remote sump, heat must be provided to the
cold water basin to prevent freezing. Electrical immersion heaters will provide the
required protection. Contact BAC for more details.
•
Heat Tracing
: Heat trace and insulate all exposed water piping including pump piping
below the overflow level (see
Table 3, page 12) and make-up water lines with electrical
heater tape.
• Remote Sump: The ideal method of protection is a remote sump located in a heated
indoor space. When the circulating pump stops, the water in the connecting piping will
drain by gravity to this indoor sump.
• Electric Water Level Control: An electric water level control will maintain the proper
water level regardless of the thermal load or variations in make-up water supply pressure.
The two-position, slow closing solenoid valve provided with the BAC electric water level
control package also minimizes valve freezing problems (see
page 20).
NOTE:
Modulating the spray water
flow rate to the unit is NOT a
recommended method of controlling
cooling capacity.