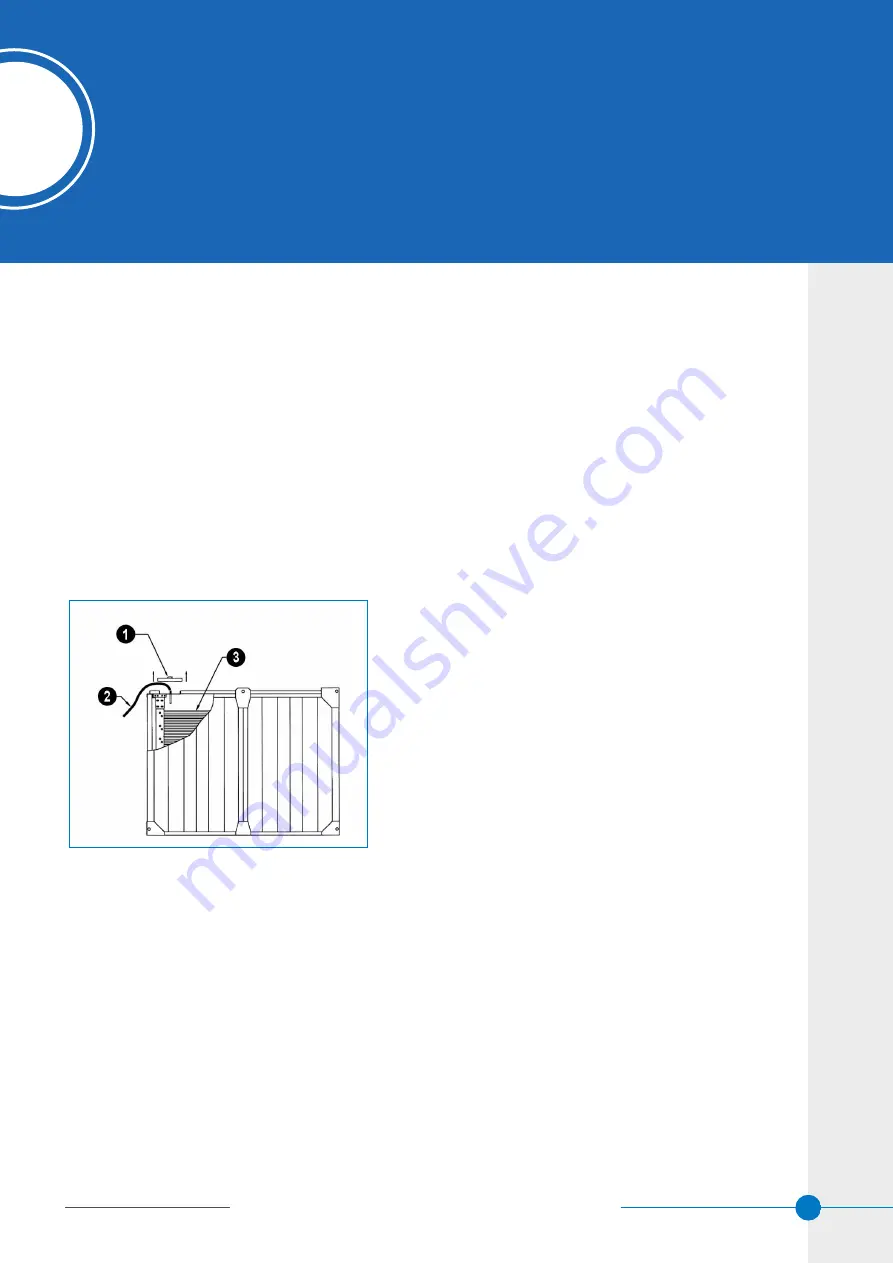
6 Maintenance Procedure
6 Maintenance Procedure
W W W . B A L T I M O R E A I R C O I L . E U
23
MAINTENANCE PROCEDURE
General
A program of regular inspection and maintenance is essential for optimum performance and maximum service life.
The following information is provided as a guide to establishing such a maintenance program. If you have any
specific questions, please contact your local BAC-Balticare service provider or representative whose name, e-mail
and phone number can be found on the website www.BACservice.eu. The model type and serial number of your
equipment appear on the nameplate at the connection end of the unit.
Checks and Adjustments
OPERATING LEVEL
Locate the tank access cover and the Sight Tube showing the tank water level (see figure below).
Side Elevation - Location of Tank Fill Connection
1. Access Covers
2. Fill Hose
3. Top of Coil Tubes
Using good quality water (see section "About Water Care" on page 19),fill the tank following the steps outlined
below. For proper, long-term operation of the thermal storage unit, the tank must be filled exactly to the prescribed
level.
1. Remove the access cover on the top of the unit. Use a fill hose to fill the tank. See following table “Fluid
Volumes” for the approximate volume of water required.
TSU-M
6