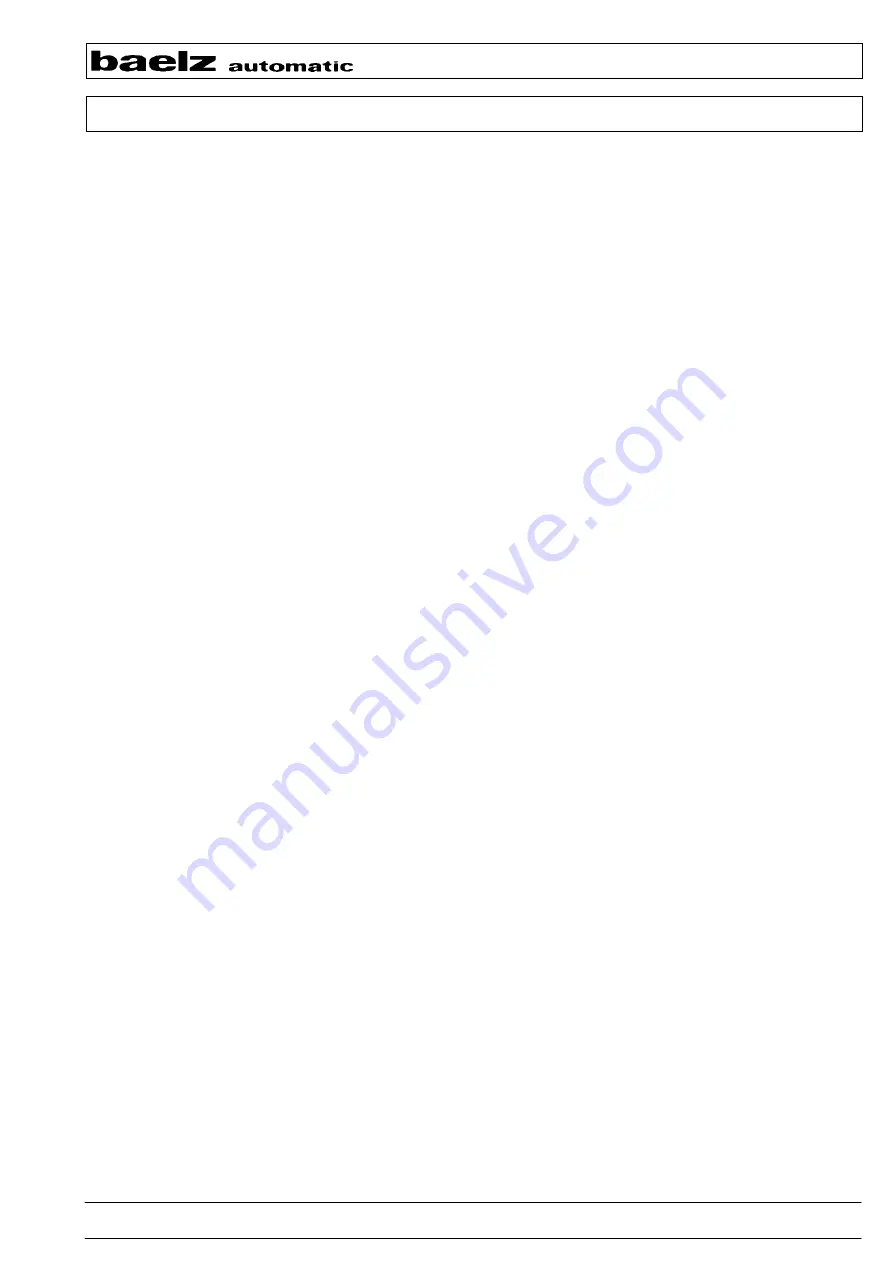
Page 13
Device manual
6490B / 6490B-y / 6590B
W. Bälz & Sohn GmbH & Co. Koepffstraße 5 D-74076 Heilbronn Telefon (07131) 1500-0 Telefax (07131) 1500-21
I.e. actual value at start of the optimisation = 60°C, target setpoint = 100°C which is a difference of
∆
T = 40°C.
The needful change of the actual value can be calculated then by
∆
PV = 1/4 *
∆
T = 1/4 *40K = 10K.
The optimisation can only be finished when the actual value is at least 60°C + 10K = 70°C.
Cause is a process gain which does not fit (see also 3.a) and 3.b)).
Solution: Cancel or finish the optimisation (see 5.).
Reduce the process gain P.G in the configuration level (e.g. 1/2).
Restart optimisation.
5. Cancelling the optimisation premature
An already running optimisation shall be cancelled without recalculation of the control parameters.
A reason for that could be e.g. a not permitted rise of the temperature over the tolerated limits during the optimisation.
After a cancel the process gain P.G can be magnified manually to get a smoother temperature change within the next
optimisation (see also 3.a) and 3.b)).
Cancelling by:
a) activating manual mode
b) setting a setpoint once more
c) activating a digital input (OPEN, CLOSE, STOP, SP.2)
d) activating the modbus RAM-setpoint (see "Modbus documentation")
Cancelling the optimisation premature, including recalculation of control parameters and process gain, can be realized by
changing "Opt = 1" to "Opt = 0" in the configuration level during process of optimisation.
6. The optimisation results are not satisfying
Reasons:
a) The optimisation did not run within the range the control is working after.
I.e. the range between 60°C and 80°C was optimised, but the following control works with a setpoint change
from 50°C to 100°C.
Solution: At beginning of the optimisation the actual value should correspond to the first point and the initial setpoint
to the other (target setpoint) of the desired control range (see also 2.c)).
b) Processes with strongly different time behaviour (e.g. fast heating up, slow cooling down) where the change of the
actual value during the optimisation worked reverse to the following control.
I.e. optimisation from 100°C to 50°C but the following control from 50°C to 100°C.
Solution: If possible, optimise in the same direction the control is working after. If it has to be controlled in both
directions, the more important direction has to be optimised. Do both directions have the same relevance,
the slower process has to be optimised.
c) The actual value has not been in a stable state before starting the optimisation.
Solution: Wait until the actual value is in a stable state before starting the optimisation. If the actual value can not get
stabilized in the automatic mode (oscillation), an optimisation started from the manual mode is necessary.
d) The target setpoint could not be reached at the end of the optimisation.
Solution: see 3)
e) During the optimisation the actuator must not run over the limits
→
neither 0% nor 100%. Nevertheless a completely closed
actuator at start of the optimisation would be tolerated, i.e. in case that a de-energized plant (with closed actuator) drives
immediately to the target setpoint at start of the optimisation.
Solution: Set a bigger process gain and restart optimisation or just set another target setpoint.
f) Power supply is not stable because of too many peripherals.
Solution: Optimisation only at times when a stable energy supply is guaranteed.
g) Controlling the process is almost impossible because the actuator does not fit (e.g. valve is over-sized).
Solution: Check dimensions of the actuator, change it if necessary.
h) The process can not be controlled perfectly with the chosen type of controller.
Solution: Let the optimisation run with another type of controller (PI or PID) and compare.