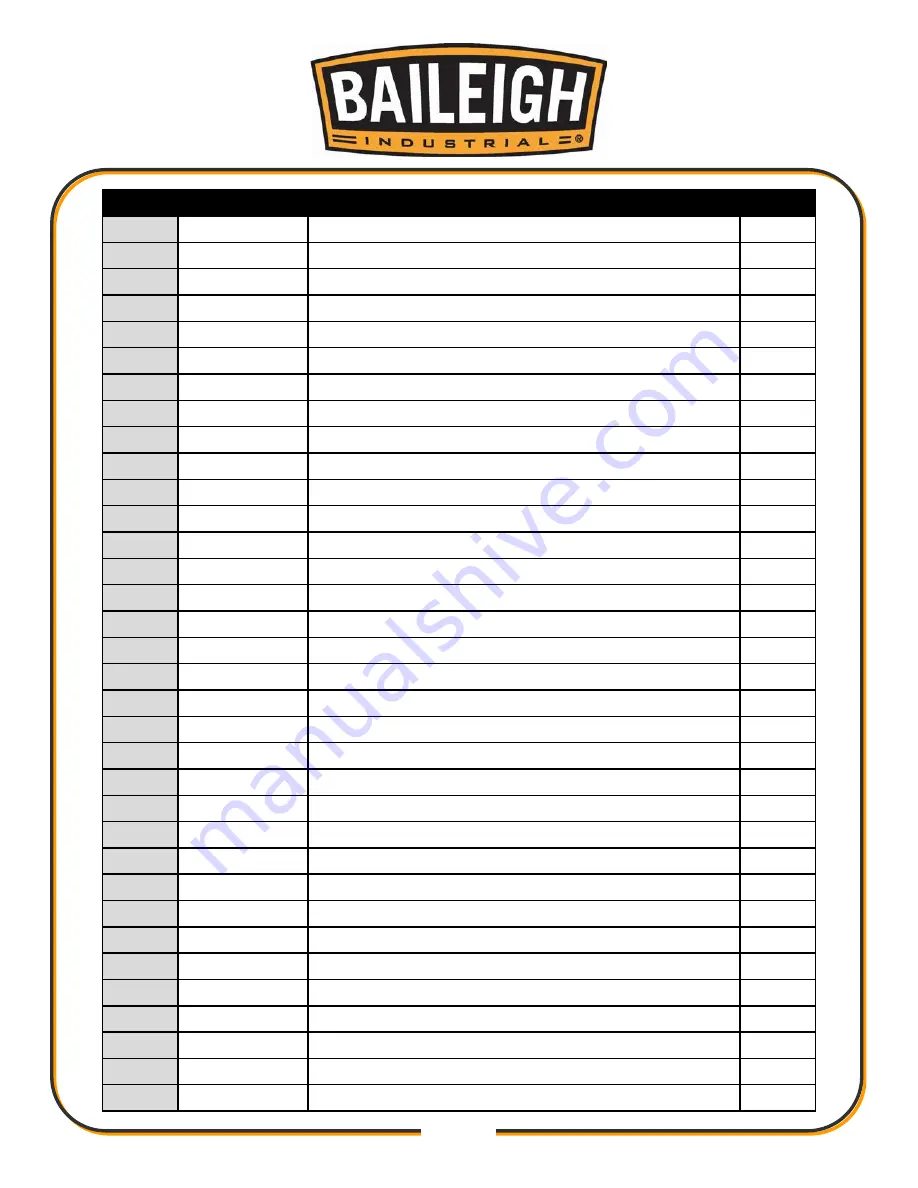
24
24
Item
Part No.
DISCRIPTION
Qty.
219
30202006p
BRACKET
1
220
30202007p
WORM
1
221
S0010615M
HEX. SOCKET CAP SCREW
4
222
30202008P
SHAFT
1
223
30204010
CRANK SHAFT
2
224
S0230400
SPRING WASHER
4
225
S0400415
KEY
1
226
C1106001
BEARING
2
227
S0521200
C RING
2
228
S0530028
C RING
2
229
S0230506
SPRING WASHER
11
230
S0210500C
FLAT WASHER
11
231
30202009
OIL CAP
1
232
30202012
STORAGE PLATE FOR DRUMS
1
233
30202013
STORAGE PLATE FOR TABLE INSERTS
1
234
30202014
OIL CAP
1
235
S0030304
PHILIPS HEAD SCREW
2
301
30203001
HOUSING
1
304a
30203003
BRACKET (RIGHT)
1
304b
30203003a
BRACKET (LEFT)
1
305
S0020825M
HEX. SCREW
13
306
30203004
TOP PLATE
1
308
S0020610M
HEX. SCREW
1
310a
40501001
SUPPORT TRUNNION (RIGHT)
1
310b
40501011a
SUPPORT TRUNNION (LEFT)
1
311
S0070615M
LOCK KNOB
2
312
S0010515M
HEX. SOCKET CAP SCREW
6
313
S0050605M
SET SCREW
1
314
10102022
POINTER
1
315
S0220400
GEAR WASHER
1
316
S0030510M
PHILIPS HEAD SCREW
1
317
30203005
DUST COVER
1
319
30203006
MAIN SPINDLE
1
320
30203007
SWITCH COVER
1
Summary of Contents for OS-1414
Page 23: ...21 21 PARTS DIAGRAM 1 ...
Page 24: ...22 22 PARTS DIAGRAM 2 ...