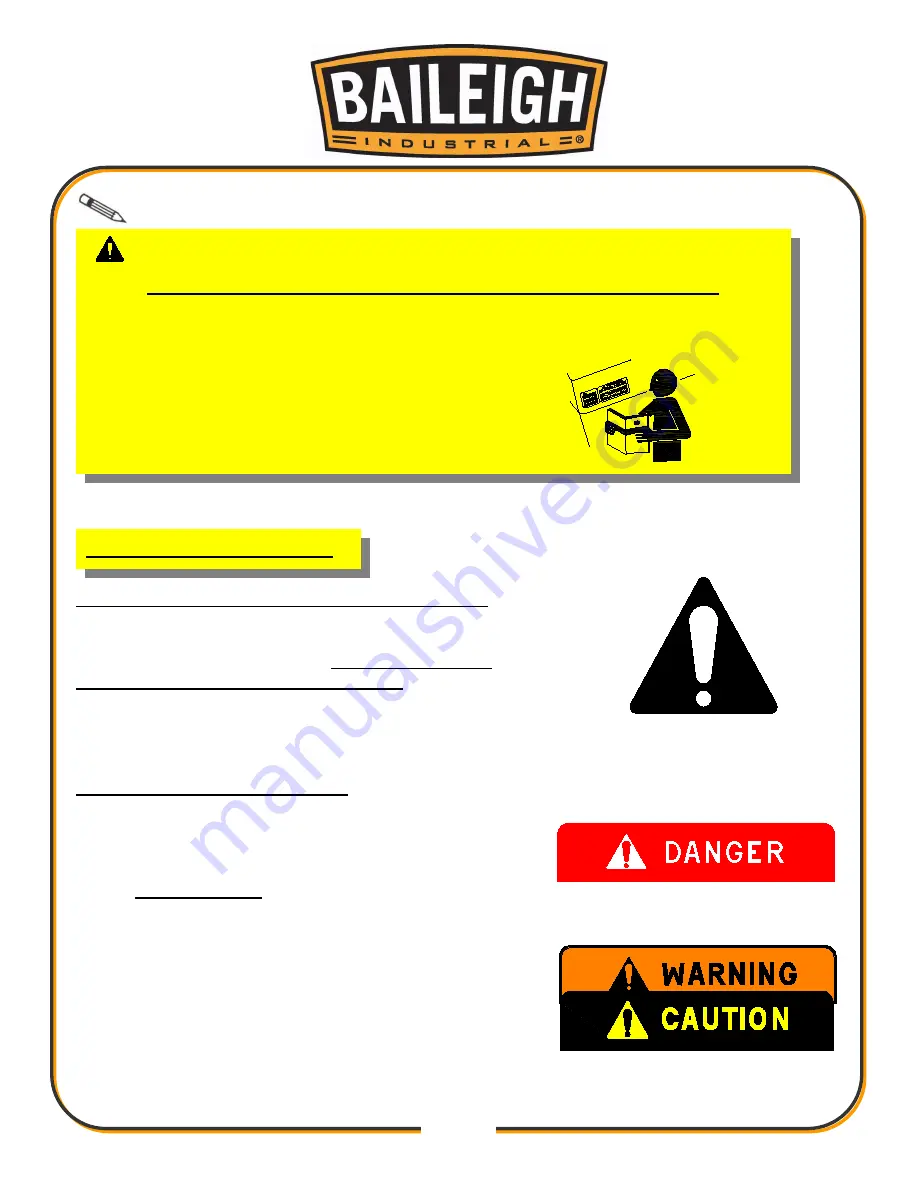
2
2
Note:
This symbol refers to useful information throughout the manual.
LEARN TO RECOGNIZE SAFETY INFORMATION
This is the safety alert symbol. When you see this symbol on
your machine or in this manual,
BE ALERT TO THE
POTENTIAL FOR PERSONAL INJURY!
Follow recommended precautions and safe operating
practices.
UNDERSTAND SIGNAL WORDS
A signal word –
DANGER
,
WARNING
, or
CAUTION
is used with the safety alert symbol.
DANGER
identifies a hazard or unsafe practice that will result in
severe
Injury or Death
.
Safety signs with signal word
DANGER
or
WARNING
are
typically near specific hazards.
IMPORTANT
PLEASE READ THIS OPERATORS MANUAL CAREFULLY
It contains important safety information, instructions, and necessary operating
procedures. The continual observance of these procedures will help increase your
production and extend the life of the equipment.
SAFETY INSTRUCTIONS
Summary of Contents for B8500
Page 15: ...13 13 PARTS IDENTIFICATION DRAWING...
Page 16: ...14 14 Parts Identification List...
Page 19: ...17 17 NOTES...
Page 20: ...18 18 NOTES...
Page 21: ...19 19...
Page 22: ...20 20...