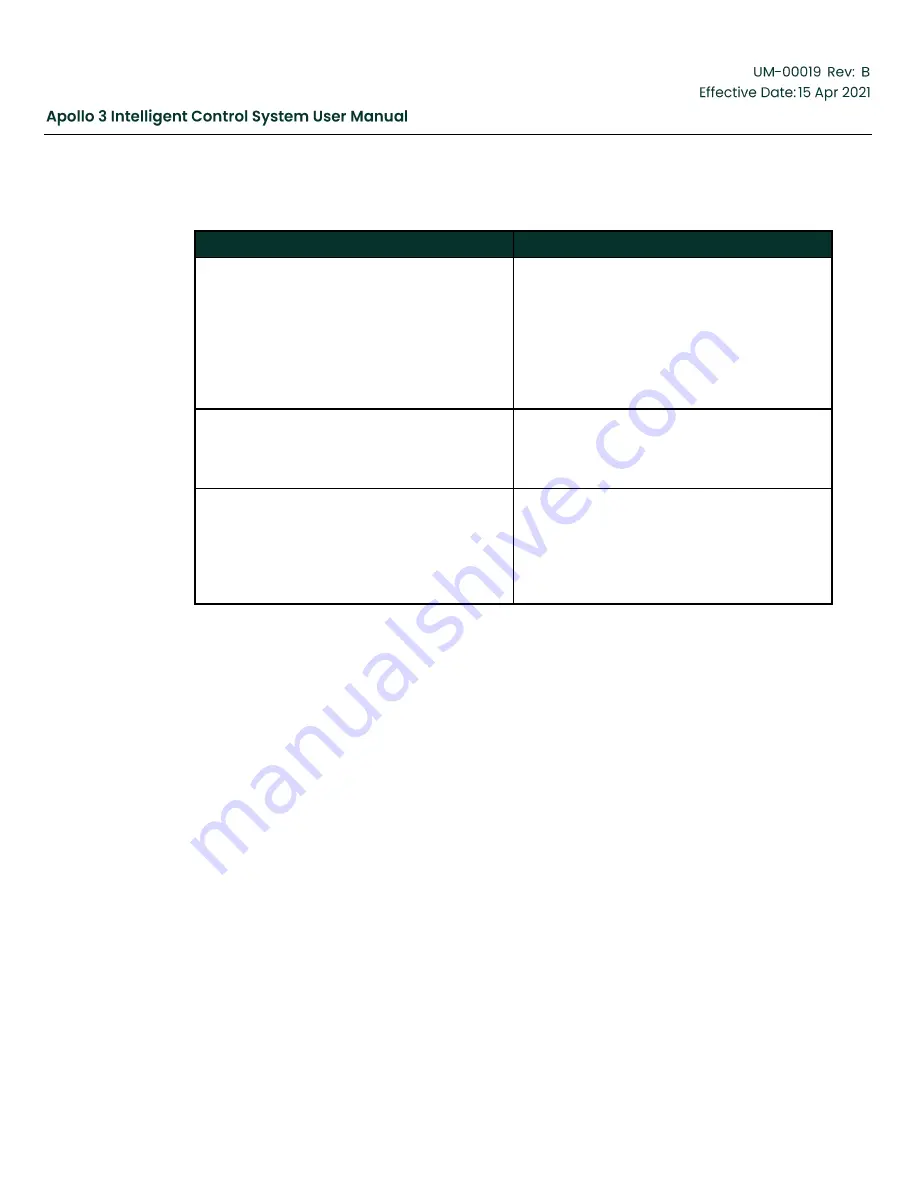
Copyright 2020 Baker Hughes Company. All rights reserved.
Page 151 of 277
Table 38: PID Speed Control Mode Parameters (cont'd.)
Parameter
Description
Mtr PIDUpdate
Run period for the PID loop. Best practice
is to keep at the same rate as the control
value (Source1) is updated. The downhole
tool is polled every 5 seconds, and the
Intake Pressure is read from the downhole
tool. Change only if the Source1 channel
is changed to a device that is polled at a
different rate.
Mtr PID ROC
PID Rate Of Change (ROC) limits how fast the
PID output will change. ROC is the amount of
time it takes the PID to ramp from 0 Hz to the
drive Max Frequency.
Mtr Spd PID
‘D’
The Derivative Gain used by the Proportional
Integral Derivative (PID) control loop used
to control the drive speed. This parameter
can be changed to tune the PID for optimal
performance. It is usually recommended to
leave the
‘D’ gain at 0.
5.6.4
Analog Follower Mode
Control mode in which the drive speed is based on a scaled analog input. Analog Follower mode
is often used in situations in which another controller, such as a PLC, dictates the speed at which
the drive should run using an analog signal.
Summary of Contents for Apollo 3
Page 1: ...Copyright 2020 Baker Hughes Company All rights reserved Page 1 of 277...
Page 266: ...Copyright 2020 Baker Hughes Company All rights reserved Page 266 of 277 Figure 227 USB Menu...
Page 267: ......
Page 276: ......
Page 277: ...Index 129112 28 197705 28 197349 28 800638 28 197350 28 810280 28 197351 29...