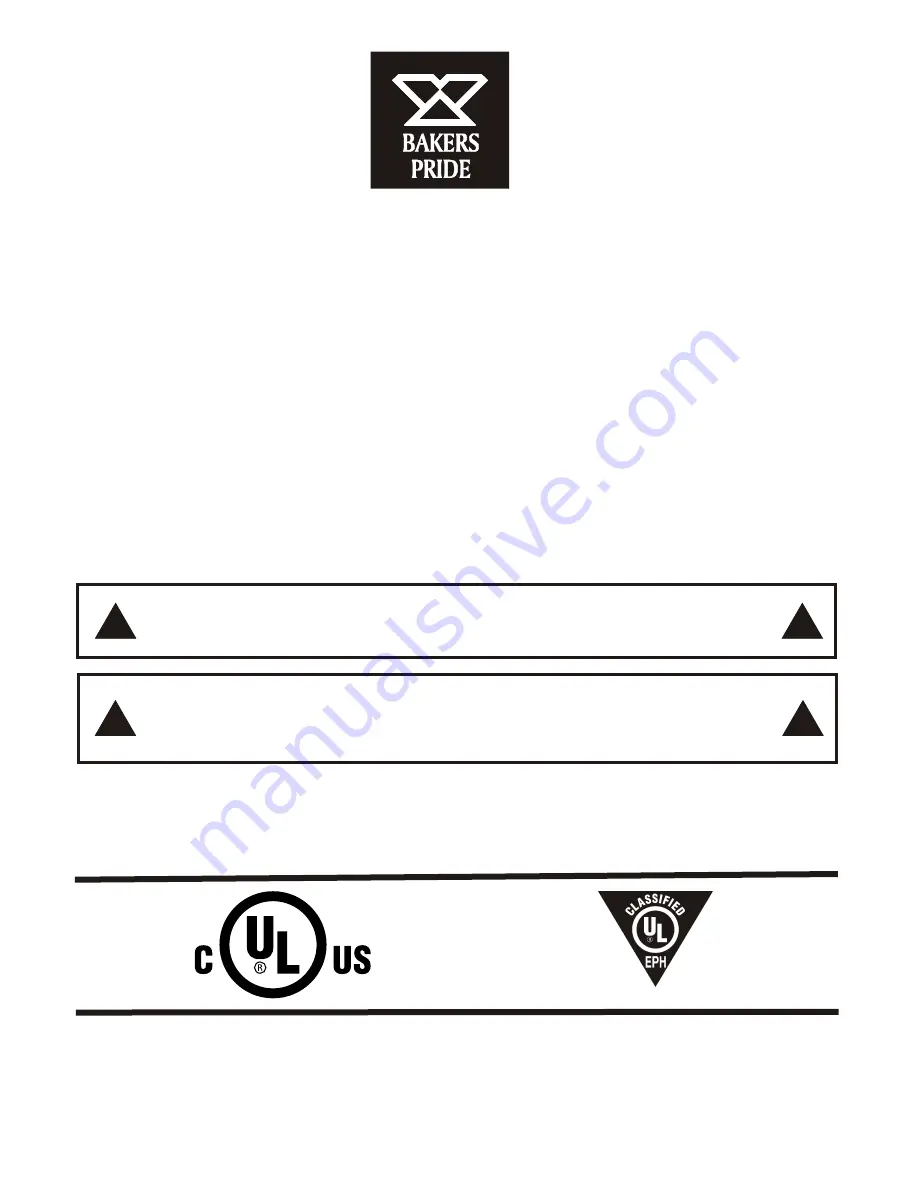
INSTALLATION
AND
OPERATING
INSTRUCTIONS
INTENDED FOR OTHER THAN HOUSEHOLD USE
Model:
VH1828G
RETAIN THIS MANUAL FOR FUTURE REFERENCE
OVEN MUST BE KEPT CLEAR OF COMBUSTIBLES AT ALL TIMES
This equipment has been engineered to provide you with year-round dependable service when used
according to the instructions in this manual and standard commercial kitchen practices.
Initial heating of oven may generate smoke or fumes and must be done in a well ventilated area.
Overexposure to smoke or fumes may cause nausea or dizziness.
FOR YOUR SAFETY:
Do not store or use gasoline or other flammable vapors and
liquids in the vicinity of this or any other appliance.
!
!
WARNING:
Improper installation, adjustment, alteration, service or maintenance can
cause property damage, injury or death. Read the Installation, Operating and
Maintenance Instructions thoroughly before installing or servicing this equipment.
!
!
COUNTERTOP MODEL
GAS IMPINGEMENT CONVEYOR OVEN
BAKERS PRIDE OVEN CO., INC
.
30 Pine Street
New Rochelle, NY 10801
+1 (914) 576-0200 Phone
(800) 431-2745
US & Canada
+1 (914) 576-0605 Fax
www.bakerspride.com Web Address
info@bakerspride.com
e-mail Address
1
P/N U4174A 2/08
ANSI/NSF4