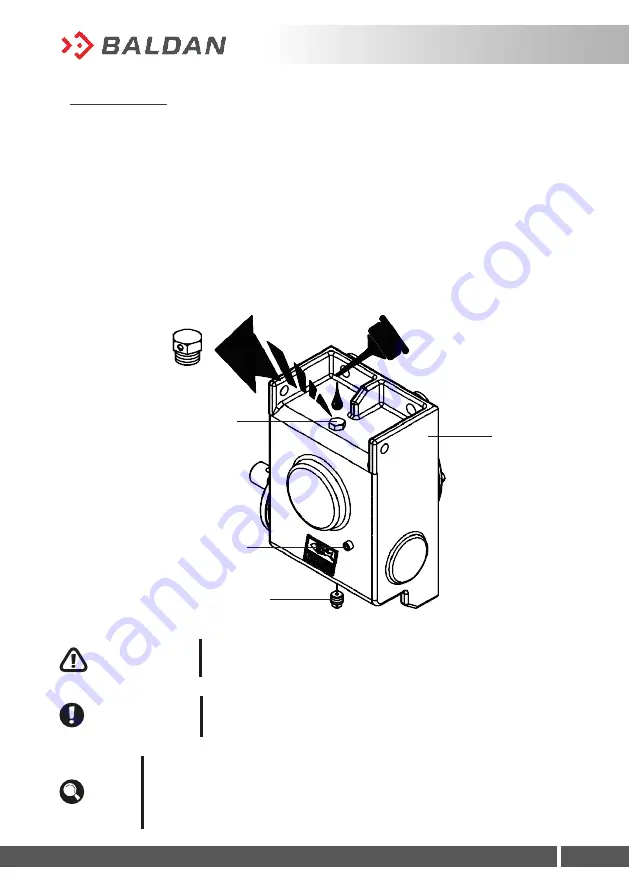
Instruction Manual
DCF-CO
83
3
1
2
4
Maintenance
• Oil change - Gearbox
Peridically check oil level of gearbox (1) through the screw indicating the level (2) and refill it
whenever required. To change the oil of the gearbox (1), proceed as follows:
01 -
Remove drainage plug (4), breather cap (3) and level indicator screw (2) draining all oil from
the gearbox (1).
02 -
Then, reinstall the drainage plug (4) and fill with the breather cap (3) until oil leaks through
the level vent (2).
03 -
Finish by placing level indicator screw (2) and breather plug (3) back again.
Do not fill with oil above the level. Only use the specifield oil:
85W140 API GL-5 MIL-L-2105D SAEJ306; May/81.
ATTENTION
Before operating the DCF-CO, remove the (“A”) plug from the gearbox
and place the (“B”) breather plug in its place.
IMPORTANT
Replace oil in first 200 hours of operation.
Then, change at every 1000 hours of operation.
When using a specific oil brand, avoid completing the oil level with a different
brand and specification.
NOTE
“A”
“B”
Summary of Contents for DCF-CO
Page 1: ...Lime Fertilizer and Organic Fertilizer Spreader DCF CO...
Page 2: ......
Page 112: ...InstructionManual DCF CO 112 Notes...
Page 113: ...InstructionManual DCF CO 113 Notes...
Page 116: ......
Page 118: ......
Page 121: ......
Page 122: ......