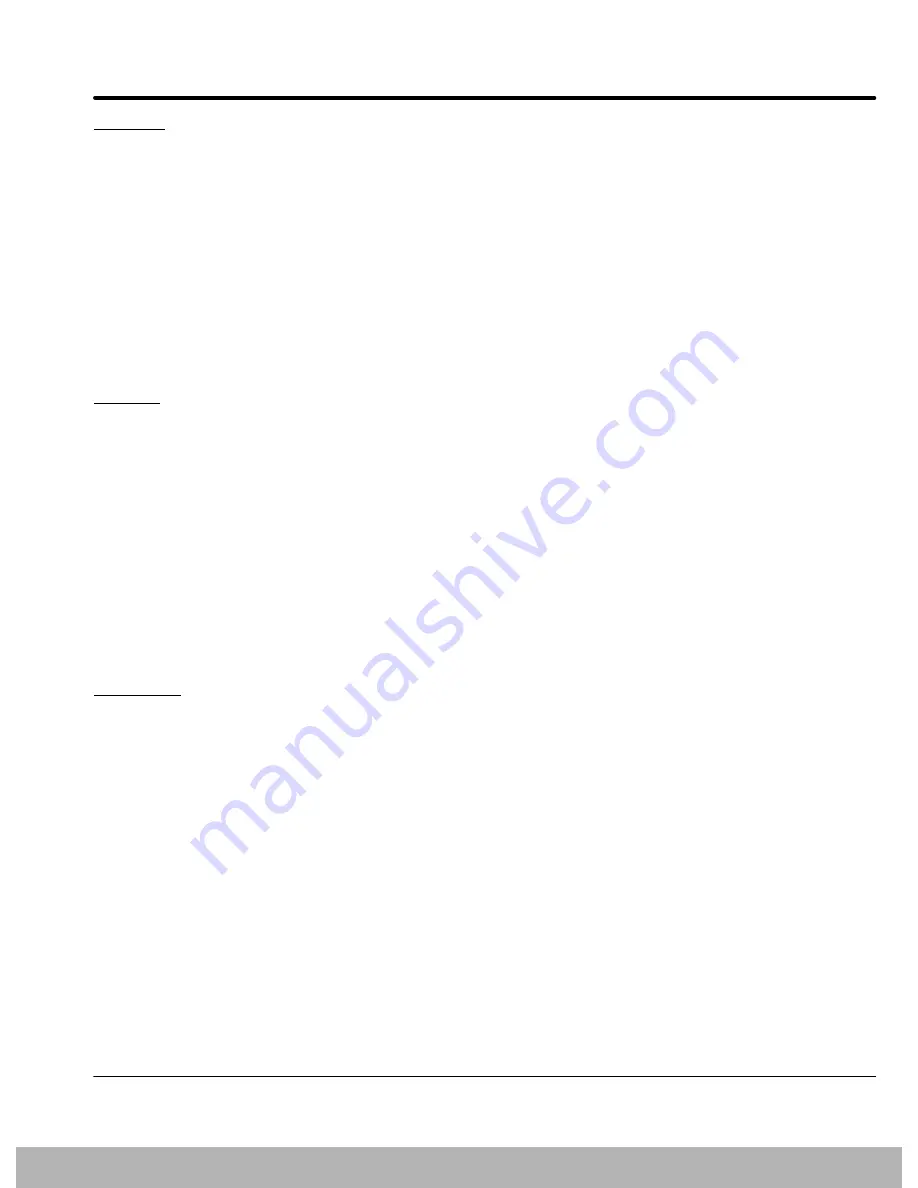
Section 2
Installation & Operation
Installation & Operation 2-1
MN409
Overview
Before installing the motor, be sure you read Section 1 and become familiar with the Warnings and
Cautions to prevent damage to the motor and prevent injury to personnel. This is extremely important for
a good installation and to ensure trouble free operation.
Installation should conform to the National Electrical Code as well as local codes and practices. When
other devices are coupled to the motor shaft, be sure to install protective devices to prevent future
accidents. Some protective devices include, coupling, belt guard, chain guard, shaft covers etc. These
protect against accidental contact with moving parts. Machinery that is accessible to personnel should
provide further protection in the form of guard rails, screening, warning signs etc.
1.
If the motor has been in storage for an extended period or had been subjected to adverse moisture
conditions, check the insulation resistance of the stator winding (see Checking Insulation Resistance
in section 3).
2.
Examine the motor nameplate data to make sure it agrees with the power circuit to which it will be
connected. The motor is guaranteed to operate successfully at line frequency not more than 5%, and
line voltage not more than 10%, above or below the nameplate ratings, or a combined variation of
voltage and frequency of not more than 10% above or below nameplate ratings. Efficiency, power
factor and current may vary from nameplate data.
3.
Check to make sure that direction of motor rotation is corrected for the intended application.
Location
It is important that motors be installed in locations that are compatible with motor enclosure and ambient
conditions. Improper selection of the motor enclosure and ambient conditions can lead to reduced
operating life of the motor. The motor must be located in an environment that satisfies local codes and
National Board of Fire and Underwriter’s regulations.
The following additional considerations should also govern its location.
On Totally Enclosed Fan Cooled (TEFC) motors the installation should be in a location that provides
adequate space for air circulation of the external cooling fan. Exposure to high ambient temperatures,
humidity and atmospheric contamination should be avoided. Acids, alkalis and gases also have
detrimental effects on electrical machinery. The location of installation should be accessible for routine
maintenance and inspection.
If the room is not large enough to have natural ventilation, some external source of forced and filtered air
will be necessary. The room should be such that the heat developed during operation can escape and will
not be recirculated over the equipment.
Permanent handling equipment to facilitate major service and repair without complete disassembly of the
individual units should be considered.
If the motor must be moved or additional handling or shipment of motor be required, be certain to block
the shaft as it was blocked for shipment by the factory. Blocking the shaft, limits the rotor movement both
axially and radially which prevents damage to the bearings.
Foundation
The dimensions for mounting are shown on the outline drawing supplied with the motor software and
should be referred to prior to planning of the foundation.
The foundation should consist preferably of solid concrete walls or piers and should be carried down far
enough to rest on a solid sub
−
base. This base should be sufficient stiffness to prevent vibration and to
insure long, trouble free operation. If necessary, a consulting engineer, who is familiar with foundation
design, should design and supervise its construction.
If the foundation is to be steel girders instead of concrete, the girders should be well braced and
supported by adequate columns to prevent vibration due to resonance. The natural frequencies of the
motor and supporting structure must be at least 20% away from the speed of rotation and twice the speed
of rotation and multiples of the power line frequency.
The size of the foundation is determined by the weight, size and speed of the equipment and by the type
and condition of the underlying soil. The width and length of the foundation are usually made to extend at
least 6 inches (150mm) beyond the equipment on all sides of the base. Increased width and weight are
necessary for operation at higher speeds and for foundations that project above the floor level to give
stability against rocking and resonant vibration.
Large motors are not rigid or self
−
supporting, and should be uniformly supported. Therefore, when set on
the foundation or base, adequate support should be provided by leveling plates and shims between the
frame and the foundation, at points of loading; Le., under the frame feet, and intersection points of the
beams as well as under long, unsupported sections of the base. The number of shims should be kept to a
minimum. A few thick ones are preferred over many thin ones.
Space should be allowed between the base and foundation for grouting. The concrete surface should be
roughed to provide a good bonding surface.
This Manual:http://www.manuallib.com/baldor/mn409-large-ac-motors-handbook.html