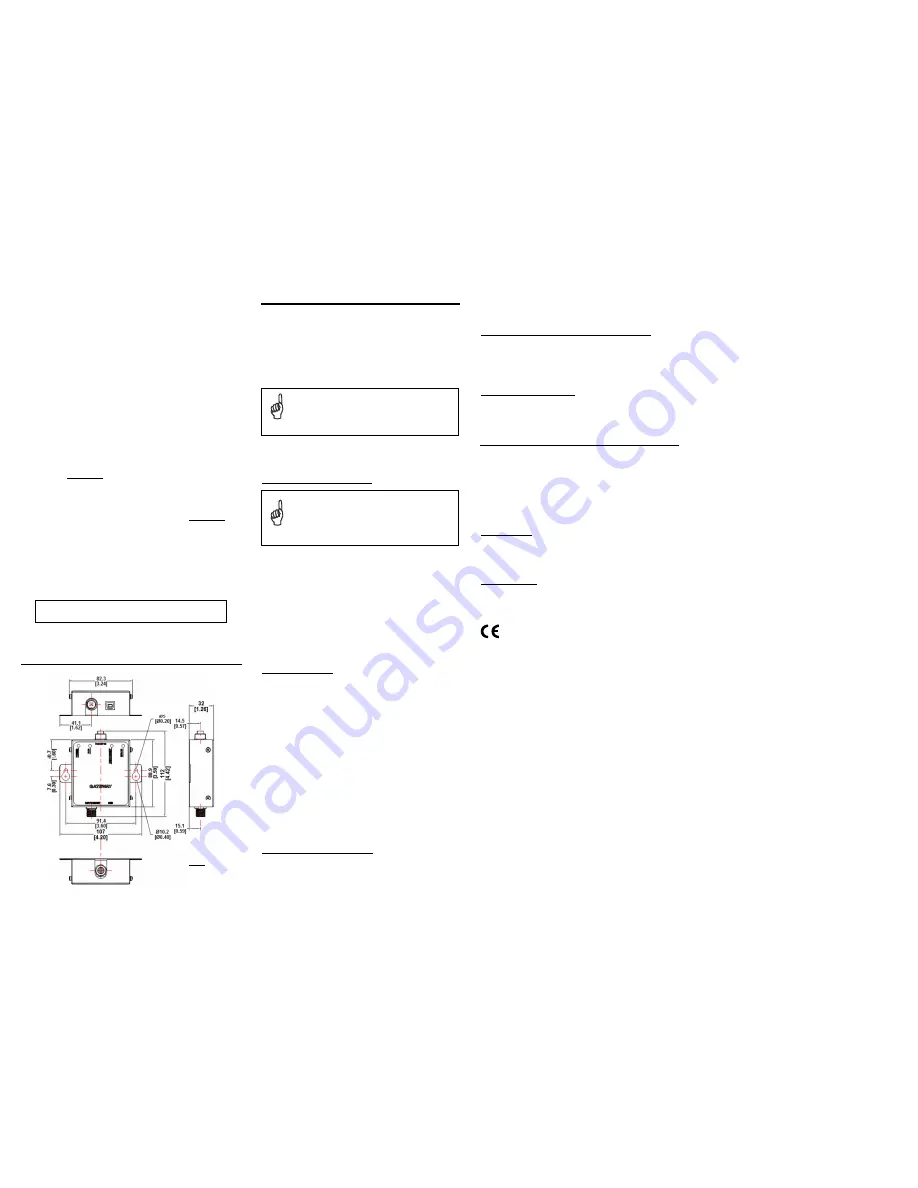
6. RFID Controller Connection: Connect the male end of a 5-pin,
male-to-female, ThinNet drop cable to the female end on your
Drop-T connector(s). Attach the remaining female end of the
ThinNet drop cable to the 5-pin, male, M12 connector on a
BIS U,
BIS M-6xx or BIS M-41x (RS485 models). Repeat Step 5 for
each RFID controller you plan to install.
Note: maximum drop cable length is 2 m.
Subnet16™ Power Supply Wiring: For ThinNet Networks: Using a 5-
pin, female, M12, ThinNet connector (
P/N: BCC06ZF), make a power
cable and connect it to your power supply (SHIELD wire connected to
Earth). Attach the female, ThinNet end to the 5-pin, male, ThinNet end
on a Drop-T connector (
P/N: BCC07WR).
7 . Gateway Power and Host Connection: Connect the Gateway to
the DeviceNet network via a DeviceNet-compatible interface
cable. The Gateway must be powered through pins V+ and V- of
the DeviceNet connector.
8 . Power On: Turn both power supplies ON. The POWER LED on
the Gateway will remain lit while power is applied to the unit
through the DeviceNet connector.
9 . Automatically Configure Subset16™ Node IDs: At this point all
controllers are powered and should have Node IDs set to 00, (all
controller Node LEDs = OFF), and Subnet16™ baudrate = 9600
(factory defaults).
a. Place the RFID Controller Configuration Tag in front of an
RFID Controller (the controller's RF Activity LED blinks once
indicating the tag has been read), and wait for the Gateway to
assign a valid Node ID to it. The controller's Node LEDs now
indicate a valid Node ID. Remove the Configuration Tag from
the controller.
b. Repeat this step for each node in the Subnet16™ network
(one controller at a time). The first is Node ID 1, then 2 and so
on up to 16 (binary).
The Subnet16™ network is now configured with the default values and
can communicate with the DeviceNet Gateway which in turn
communicates with the DeviceNet Master.
BIS Z-GW-001-DNT DEVICENET FACTORY DEFAULTS:
Node Address: 63; Baud Rate: 125 kbps
For further information or for application specific configuration using
the Dashboard Configuration Tool program, see the Gateway Manual.
DIMENSIONS
POWER REQUIREMENTS
The DeviceNet Gateway requires an electrical supply voltage of
12 to 30 Vdc. It is powered through the DeviceNet network
connector.
In addition, each RFID controller connected to the Gateway via
the Subnet16™ network will also require power. This network is
powered separately. Use a regulated power supply that is
capable of delivering the requirements listed in the Technical
Features.
NOTE
Power is applied directly to the Subnet16™ Network
trunk and distributed through drop cables to the RFID
controllers. By positioning the power supply near the
middle of the network, you can limit voltage drop at the
ends, (see example layouts).
The following information is provided to assist you in
determining the power requirements of your RFID application.
System Current Consumption
NOTE
The current consumption values of each product are
given in the Technical Features paragraph of the relative
Installation manual and refer to the min and max input
voltage range. These values already include an
adequate safety margin. The consumption values given
in the following examples have been interpolated for an
input voltage of 24 Vdc.
Max Gateway Current: 200 mA @ 12 Vdc (133 mA @ 24 Vdc).
Max Processor Current: 366 mA @ 24 Vdc for BIS M-6xx-Series, 87
mA @ 24 Vdc for BIS M-41X-Series, etc. (refer to Processor ’s spec).
Calculating Subnet16™ System Current Consumption:
Subnet16™ System Current Consumption = (Max Controller
Current x Number of Controllers)
Example
A Subnet16™ network powered at 24 Vdc is composed of a BIS Z-GW-
001-DNT connecting eight BIS M-41X-485 Processor s.
Subnet16™ System Current Consumption = (0.087 A X 8)] = 0.696 A
Cable Voltage Drop
In addition, each RFID controller on the Subnet will experience a certain
amount of voltage drop depending on the length of the cable.
Cable Resistance per Meter
•
ThinNet = 0.058 ohms per meter per wire
•
ThickNet = 0.0105 ohms per meter per wire
Calculating Voltage Drop
Voltage Drop =
(Max Controller Current x Number of Controllers) x
(Cable Resistance per Meter per Wire
1 x Cable length
in Meters)
Example
A Subnet16™ network is composed of a BIS Z-GW-001-DNT
connecting eight BIS M-41X-485 Processors (87 mA each @ 24 Vdc). A
total of 20 meters of ThinNet cables are used to connect the devices,
which have Cable Resistance = 0.058 Ohms per meter per wire. The
network power is 24 Vdc.
2
Voltage Drop =
(0.087 A x 8 controllers) x [(0.058 x 2) x 20 meters] =
1.61 Vdc
24 Vdc - 1.61 = 22.39 Vdc at controller number 8
1
The resistance calculation must include both wires (Vdc and GND).
2
This example assumes the power supply is placed at the end of the
network, therefore controller #8 is the worst case. By placing the
power supply in the middle of the network the voltage drop at the
ends is reduced.
It is recommended that the voltage drop calculation be conducted on
the RFID controller that is farthest from the Gateway, as it will
experience the greatest voltage drop.
Max Supported Trunk and Drop Cable Lengths
•
ThickNet trunk length up to 300 m.
•
ThinNet trunk length up to 20 m.
•
ThinNet drop cable length up to 2 m.
Current Rating for Cables
The maximum current rating for the Subnet16™ network using
Balluff cables and accessories (BCCxxxx), is 4.0 A.
COMPLIANCE
This product is intended to be installed by Qualified
Personnel only.
This product must not be used in explosive environments.
See the Subnet16™ Gateway Manual for the Declaration of
Conformity.
Power Supply
This device is intended to be supplied by a UL Listed or CSA
Certified Power Unit with «Class 2» or LPS power source.
CE Compliance
Warning: This is a Class A product. In a domestic environment
this product may cause radio interference in which case the
user may be required to take adequate measures.
mm
in
N
r.
8
9
0
4
1
3
E
.
E
d
it
io
n
1
3
0
5
;
S
u
b
je
c
t
to
m
o
d
if
ic
a
ti
o
n
.