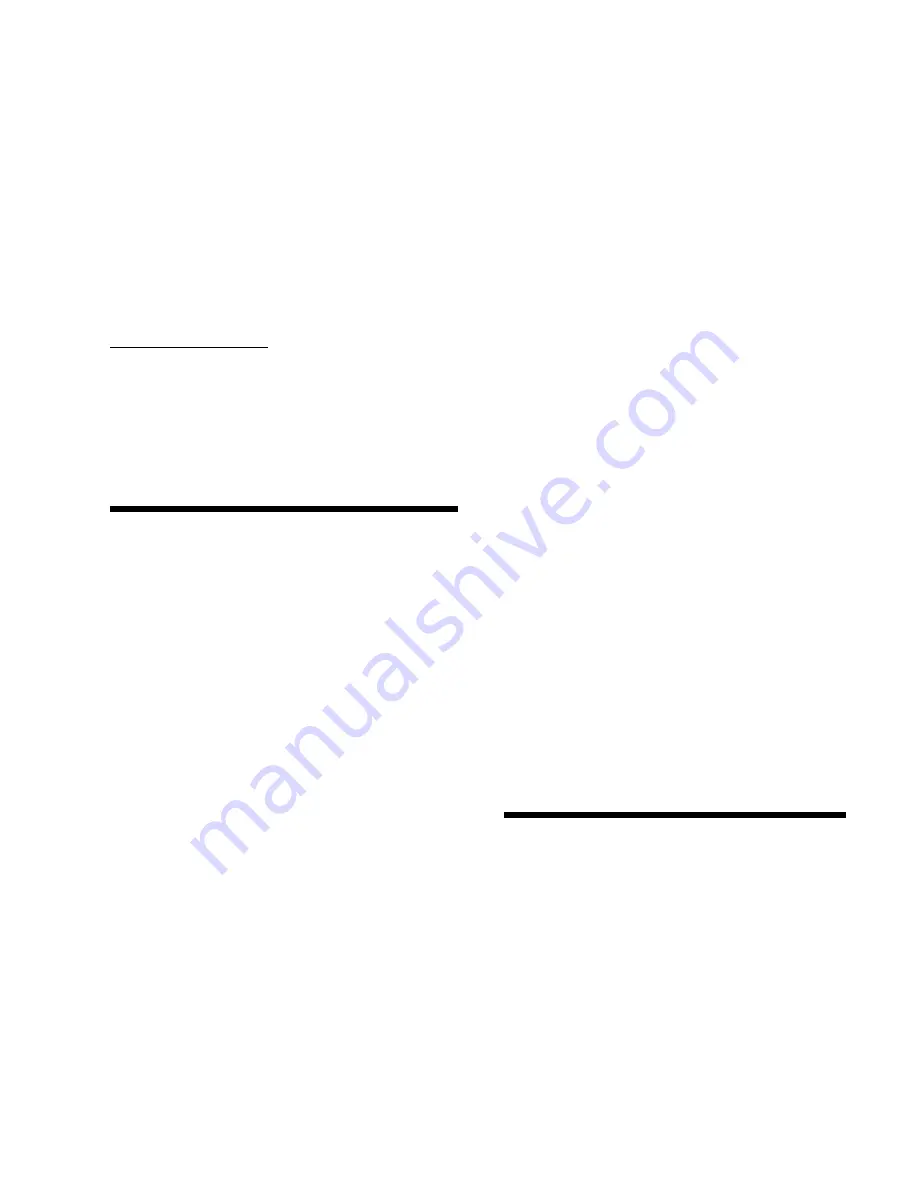
Baltimore Aircoil Company maintains a stock of replace-
ment parts at each of its manufacturing facilities.
Shipment of these parts is normally within four days after
receipt of an order. In emergency situations, shipment can
usually be made within twenty-four hours. To order factory
authorized parts, contact your local B.A.C.
Representative. Be sure to include the unit serial number
when ordering any parts.
To facilitate servicing the unit, it is suggested that the fol-
lowing parts be carried on hand:
Make-Up Float Ball
Valve Seat for Make-Up Valve
Fan Shaft Bearings
Fan Wheel
Fan Belt(s)
Fan Shaft
Spray Nozzles and Grommets
Spray Distribution Branch Grommet
Access Door Gasket
The necessary precautions include:
1. Limit the duration of the cleaning to one, or at the
most, two days.
2. The temperature of the solution should never exceed
100°F.
3. The maximum concentration of chemicals in the circu-
lation solution should not exceed any of the following:
5% Sodium Hydroxide
5% Sodium Metasilicate
2% Sodium Carbonate
2% Tetra Sodium Pyrophosphate
0.5% Trisodium Phosphate
0.5% Sodium Nitrate
5-10% Butyl Cellosolve
Evaporative Condensers
The installation and manufacturing processes commonly
used for field-assembled steel-piped refrigeration systems
leave weld byproducts inside coils and connecting piping.
It is common practice to install filters and/or strainers that
remove contaminants during initial system operation.
Shortly after system startup, the filters and/or strainers
should be cleaned or replaced.
Biological Control
B
leed-off with or without chemical treatment for
scale and corrosion control is not adequate for
control of biological contamination. The growth
of algae, slimes and other microorganisms, if unchecked,
will reduce system efficiency and may contribute to the
growth of potentially harmful microorganisms, including
Legionella, in the recirculating water system.
Accordingly, a biocide treatment program specifically
designed to address biological control should be initi-
ated when the system is first filled with water and
administered on a regular basis thereafter in accor-
dance with the supplier’s instructions. Liquid biocides
may be added to the basin of the cooling unit in dilute
form. If a solid form of biocide is used, it should be added
to the system via a pot feeder. If ozone water treatment
is used, ozone concentrations should not exceed 3-4
ppm in order to ensure maximum equipment life.
B.A.C. offers a simple, easily applied, low maintenance
form of biological control, the IOBIO‚ Bacteria, Slime and
Algae Control. The control is easy to use and requires lit-
tle maintenance. By delivering low concentrations of
iodine through the make-up water line, the IOBIO‚ Control
automatically controls unwanted microbiological contami-
nants in the open water system. Contact your local B.A.C.
Representative for more information.
START-UP FOLLOWING A SHUT-DOWN PERIOD
To minimize the risk from biological contamination
following a shut-down period, it is recommended that
the entire system (evaporative cooling equipment,
system piping, heat exchangers, etc.) be drained
when the system is to be shut-down for more than
three days. To resume operation of a drained system,
clean all debris, such as leaves and dirt from the cooling
tower and re-fill the system with fresh water. While operat-
ing the circulating pump(s) and prior to operating the unit
fans, execute one of the following two alternative biocide
treatment programs:
1. Resume treatment with the biocide, which had been
used prior to shut-down. Maintain the maximum recom-
15
Factory
Authorized Parts
mended biocide residual (for the specific biocide) for a
sufficient period of time (residual and time will vary with
the biocide) as recommended by the water treatment
supplier to bring the system under good biological con-
trol.
2. Check the pH of the circulating water and, if necessary,
adjust it to 7.0 to 7.6. Then treat the system with sodi-
um hypochlorite to maintain a level of 4 to 5 mg/l (ppm)
free chlorine (as Cl2) over a six (6) hour period. Test
kits that can be used to measure the free residual of
chlorine are commercially available.
When it is not practical to drain the system during shut-
down periods, a by-pass line with shut-off valves should
be installed to permit the cooling water to be circulated
throughout the system, including the unit basin, while by-
passing the heat transfer section. Then, after each shut-
down of three (3) days or more, the system should be
treated prior to restarting the unit using one of the two
methods described above.
However, while circulating the treated cooling tower
water through the entire system, the cooling tower fill
should be by-passed and the tower fans kept inopera-
tive. After the biocide residual has been maintained at the
required level for at least six (6) hours, the water can be
directed over the fill and the tower returned to service.
The standard water treatment program (including the bio-
logical treatment) should be resumed at this time.
For specific recommendations on treatment for scale,
corrosion, or biological control, consult a qualified
water treatment consultant.
COIL CLEANING
Both the inside and outside of the heat exchange coil may
require occasional cleaning. The chemicals used must be
compatible with the materials being treated (for example -
standard coil: outside of the coil is galvanized steel; inside
coil is black carbon steel). For specific recommenda-
tions on coil cleaning, consult a qualified water treat-
ment consultant.