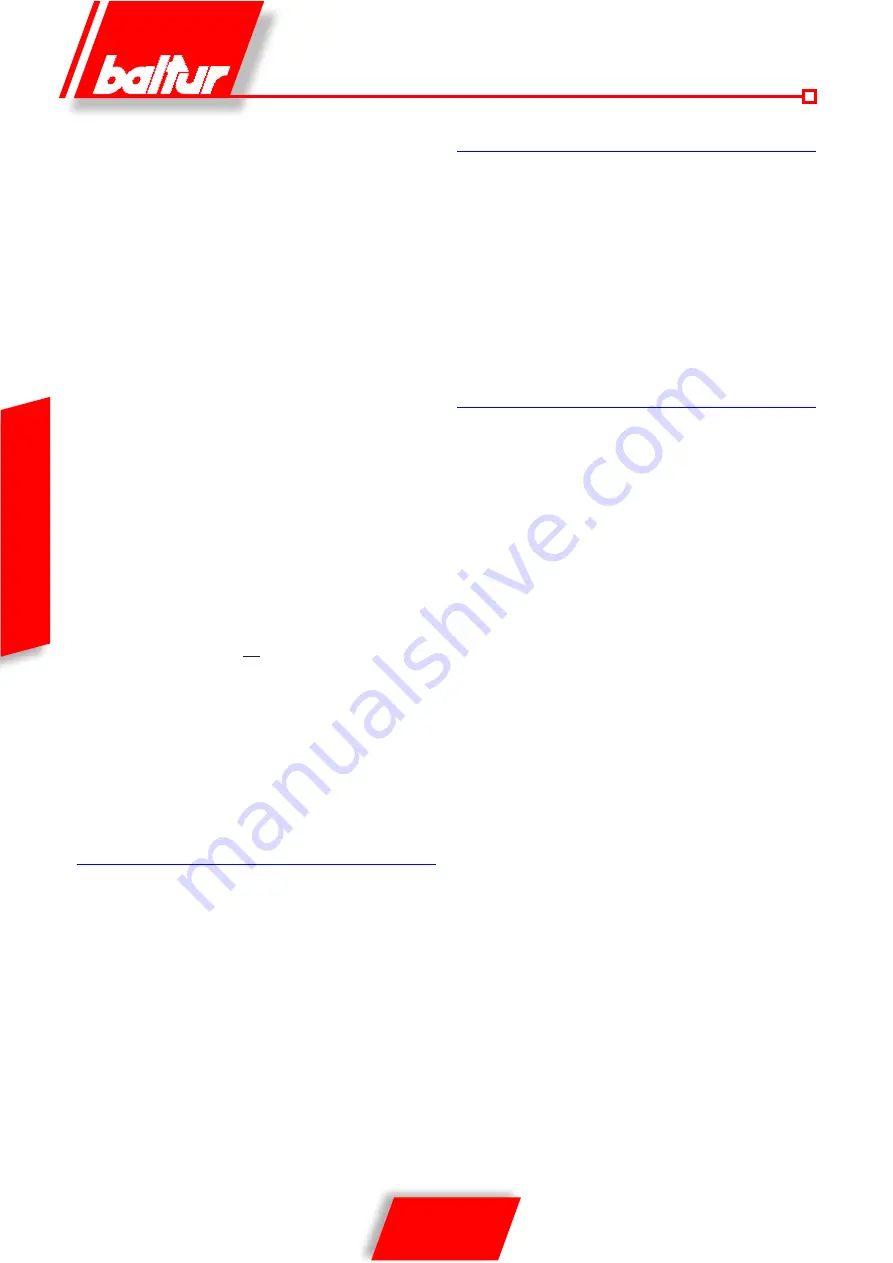
22 / 42
0006080764 _201312
ENGLISH
• The modulating servo-motor will now start up. wait until the
modulator disk has moved through an angle of about 12°
(corresponding to the space occupied by three screws) and
then interrupt modulation by turning the switch back to “O”.
Make a visual check on the flame and if necessary regulate
gas and air throughput rates using the regulator screws on the
modulator disk. The operation above must be progressively
repeated (making the disc turning by approx. 12° each time)
and adjusting, if necessary, the gas and air output along the
modulation stroke. It is important to check that the gas and air
flows rates rise gradually and that maximum rates are obtained
at the end of the modulation range. This condition is necessary
to ensure that modulation operation is gradual enough. Change
the fuel control screw positioning in order to fulfil the above-
mentioned condition.
• At this point, with the burner providing the maximum heat output
required by the boiler, check combustion using the appropriate
instruments and, if necessary, modify the previous setting made
solely on the basis of visual inspection. (CO2 max. = 10% which
corresponds to an O
2
value of about 3% - CO max. = 0,1%).
• It is recommended to check combustion also in some
intermediate points along the modulation stroke, using the
specific tools and, if necessary, modify the previous setting
made after a visual check only.
• Now check that the modulation system is operating correctly by
turning the AUT - O - MAN switch to “AUT” and the MIN - O -
MAX switch to “O”. With this setting the modulation function will
be enabled automatically only in response to requests from the
boiler probe. It is normally not necessary to act on the internal
adjusters of the electronic modulation regulator; however, the
relevant instructions are to be found in the pamphlet.
• Check that the flame supervision device (UV photocell) is
operating correctly by sliding it out of its seat on the burner and
checking that the burner effectively locks out.
• Check that the boiler thermostats or pressure switches are
operating correctly (they must cause the boiler to shut down
when they intervene).
USE OF THE BURNER
The burner operates fully automatically: it is activated by switching
on the main switch and the control panel switch. Burner operation
is controlled by command and control devices, as described in the
chapter “Operation description”. The “shut down” position is a safety
position automatically taken up by the burner when a particular part of
the burner or the system is inefficient. Therefore, it is good practice,
before unblocking the burner and starting it up again, to check that
there are no defects in the heating plant. The burner may stay in
the lock position without any time limits.
To unlock press the appropriate push-button (reset). Blocks can be
caused by transitory flows (a little water in the fuel, air in the pipes,
etc.); in these cases, if unblocked, the burner will start up normally.
When, however, blocks occur repeatedly (3 or 4 times), do not keep
on trying to unblock the burner, first check that there is fuel in the tank
and then call the Technical Assistance Service to repair the defect.
MAINTENANCE
Burners do not require particular servicing, however it is good
practice that authorised personnel performs the following operations,
at least at the end of the heating season:
• Periodically check that the gas filter is clean for gas burners.
• In order to clean the combustion head, its components must
be disassembled.
Take care during reassembly that the ignition electrode is correctly
positioned, checking that the spark jumps only between the electrode
and the central drilled pilot flame disk.
AIR REGULATION ON THE
COMBUSTION HEAd
The combustion head is equipped with a device that automatically
regulates the passage between the diffusor disk and the head,
admitting combustion air to the head.
This passage can be restricted to obtain high pressure upstream
of the diffusor disk, even with low fuel throughput, so that high
velocity and turbulence ensure that the air penetrates the gas
more thoroughly, giving an optimum fuel/air mixture and a stable
flame. With gas burners, it can be essential to have high air
pressure on the diffusor inlet side if pulsation of the flame is to be
prevented, especially where the burner operates in a high pressure
combustion chamber, or in high thermal load conditions.
Accordingly, the head must be adjusted in such a way that a
substantially high pressure is always generated behind the disk.
It is recommended that the passage of air allowed through to the
head be restricted in such a way that there is a generous opening
of the air shutter regulating the air flow supplied by the burner fan.
To achieve this, adjust the screws on the modulation disk. When
the regulation is complete, remember to tighten the screws locking
the regulator screws.
Summary of Contents for 66875410
Page 2: ......
Page 37: ...35 42 0006080764 _201312 ITALIANO schema elettrico...
Page 38: ...36 42 0006080764 _201312 ITALIANO...
Page 39: ...37 42 0006080764 _201312 ITALIANO...
Page 40: ...38 42 0006080764 _201312 ITALIANO...
Page 41: ...39 42 0006080764 _201312 ITALIANO...
Page 42: ...40 42 0006080764 _201312 ITALIANO...
Page 43: ...41 42 0006080764 _201312 ITALIANO RAMPA PILOTA RAMPA PRINCIPALE...
Page 46: ...2 42 0006080764 _201312 ENGLISH...
Page 79: ...35 42 0006080764 _201312 ENGLISH Wiring diagram...
Page 80: ...36 42 0006080764 _201312 ENGLISH...
Page 81: ...37 42 0006080764 _201312 ENGLISH...
Page 82: ...38 42 0006080764 _201312 ENGLISH...
Page 83: ...39 42 0006080764 _201312 ENGLISH...
Page 84: ...40 42 0006080764 _201312 ENGLISH...
Page 85: ...41 42 0006080764 _201312 ENGLISH PILOT TRAIN MAIN TRAIN...
Page 87: ......