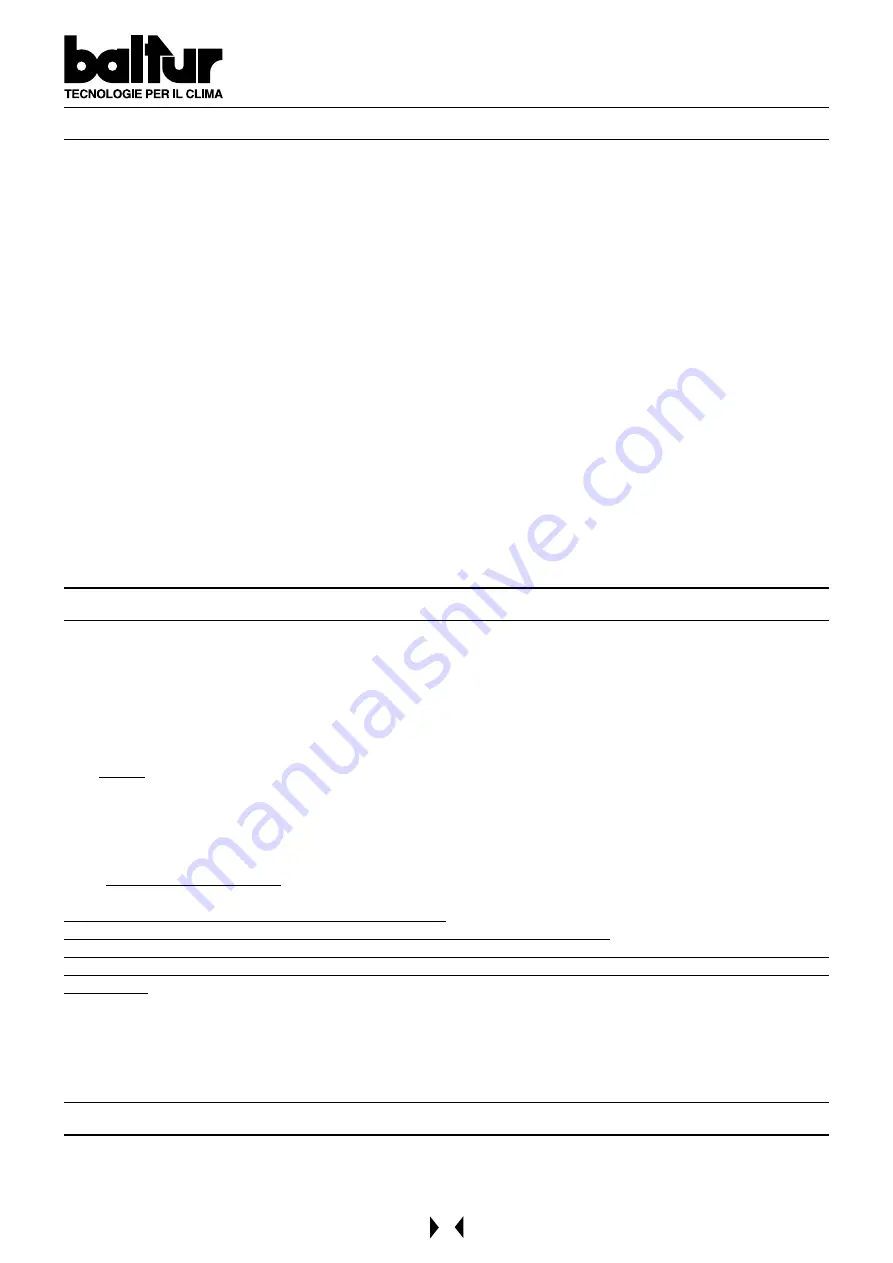
12
CHECKS
After starting up the burner, check the safety devices (photoresistant cell, shut down system, thermostats).
1)
The photoresistant cell is the flame control device and, if the flame should be extinguished during operations, it
must be capable of intervening (this check should be made at least one minute after start up).
2)
The burner should be capable of blocking itself (shut down), and remaining so, when the flame does not appear
regularly during the starting phase within the time limit pre-set on the control box. The shut down causes the
immediate arrest of the motor and therefore the burner and the red warning light is turned on. To check the
efficiency of the photoresistant cell and of the shut down system, proceed as follows:
a)
Start up the burner.
b)
About one minute after ignition, extract the photoresistant cell by pulling it out of its seat and simulate
flame failure (using a rag to close the window in the photoresistant cell support). The burner flame
should be extinguished.
c)
Keep the photoresistant cell in the dark and the burner will start up again but, as the
photoresistant cell does not see the light, the burner will go to shut down within the time pre-set by the
programmer.
The control box can only be unblocked by pressing manually on the appropriate push-button.
Check the shut down efficiency at least twice.
3)
To check thermostat efficiency, run the burner until the water in the tank reaches a
temperature of at least 50 °C. Then turn the thermostat control knob, to lower the water temperature, until an
opening click is heard which causes the burner to stop.
The thermostat should trip within a maximum tolerance of 5 to 10 °C in respect to the control thermostat (boiler
thermostat); if not, change the setting on the thermostat scale to match that of the thermometer.
AIR REGULATION ON THE COMBUSTION HEAD (see BT 8608/3)
The combustion head is fitted with a regulating device which closes (by moving forwards) and opens
(by moving backwards) the air passage between the disk and the head.
By closing the passage it is possible to achieve high pressure upstream the disk for low outputs as well. High velocity
and air turbulence ensure a better penetration in the fuel, an optimum mixture and good flame stability. It might be
necessary to have high air pressure upstream the disk in order to avoid flame pulsation’s and it is considered practically
indispensable when the burner is operating with a pressurized furnace and/or high thermal load.
It is evident from the above, that the device which closes the air on the combustion head should be put in such a position
as to always obtain a decidedly high air pressure value behind the disk.
It is advisable to regulate in such a way as to achieve a closing of the air on the head; this will necessitate a considerable
opening of the air shutter which regulates the flow to the burner’s fan suction. Obviously these adjustments should be
carried out when the burner is operating at maximum delivery desired. In practice, start regulating by putting the device
which closes the air on the combustion head in an intermediate position, start up the burner and make trial adjustments
as previously described.
When maximum delivery required has been reached, proceed with correcting the position of the device which closes the
air on the combustion head; move it backwards or forwards in such a way as to obtain an air flow suitable for the delivery,
with the air regulation shutter in suction considerably open.
When reducing the air passage on the combustion head, avoid closing it completely.
Proceed with perfect centering with respect to the disk. It must be pointed out that, if perfect centering with respect to
the disk is not obtained, bad combustion and excessive heating of the head could occur which would result in its rapid
deterioration.
A control can be carried out by looking through the spy hole situated at the back of the burner.
Note:
Check that ignition occurs regularly, because when the device has been moved forwards, it
could occur that the air velocity in exit is so high as to render ignition difficult.
If this happens, move it backwards, gradually, until it reaches the correct position and ignition occurs regularly.
This position should be definitive.
SETTING THE DISTANCE BETWEEN THE DISK AND THE NOZZLE
Burners are fitted with a device which permits to change the distance between the disk and the nozzle.
The distance between the disk and the nozzle is set in the factory, and it should be reduced only if the atomized fuel cone
coming out of the nozzle wets the disk and fouls it up.
Summary of Contents for BT 180 DSG
Page 15: ...15 GENERAL DIAGRAM AIR REGULATION N 8608 3...
Page 18: ...18 POMPA BALTUR MODELLO BT BALTUR PUMP MODEL BT BOMBA BALTUR MODELO BT N 0002900580...
Page 23: ......
Page 24: ......
Page 25: ......
Page 26: ......