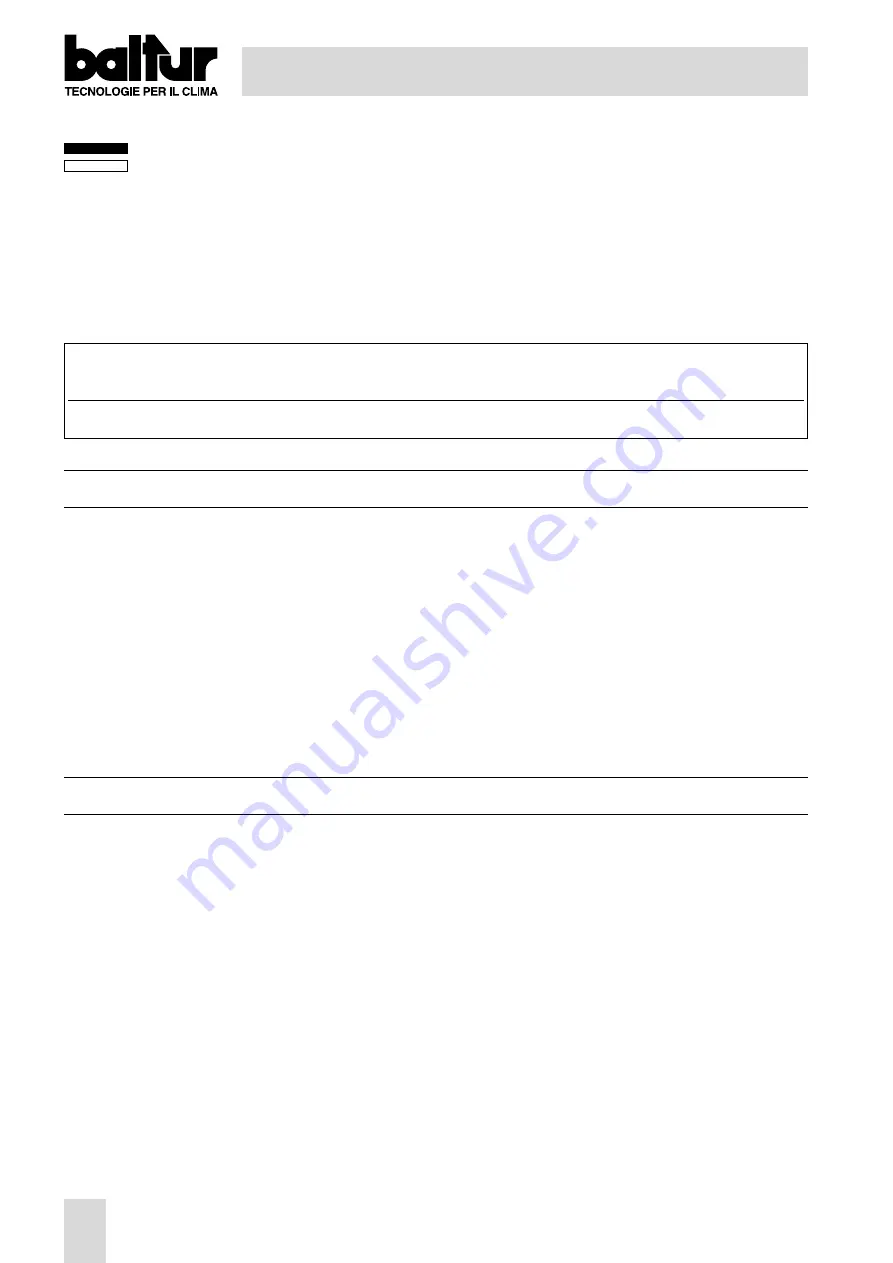
18
ONE STAGE LIGHT OIL BURNERS
Program Legend
Control-box output signals
Input signals required
A’ Beginning of starting cycle for burners
with light-oil pre-heater “OH”
A Beginning of starting cycle for burner
without light-oil pre-heater
B Flame presence
C Normal operation
D Adjustment stop by “R”
tw Light-oil pre-heating time until operation consent
by contact “OW” (minimum thermostat)
t1 Pre-ventilation time
t3 Pre-starting time
t2 Safety time
t3n Post-starting time
t4 Time interval between flame presence and
connection of 2nd valve to terminal 5
1234567
1234567
Tension
Type
Safety at
Pre-ventilation
Pre-starting
Safety
Post-starting
Time
low voltage
time
Interval
V ~
t1
t3
t2max
t3n
BV1-BV2=t4
220/240
LOA 24.171B27
YES
13 s
13 s
10 s
15 s
15 s
PREPARATIONS FOR START UP
Control that the nozzle applied is suitable for the boiler potentiality. The table shows the delivery rates in kg/h of
light oil with respect to the nozzle size and the pump pressure (normally 12 bar). It should be remembered that 1
kg of light oil is equivalent to approximately 10.200 kcal). Make sure that the return pipe in the tank has no
obstructions, e.g. gate valves, closed plugs etc. Any eventual obstruction would cause a breakage in the sealing
surface situated on the pump shaft. Close the main switch and the boiler thermostats in order to start up the motor
and the ignition transformer. Upon completion of the pre-ventilation time, the solenoid valve is activated. the
electrovalve will cut in and expose the photoresistant cell to a source of light until the burner stops (shut down).
When the pipelines have been filled up (and when fuel has come out of the nozzle), stop the burner and put the
photoresistant cell back in its seat.
NOTE: Should it be necessary to purge air, this can be done by loosening the special fitting which the pump is
provided with (see 0002901310). Do not illuminate the photoresistant cell before the electric valve has cut
in because, in this case, the control box will go to “shut down”.
IGNITION AND ADJUSTMENT
Loosen the lock screw “C” (see 0002934112); act on the screw “A”; bring the air regulation damper into
the necessary position as indicated by index “B”. Turn the main switch to ON to power the burner and
thus ignite it. Correct, if necessary, combustion air delivery by acting on the intake damper and the
position of the deflector disk (adjustable via screw D). The burner is, in fact, fitted with a special screw
to adjust the position of the deflector disk; this device allows for optimisation of combustion by
reducing or increasing the air flow between deflector disk and head. It is normally necessary to reduce
the air flow between deflector disk and head when there is reduced fuel delivery: this passage must be
proportionately more open when the burner is working with a higher fuel delivery rate. After modifying
the position of the deflector disk it is, usually, necessary to correct the air damper positions and
afterwards check for proper ignition.
Summary of Contents for BTL 20
Page 2: ......