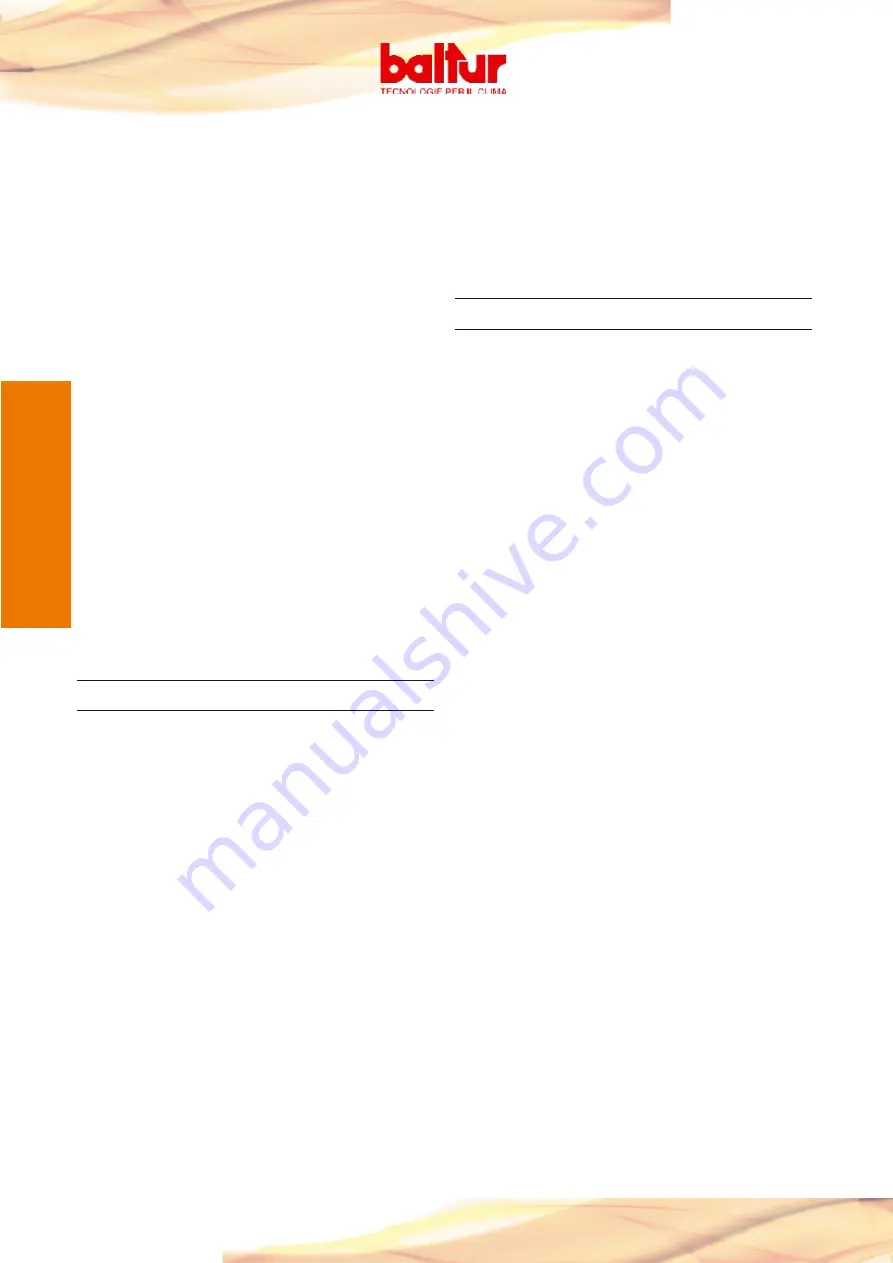
10 / 87
0006081047_200802
E
N
G
L
I
S
H
return the pressure switch setting to a sufficient value to detect
the existing air pressure during the preventilation stage.
13) The minimum and maximum gas pressure control switches
have the aim of preventing the burner from working when
the gas pressure goes outside the preset limits. It is clear
from the specific function of the pressure switches that the
pressure switch that controls the minimum pressure must use
the contact that is closed when the pressure switch detects a
higher pressure than that of the preset value. The maximum
pressure switch must use the contact that is closed when the
pressure switch detects pressure below that of the preset value.
The adjustment of the minimum and maximum gas pressure
switches must therefore take place when the burner is being
tested, according to the pressure found from time to time.
The action of any of the gas pressure switches (the opening
of a circuit) will thus not permit the equipment, and hence the
burner, to be switched on. When the burner is running (flame
on), the action of the gas pressure switches (opening the
circuit) causes the immediate arrest of the burner. When the
burner is being set up and tested it is essential to check the
proper working of the pressure switches. Using the respective
regulators, the pressure switch (opening of the circuit) must
be seen to intervene to stop the burner. (see also the enclosed
ETAMATIC instructions).
14) Check the flame detector works (infra red cell) with the system
already on, remove it from its position on the burner and check that
the system goes into “lock-out”.
15)Check the boiler’s thermostats or pressure switches are working
properly (when triggered the burner must stop).
QUICK GUIDE TO PROGRAMMING
Connect the keyboard “Operating unit” to the ETAMATIC OEM
equipment by means of the special cable provided. “Status” is
written on the keyboard display
The working of keys in “status” mode. Press the keys in the “sta
-
tus” position for the following functions:
F2 = hours of working of the burner
F3 = manual (vary loading by means of keys 2-3)
F4 = flame quality (%)
F1 = to return to “status” or to release the burner
2-3 = to view the last 10 lock-out codes.
Function of “level 1” mode keys with the password “0000”
F2-F3 = PARM: parameters
O2 EI: adjustment of O2 curve (enabled only with
parameter 896=1)
AUTO: automatic
EINS: curve points calibration
SPLO: cancel current curve
17-16 = Status: shows the burner mode loading (use keys 2-3 to
change the loading) set value: setting (use the keys for the
channel you want to change from 2 to 9) actual return: di
-
splays the current channel in digits setpo return: displays
set-point channel in digits Dig. Input: digital inputs (indi
-
cates digital control input)
Using the blue keys indicated below you can change the digits
for each channel used, the odd keys increase the value and the
even keys decrease the value.
2-3 = CH1: channel 1 (INVERTER)
4-5 = CH2: channel 2 (COMBUSTION HEAD) (OIL , for mixed
burners)
6-7 = CH3: channel 3 (FUEL)
8-9 = CH4: channel 4 (AIR)
BURNER ADJUSTMENT
1. With the burner off (I-0 burner switch “closed”, thermostat switch
“open”) press buttons 5-7-8 at the same time and the PAS-
SWORD level 1 (0000) will appear, press button 11 to confirm,
press F3 twice to enter in “cancel memory” (SPLO) mode,
press button 11 to cancel the current curve and the word “can
-
celled” will appear.
2. Press F2 to enter in Setting EINS) mode: curve points calibration
Close the thermostat switch, to switch on the burner, the ETA
-
MATIC OEM equipment will carry out a self check and check
parameters. When this is happening you must never carry out
any operation; at the end of the self check the Operating unit
display will show the “STATUS” position
3. The ETAMATIC OEM equipment will start the ignition cycle by
carrying out preventilation, taking all servo motors to maximum
opening and the pre-ventilation time will be counted out (30
seconds). At the end of this phase all the servo motors will
come to the minimum opening position and the display will say
“please set ignition point”.
4. Press button 16 and display will read loading “2 SZP” , press
button 16 again to go to “calibration” mode and the display will
show “set value EINS”. At this point, using buttons 2 to 9 you can
adjust the positions of channels 1 to 4, press button 11 to store
in memory and the display will read “can be switched on” , press
button 11 again to switch on.
5. In the burner is in a lock-out state, (with top left symbol flashing)
press F1 and repeat the procedure from point 1.
6. Once the burner is on, bring the loading up to 200 digits (burner
working minimum position): press button 17, then button 3 until
200 is shown
7. Press button 16 to return to “calibration”, adjust the positions
of channels 1 to 4 using buttons 2 to 9 and press button 11 to
store in memory.
8. Bring the loading up to 990 digits (maximum burner working posi
-
tion): press button 17 , then button 3 until 990 is displayed
9. Press button 16 to return to “calibration”, adjust the positions
of channels 1 to 4 , using buttons 2 to 9, press button 11 to
store in memory.
10. Now adjust the intermediate points by bringing the loading respec
-
tively to 900-800-700-600-500-400 and 300 digits and changing
the positions of the channels 1 to 4, using buttons 2 to 9. After the
calibration of each point press button 11 to store in memory.
11. When you have finished the above adjust
-
m e n t s , p r e s s F 2 t o s t o r e t h e w h o l e c u r v e
Summary of Contents for GI 350 ME
Page 2: ......
Page 4: ......
Page 24: ......
Page 63: ......
Page 83: ...81 87 0006081047_200802 ...
Page 84: ...82 87 0006081047_200802 ...
Page 85: ...83 87 0006081047_200802 ...
Page 86: ...84 87 0006081047_200802 ...
Page 87: ...85 87 0006081047_200802 ЭЛЕКТРИЧЕСКАЯ СХЕМА GI 350 510 ME С ETAMATIC OEM ...