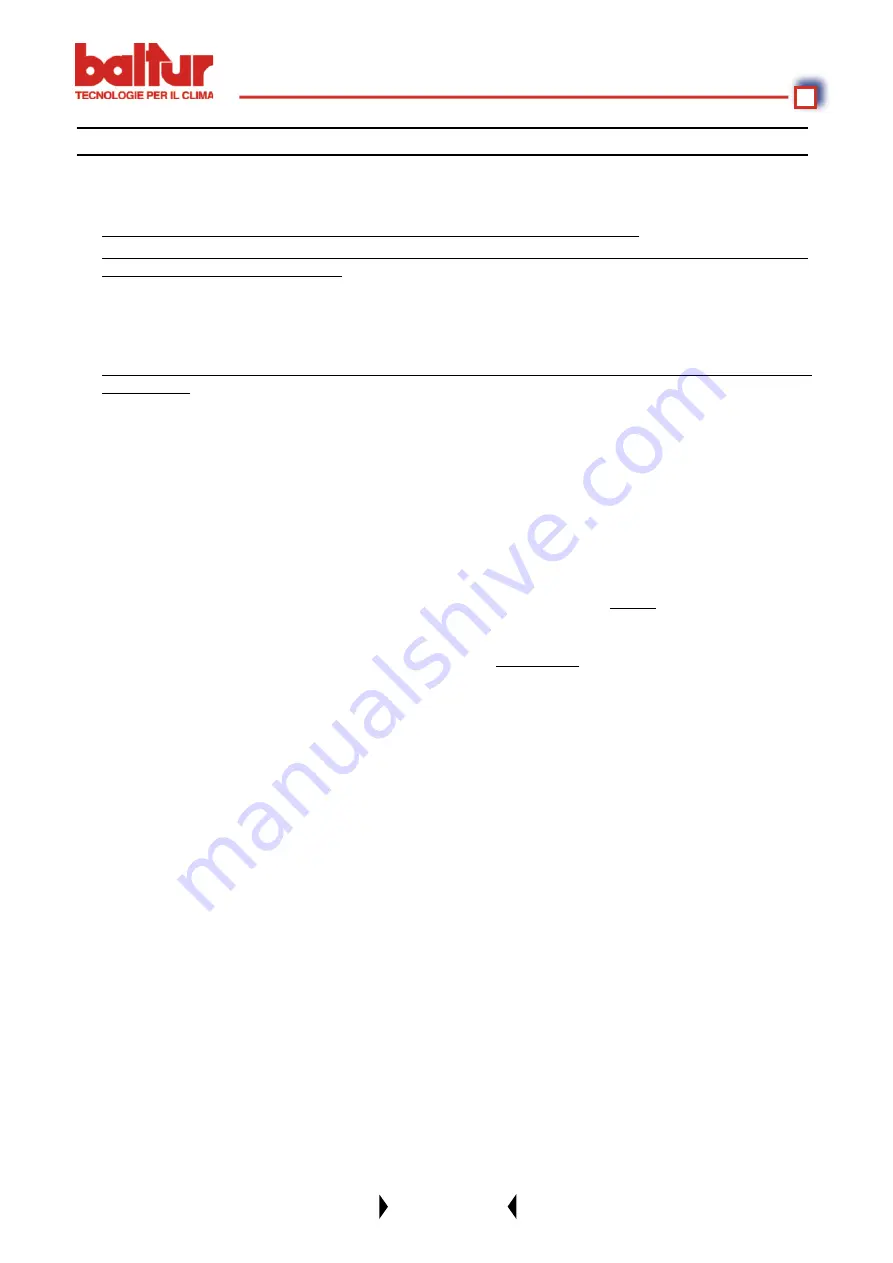
19 / 61
0006080103 ed2005/10
STARTING UP AND REGULATION WITH LIGHT OIL
1) Check that the characteristics of the nozzle (delivery and spray angle) are suitable for the furnace
(see BT 9353/1). If not, replace it.
2) Check that there is fuel in the cistern and that it is, at least visually, suitable for the burner.
3) Check that there is water in the boiler and that the system’s gate valves are open.
4) Check, with absolute certainty, that the discharge of combustion products can take place freely (boiler and
chimney lock-gates should be open).
5) Make sure that the voltage of the electric line to which the burner is to be connected, corresponds to that
required by the manufacturer, and that the motors electrical connections have been correctly prepared to
match the voltage rating available. Also check that all the electrical connections carried out on the spot are
in accordance with our electric wiring diagram.
6) Make sure that the combustion head is long enough to enter the furnace to the extent specifi ed by the boiler
manufacturer. Check that the air regulation device on the combustion head is in the position considered ne-
cessary for the fuel delivery required (the air passage between the disk and the head should be considerably
closed when the fuel delivery is relatively reduced; on the other hand, when the nozzle has a fairly high
delivery, the air passage between the disk and the head should be relatively open (see chapter “Regulation
of the Combustion Head).
7) Remove the protective cover from the rotating disk inserted on the servomotor regulating delivery (fuel/air).
On this disk have been fi tted adjustable screws which are used to control the fuel and the relative combustion
air.
8) Put the two modulating switches in the “MIN” (minimum) and “MAN” (manual) position.
9) Start up the fuel supply auxiliary circuit, check its effi ciency and regulate the pressure at about 1 bar
(if thecircuit is supplied with a pressure regulator).
10) Remove from the pump the vacuumeter connection point plug and then open slightly the gate valve fi tted on
the fuel arrival pipe. Wait until the fuel comes out of the hole, without air bubbles, and then re-close the gate
valve.
11) Insert a manometer (end of the scale about 3 bar) into the vacuumeter connection point on the pump and
control the value of the pressure at which the fuel arrives at the burner pump. Insert a manometer (end of the
scale 30 bar) into the manometer connection point provided on the pump and control it’s working pressure.
Insert a manometer (end of the scale about 30 bar) into the special connection point of the nozzle return
pressure regulator (see BT 8714/1) in order to control the return pressure.
12) Now open all the gate valves and any other interception devices fi tted on the light oil pipelines.
13) Put the switch on the control panel in the “O” (open) position and give current to the electric lines which the
burner is connected to. Check, by pressing manually the relative relay, that the fan and pump motors rotate
in the right direction. If they do not, exchange the places of two cables of the principle line in order to inverse
the sense of rotation.
14) Start operating the burner pump by pressing manually on the relative relay until the manometer, which mea-
sures the working pressure of the pump, indicates a slight pressure. The presence of low pressure in the
circuit confi rms that fi lling up has taken place.
15) Insert the switch on the control panel to give current to the control box. If the thermostats (safety and boiler)
are closed, the control box’s programmer will be connected and will insert the burner’s component devices
according to its pre-established programme. The unit starts up in this way, as described in Chapter “Descrip-
tion of Operations”.
16) When the burner is operating at “minimum”, proceed with regulating the air to the quantity considered ne-
cessary to ensure good combustion. Tighten more or loosen more the adjusting screws in correspondence
to the point of contact, with the lever which transmits the movement to the combustion air regulation shutter.
It is preferable that the quantity of air for the “minimum” is slightly reduced, in order to ensure a soft ignition
even in the most critical conditions.
17) After having regulated the air for the “minimum”, put the modulation switches in the “MAN” (manual) and
“MAX” (maximum) positions.
Summary of Contents for GI MIST 350 DSPGM
Page 40: ......
Page 41: ......
Page 42: ......
Page 43: ......
Page 44: ......
Page 45: ......
Page 46: ......
Page 47: ......
Page 48: ......
Page 49: ......
Page 50: ......
Page 51: ......
Page 52: ......
Page 53: ......
Page 54: ......
Page 55: ......
Page 56: ......
Page 57: ......
Page 58: ......
Page 59: ......