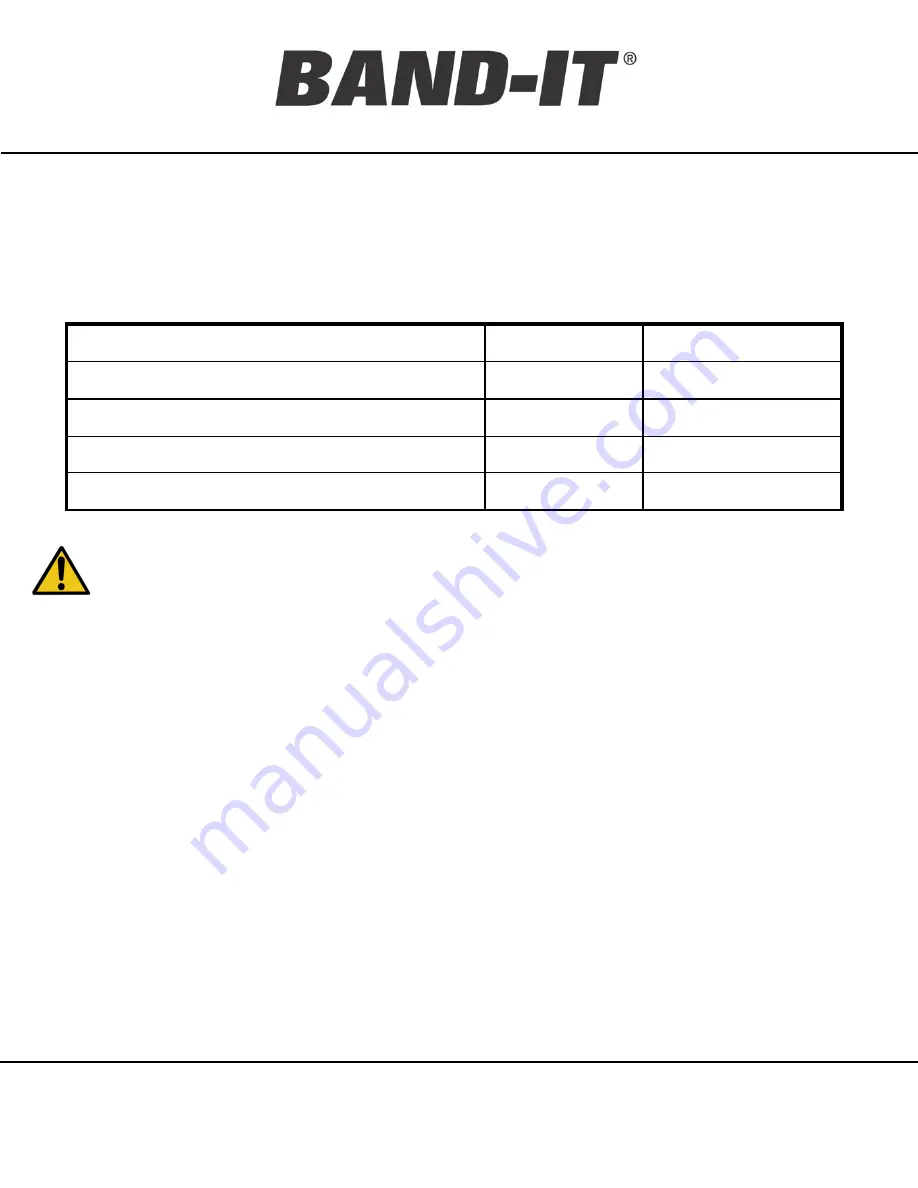
IT5000-C / IT6000-C
3/8” IT Tool
www.BAND-IT-IDEX.com
Document # P48850 Rev. C
© Copyright
BAND-IT-IDEX, Inc. 2015
All rights reserved
Page 10 of 36
BAND-IT-IDEX, Inc.
A Unit of IDEX Corporation
4799 Dahlia Street
Denver, CO 80216-3070 USA
P: 1-800-525-0758
F: 1-800-624-3925
Operating
Manual
For proper tool performance, the incoming compressed air requirements to the BAND-IT Air
Controller Module of the 3/8” BAND-IT Pneumatic IT Tool must be:
Item
Min
Max
Inlet Supply Pressure in PSI (kPa)
100 (690)
150 (1,034)
Inlet Supply Air Flow in SCFM (L/min)
1.5 (0.71)
Filtered air particle size (microns)
(5)
Air Moisture Content
20% RH
Although cylinders are permanently lubricated,
premature wear can be caused by
contaminants in the air supply or the presence of water and oil
. The tool’s internal
valves can also be affected by contaminants in the air lines causing a valve malfunction.
The BAND-IT Air Controller Module includes a filter to meet particle requirements.
BAND-IT recommends the use of an Air Booster System to address the potential problems
associated with low air supply, including:
•filters and dries the air supply
•assures pressure of 100 PSI (690 kPa)
Contact BAND-IT-IDEX Customer Service at 1-800-525-0758 or 303-320-4555 for more
information.
Warning
- Failure to follow the below specifications may cause significant damage to
internal tool components.
Air System Requirements