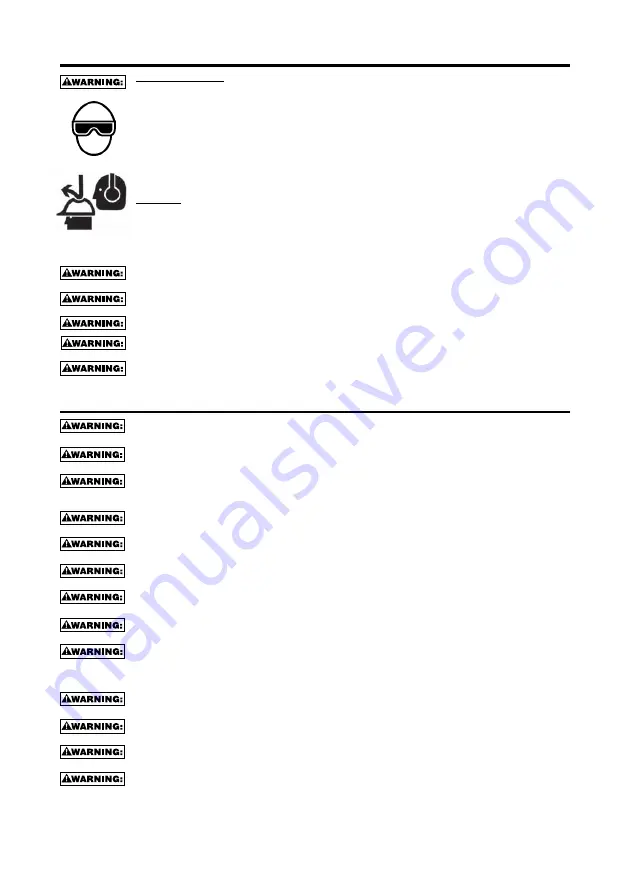
-3-
SAFETY INSTRUCTIONS
EYE PROTECTION which conforms to ANSI specifications and provides protection against
flying particles both from the FRONT and SIDE should ALWAYS be worn by the operator and
others in the work area when connecting to air supply, loading, operating or servicing this
tool. Eye protection is required to guard against flying fasteners and debris, which could
cause severe eye injury.
The employer and/or user must ensure that proper eye protection is worn. Eye protection
equipment must conform to the requirements of the American National Standards Institute,
ANSI Z87.1 and provide both frontal and side protection.
NOTE: Non-side shielded spectacles and face shields alone do not provide adequate
protection.
CAUTION: Additional Safety Protection will be required in some environments. For example,
the working area may include exposure to noise level which can lead to hearing damage.
The employer and user must ensure that any necessary hearing protection is provided and
used by the operator and others in the work area. Some environments will require the use
of head protection equipment. When required, the employer and user must ensure that head
protection conforming to ANSI Z89.1 is used.
Stay alert, watch what you are doing and use common sense when operating a power tool.
Do not use tool while tired or under the influence of drugs, alcohol, or medication.
Dress properly. Do not wear loose clothing or jewelry. Contain long hair. Keep your hair,
clothing, and gloves away from moving parts.
Keep fingers away from trigger when not driving fasteners to avoid accidental firing.
Do not overreach. Keep proper footing and balance at all times. Proper footing and balance
enables better control of the tool in unexpected situations.
Do not use on a ladder or unstable support. Stable footing on a solid surface enables better
control of the tool in unexpected situations.
SERVICE
Tool service must be performed only by qualified repair personnel. Service or maintenance
performed by unqualified personnel may result in a risk of injury.
When servicing a tool, use only identical replacement parts. Use of unauthorized parts may
create a risk of injury.
Know your pneumatic tool. Read operator's manual carefully. Learn its applications and
limitations, as well as the specific potential hazards related to this tool. Following this rule
will reduce the risk of electric shock, fire, or serious injury.
Always wear safety glasses with side shields. Everyday glasses have only impact resistant
lenses. They are NOT safety glasses. Following this rule will reduce the risk of eye injury.
Protect your lungs. Wear a face or dust mask if the operation is dusty. Following this rule
will reduce the risk of serious personal injury.
Protect your hearing. Wear hearing protection during extended periods of operation.
Following this rule will reduce the risk of serious personal injury.
Make sure the hose is free of obstructions or snags. Entangled or snarled hoses can cause
loss of balance or footing and may become damaged.
Use the tool only for its intended use. Do not discharge fasteners into open air. Use the
pneumatic tool only for the purpose for which it was designed.
Use only the fasteners recommended for this tool. Use of the wrong fasteners could result
in poor fastener feeding, jammed fasteners, and nails leaving the tool at erratic angles. If
fasteners are not feeding smoothly and properly, discontinue their use immediately.
Jammed and improperly feeding fasteners could result in serious personal injury.
Never use this tool in a manner that could cause a fastener to be directed toward anything
other than the workpiece. Do not use the tool as a hammer.
Do not alter or modify this tool from the original design or function without approval from
the manufacturer.
Always be aware that misuse and improper handling of this tool can cause injury to yourself
and others. Never leave a tool unattended with the air hose attached.
Do not operate this tool if it does not contain a legible warning label. Do not continue to use
a tool that leaks air or does not function properly.