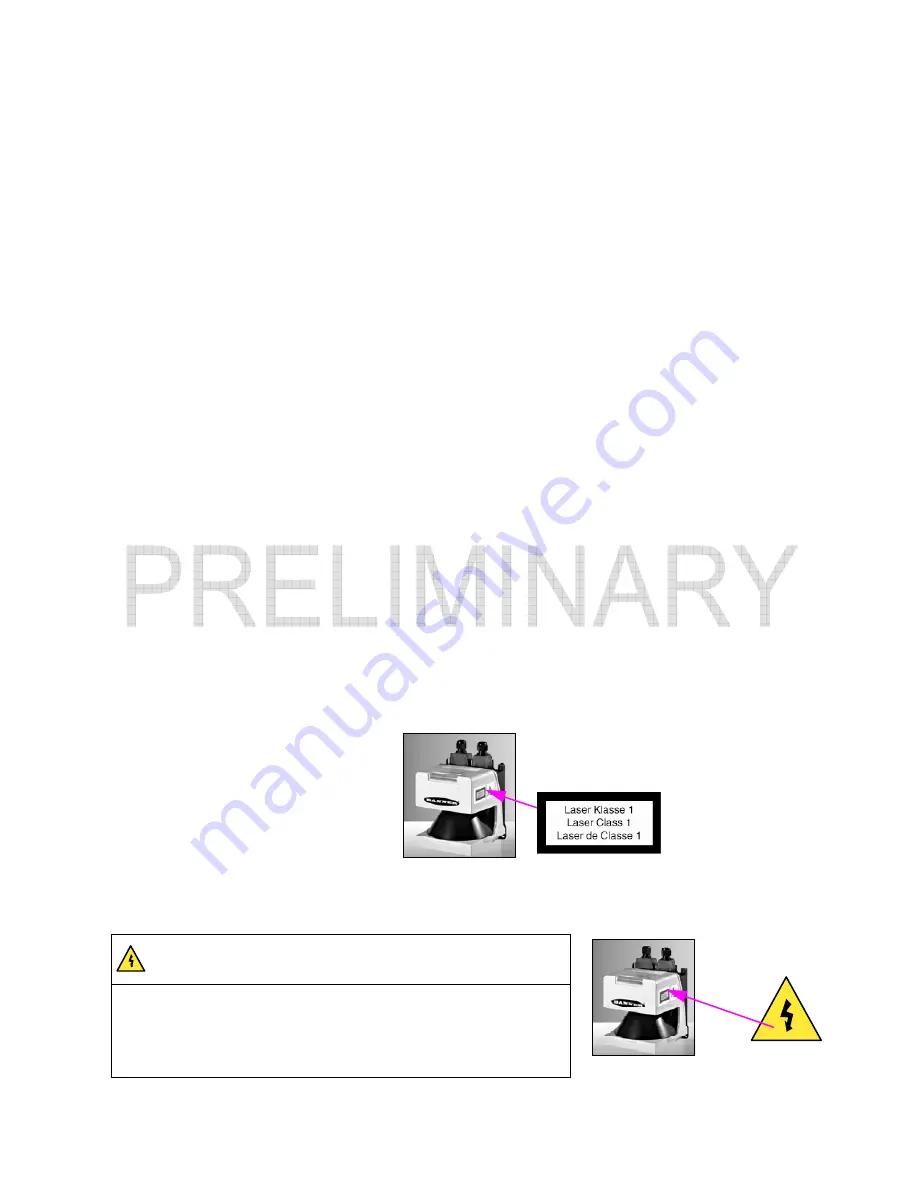
Banner AG4 Series Safety Laser Scanner
1.6.2 Qualified
Person
A
Qualified Person
, by possession of a recognized degree or certificate of professional training, or by extensive knowledge, training and
experience, has successfully demonstrated the ability to solve problems relating to the installation of the Scanner and its integration with the
guarded machine. In addition to everything for which the Designated Person is empowered, the
Qualified Person
is empowered to:
Install the Scanner
Perform all Scanner checkout procedures
Access and change both the Scanner’s configuration settings and the password for accessing the configuration program.
Reset the system
1.7
Responsibility for Safety
The responsibility for the proper use of the Scanner and compliance with the regulations and directives that apply in the country of use lies with
the machine's manufacturer and operator.
The machine manufacturer is responsible for:
•
The safe design and construction of the machine.
•
The safe implementation of the Scanner.
•
The provision of all relevant information to the operator.
•
Compliance with all regulations and directives for safely putting the machine into operation.
The machine operator/supervisor is responsible for:
•
Instructing the operator.
•
Maintaining the safe operation of the machine.
•
Compliance with all occupational health and safety at work regulations and directives.
Passwords
Improperly set parameters on the Scanner can cause serious accidents. The configuration of the Scanner is therefore protected by passwords.
Ensure that the passwords are kept locked away by the security officer.
The people responsible for the machine's safety must ensure that the appropriately Qualified Person can properly perform the tests and
work on the machine and the Scanner in accordance with their intended use.
1.8
Laser
The Scanner has a Class 1 laser. Under normal
conditions, no special precautions are necessary when
working with or handling a Class 1 laser. Observe the
applicable legal and local regulations for operating laser
equipment.
Figure 6. Laser Safety Sticker and Location
1.9
High Voltage
WARNING . . . HIGH VOLTAGE EXISTS INSIDE THE AG4.
Do not open the AG4 with power applied. In connection with fault diagnosis or repair,
such as screen replacement, the unit should only be opened by a
Qualified Person
.
Otherwise return the Scanner to the factory for repair or replacement. Failure to
observe this warning could result in serious injury or death.
Figure 7. High Voltage Safety Sticker and Location
Product Manual
P/N 144924 05/2009
11