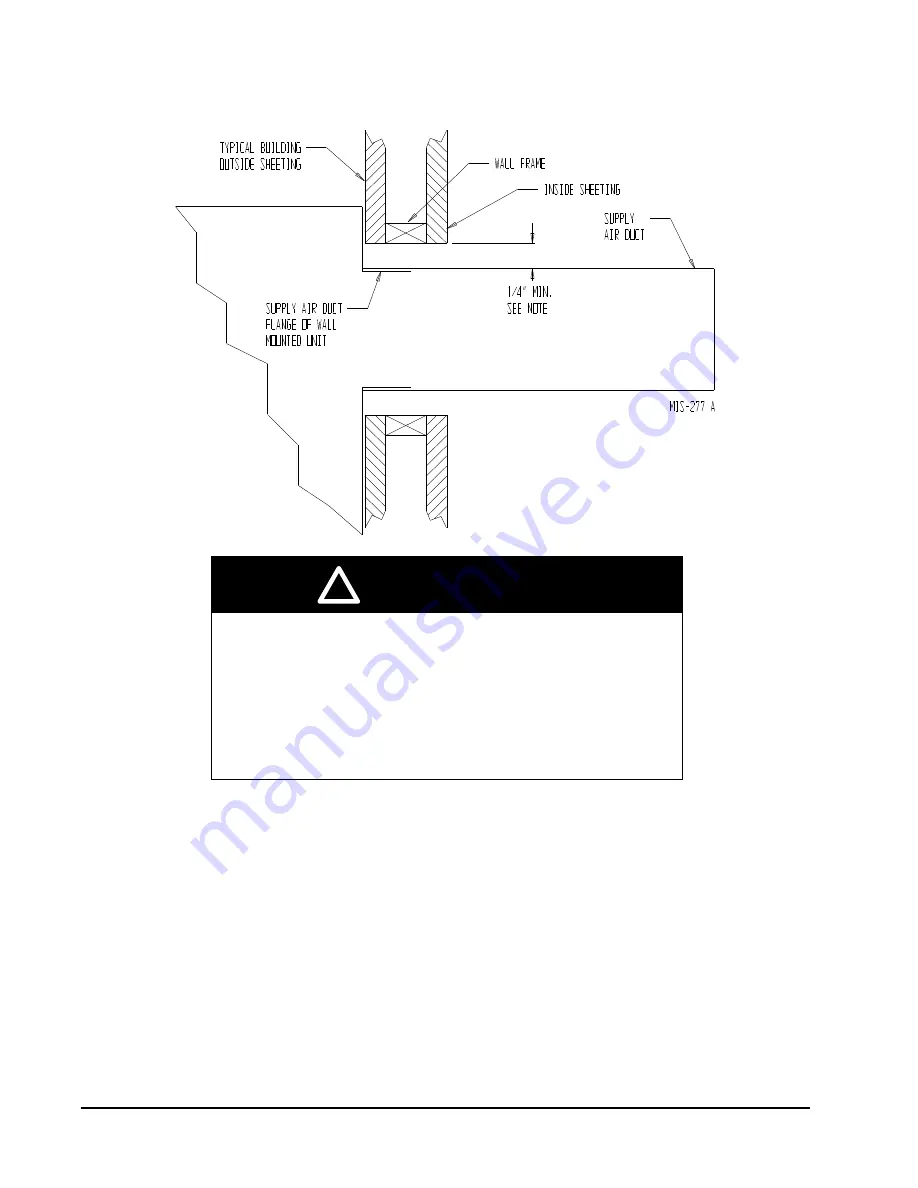
Manual 2100-646
Page
12 of 26
!
WARNING
A
minimum
of 1/4" clearance must be maintained between the
supply air duct and combustible materials. This is required for the
first 3' of ducting.
It is important to insure that the 1/4" minimum spacing is
maintained at all points.
Failure to do this could result in overheating the combustible
material and may result in a fire causing damage, injury or death.
FIGURE 6
Electric Heat Clearance
WIRING – LOW VOLTAGE WIRING
All 230/208V 1 phase and 3 phase equipment have
dual primary voltage transformers. All equipment
leaves the factory wired on 240V tap. For 208V
operation, reconnect from 240V to 208V tap. The
acceptable operating voltage range for the 240 and
208V taps are:
TAP RANGE
240
253 – 216
208
220 – 187
NOTE:
The voltage should be measured at the field
power connection point in the unit and while
the unit is operating at full load (maximum
amperage operating condition).
For wiring size and connections, refer to MV5000
Controller Manual 2100-636.
NOTE:
Side section view of supply air duct
for wall mounted unit showing 1/4"
clearance to combustible surfaces.