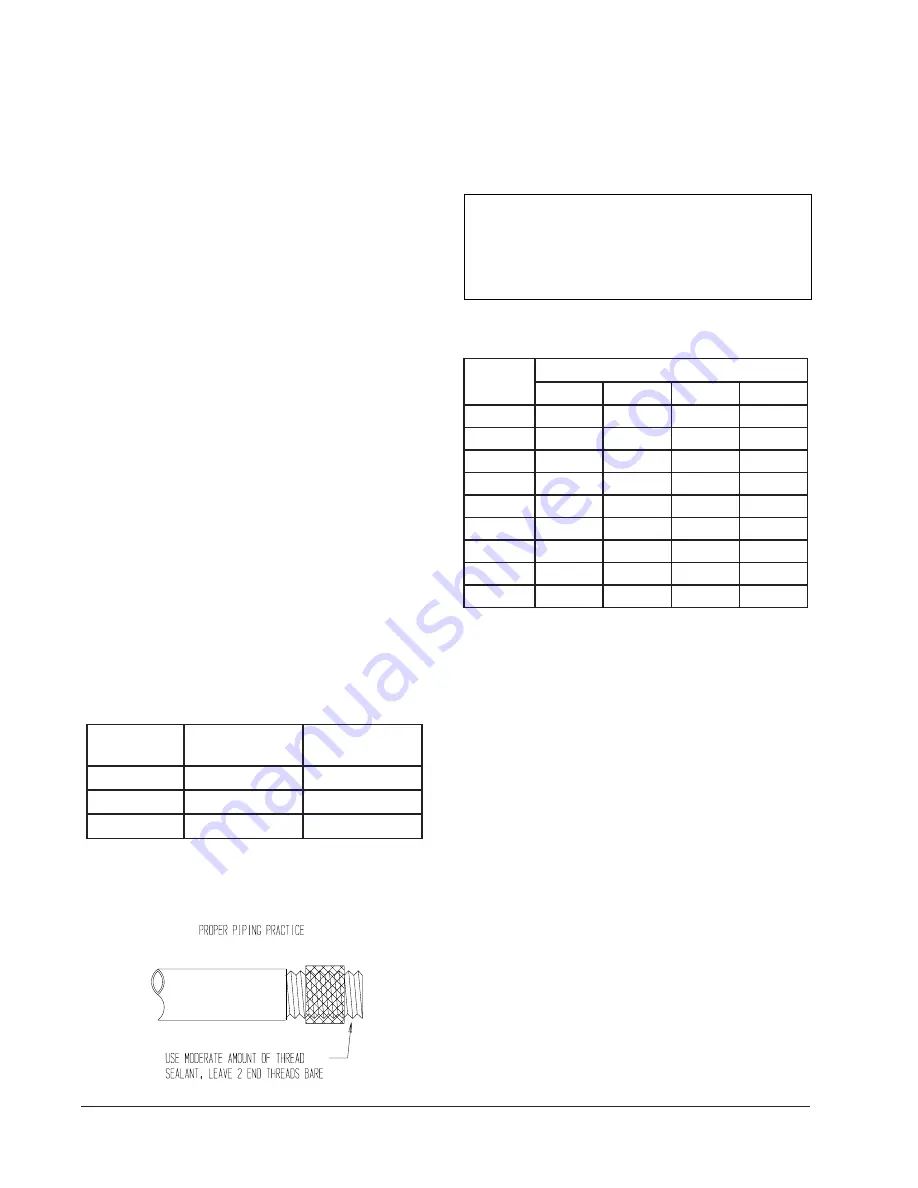
Manual
2100-486D
Page
21 of 37
17. GAS SUPPLY AND PIPING
GENERAL RECOMMENDATIONS
1. Be sure the gas line complies with the local codes
and ordinances, or in their absence with the National
Fuel Gas Code, ANSI Z223.1, or Natural Gas
Installation Code, CAN/CGA B149.1, or Propane
Installation Code B149.2, latest edition.
2. A sediment trap or drip leg must be installed in the
supply line to the furnace.
3. A ground joint union shall be installed in the gas line
adjacent to and upstream from the gas valve and
downstream from the manual shut off valve.
4. An 1/8" NPT plugged tapping accessible for test
gauge connection shall be installed immediately
upstream of the gas supply connection to the furnace
for the purpose of determining the supply gas
pressure. This can be omitted if local codes permit
use of plugged tapping in gas valve inlet.
5. Install listed manual shut off valve in the supply gas
line external to and immediately upstream of the
furnace. See Figure 12.
6. Use steel or wrought iron pipe and fittings.
7.
DO NOT
thread pipe too far. Valve distortion or
malfunction may result from excess pipe within the
control. Use pipe joint compound resistant to the
action of liquefied petroleum gases on male threads
only.
DO NOT
use Teflon tape. See Table 5 and
Figure 13.
TABLE 5
LENGTH OF STANDARD
PIPE THREADS (INCHES)
e
z
i
S
e
p
i
P
h
t
g
n
e
L
e
v
i
t
c
e
f
f
E
d
a
e
r
h
T
f
o
h
t
g
n
e
L
l
l
a
r
e
v
O
d
a
e
r
h
T
f
o
8
/
3
2
/
1
6
1
/
9
4
/
3
6
1
/
9
-
-
2
/
1
6
1
/
3
1
1
6
1
/
9
1
f
o
h
t
g
n
e
L
t
e
e
F
-
e
p
i
P
e
z
i
S
e
p
i
P
t
u
p
n
I
r
u
o
H
r
e
p
U
T
B
-
y
t
i
c
a
p
a
C
e
p
i
P
"
2
/
1
"
4
/
3
"
1
"
4
/
1
-
1
0
1
0
0
0
,
2
3
1
0
0
0
,
8
7
2
0
0
0
,
0
2
5
0
0
0
,
0
5
0
,
1
0
2
0
0
0
,
2
9
0
0
0
,
0
9
1
0
0
0
,
0
5
3
0
0
0
,
0
3
7
0
3
0
0
0
,
3
7
0
0
0
,
2
5
1
0
0
0
,
5
8
2
0
0
0
,
0
9
5
0
4
0
0
0
,
3
6
0
0
0
,
0
3
1
0
0
0
,
5
4
2
0
0
0
,
0
0
5
0
5
0
0
0
,
6
5
0
0
0
,
5
1
1
0
0
0
,
5
1
2
0
0
0
,
0
4
4
0
6
0
0
0
,
0
5
0
0
0
,
5
0
1
0
0
0
,
5
9
1
0
0
0
,
0
0
4
0
7
0
0
0
,
6
4
0
0
0
,
6
9
0
0
0
,
0
8
1
0
0
0
,
0
7
3
0
8
0
0
0
,
3
4
0
0
0
,
0
9
0
0
0
,
0
7
1
0
0
0
,
0
5
3
0
0
1
0
0
0
,
8
3
0
0
0
,
9
7
0
0
0
,
0
5
1
0
0
0
,
5
0
3
TABLE 6
GAS PIPE SIZES - NATURAL GAS
CHECKING THE GAS PIPING
Before turning gas under pressure into piping, all
openings from which gas can escape should be closed.
Immediately after turning on gas, the system should be
checked for leaks. This can be done by watching the 1/2
cubic foot test dial and allowing 4 minutes to show any
movement, and by soaping each pipe connection and
watching for bubbles. If a leak is found, make the
necessary repairs immediately and repeat the above test.
The furnace must be isolated from the gas supply piping
system by closing the manual shut off valve on the
combination gas control valve during pressure testing of
the gas supply piping system at pressures up to 1/2
PSIG. The furnace and its individual shut off valve must
be disconnected from supply piping and supply piping
capped during any pressure testing of supply piping
system at test pressures in excess of 1/2 PSIG.
Defective pipes or fittings should be replaced and not
repaired. Never use a flame or fire in any form to locate
gas leaks; use a soap solution.
After the piping and meter have been checked
completely, purge the system of air.
DO NOT
bleed air
inside the furnace.
Be sure to check and relight all the
gas pilots on other appliances that may have been
extinguished because of interrupted gas supply
.
FIGURE 13
PROPER PIPING PRACTICE
8. Refer to Table 6 for Gas Pipe Sizes for natural gas.
If more than one appliance is supplied from a single
line size, capacity must equal or exceed the
combined input to all appliances, and the branch
lines feeding the individual appliances properly sized
for each input.
MIS-897
THIS PRODUCT MUST BE GAS PIPED BY
A LICENSED PLUMBER OR GAS FITTER
IN THE COMMONWEALTH OF
MASSACHUSETTS.
Summary of Contents for WF0501-A
Page 13: ...Manual 2100 486D Page 13 of 37 FIGURE 6 COMMON WALL MOUNTING INSTALLATIONS...
Page 19: ...Manual 2100 486D Page 19 of 37 FIGURE 11 LOW VOLTAGE WIRING...
Page 20: ...Manual 2100 486D Page 20 of 37 FIGURE 12 GAS PIPE CONNECTION...
Page 34: ...Manual 2100 486D Page 34 of 37 230 208 60 1...
Page 35: ...Manual 2100 486D Page 35 of 37 115 60 1...