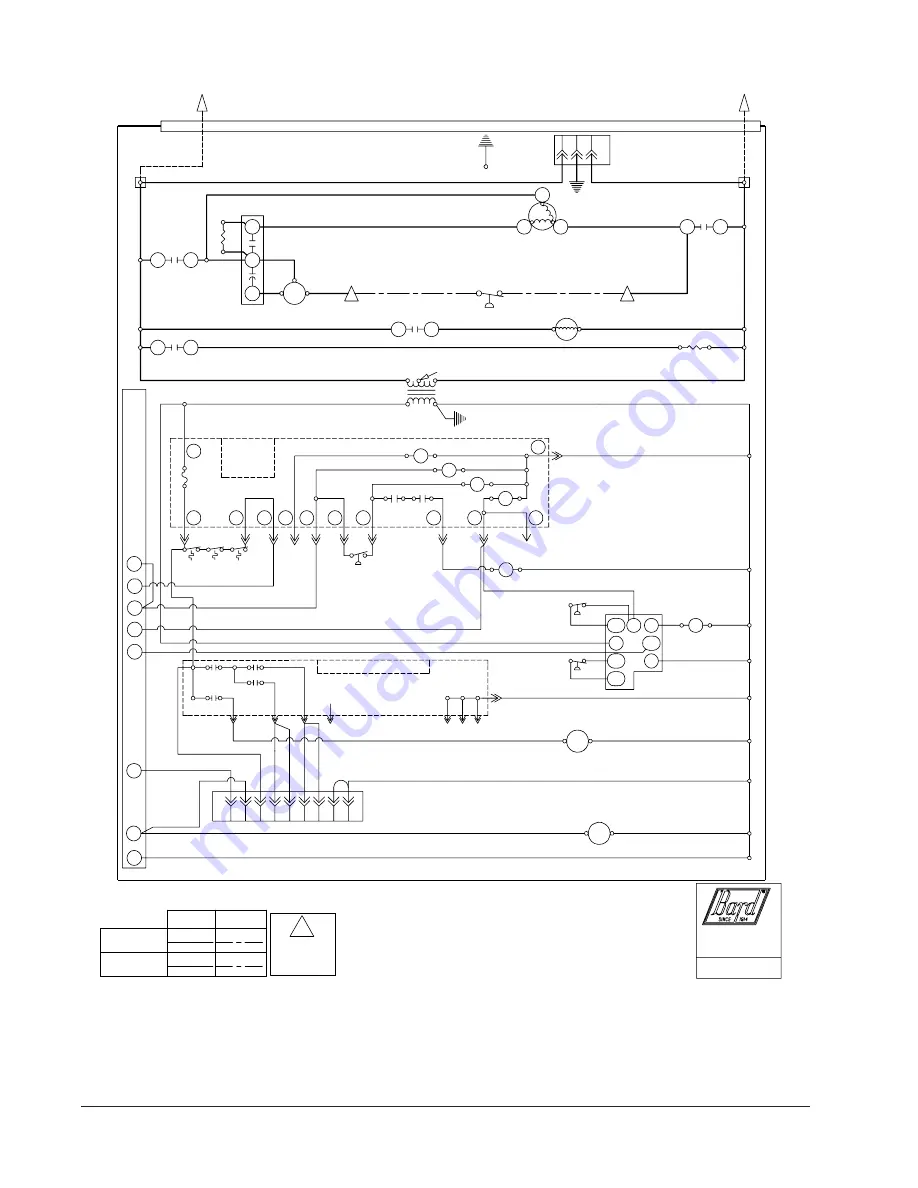
Manual
2100-483E
Page
51 of 59
WG3S1-A, WG4S1-A, WG5S1-A 208/230/60/1
if Option Not
A
Wires Connect
Used
Bard Mfg. Co.
Bryan, Ohio
4085-143 A
Indoor Blower Motor
14 12 10
6
2 13
3
1
16 Pin Plug for
15
W1
C
HEAT UNUSED
G
High Voltage
Optional
Low Voltage
Factory
CONTROL
INDUCED DRAFT
BLOWER RELAY
Y2
Contactor
Compressor
L2
T2
C
S
A
Compressor
Power Source
R
Crankcase
Line 2
230/208-60-1
for Indoor
Block
4
3
5
Ground
Ladder Diagram
Blower Motor
Terminal
A
Dual Can
Motor
H
F
C
T1
L1
Line 1
Low Vol
tage Term
. Bl
ock
C
Capacitor
Outdoor Fan
NC
Compressor
Contactor Aux.
Compressor
Block
Contactor
Terminal
BLOWER MOTOR
2
Start Kit
INDUCED DRAFT
4
INDUCED DRAFT
CONTROL (OPT.)
R
CONTROL MODULE
COMPRESSOR
CONTACTOR
COMPRESSOR
LOW PRESSURE
CONTROL
LPC
LPC
C
ALR
Y
HPC
CC
Y1
2
R
FURNACE CONTROL BOARD
K3
K4
K4
K2
COOL
D1
BLOWER RELAY
LOW AMBIENT
Heater
HIGH PRESSURE
208
24VAC
240
COM
Transformer
Use for 208V Operation
BOARD
CONTROL
FURNACE
VALVE
GAS
1
SWITCH
PRESSURE
K1
K1
K4
K1
K2
K3
12
11
3
6
8
10
7
9
5
4
2
LIMIT
SEC.
ROLLOUT
FLAME
LIMIT
PRIM.
W2
L1
5 Pin Plug
HIGH SPEED
SOLENOID
L2 L2 L2
Summary of Contents for WG3S1-A
Page 11: ...Manual 2100 483E Page 11 of 59 FIGURE 2A MOUNTING INSTRUCTIONS FOR WG3S1 ...
Page 12: ...Manual 2100 483E Page 12 of 59 FIGURE 2B MOUNTING INSTRUCTIONS FOR WG4S1 AND WG5S1 ...
Page 15: ...Manual 2100 483E Page 15 of 59 FIGURE 6 COMMON WALL MOUNTING INSTALLATIONS ...
Page 25: ...Manual 2100 483E Page 25 of 59 FIGURE 11 GAS PIPE CONNECTION ...