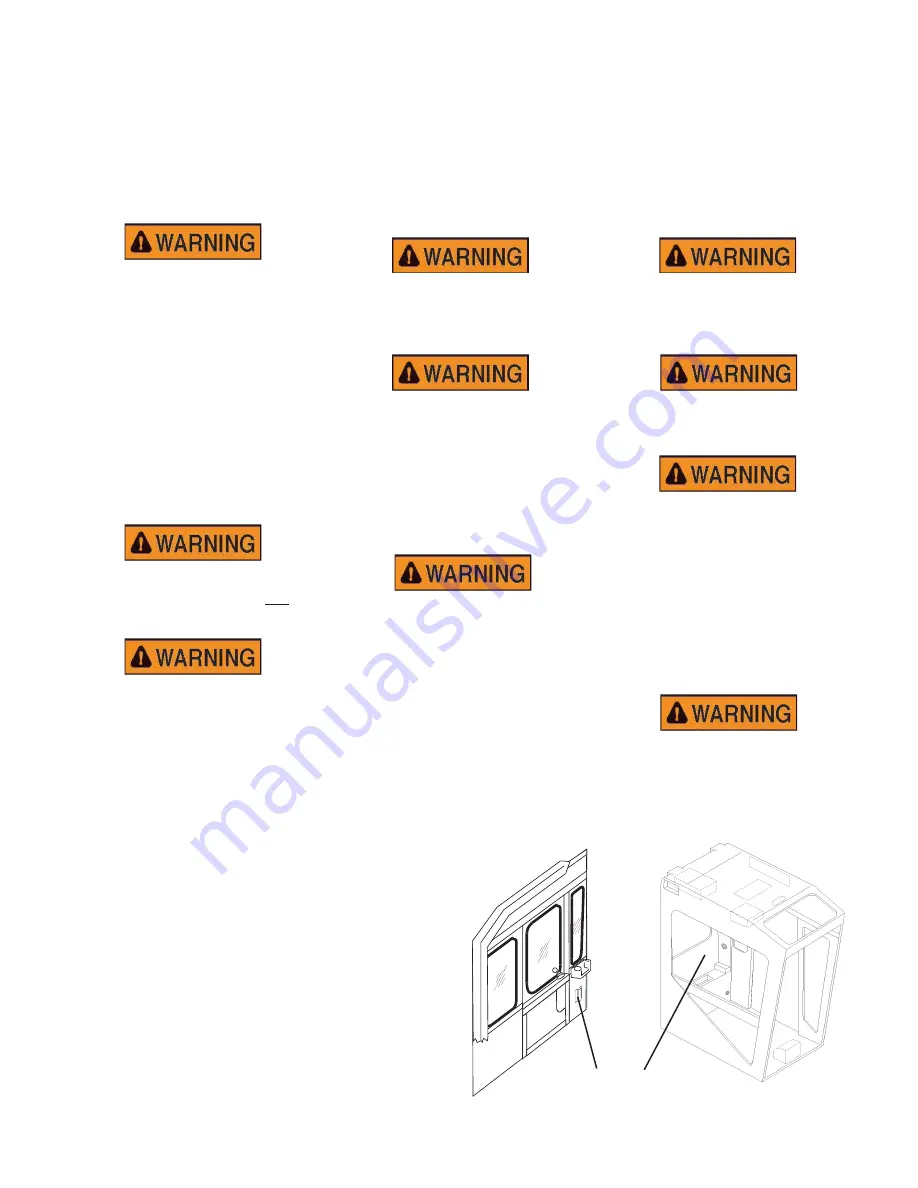
Service Manual
495B SE (S)
13
Last Updated - 9/28/2016
FIRE PREVENTION
This machine may have several components which are at high temperatures under normal operating conditions, such
as the engine, exhaust system, brake system and transmission.
Clean the machine often. High pressure washing of the machine is suggested every 1000 hours (or 6 months) and
always after a spill.
The following list of hazards provides information which will help to prevent fires:
Always keep a fire extinguisher and first aid
kit where they can be easily reached in
case of fire and keep these items properly
maintained.
Operating personnel should be instructed on
what to do in case of fire and be required to
demonstrate how to use fire extinguisher and
fire suppression equipment.
Any portable fire extinguisher or fire
suppression system carried on the machine
that has been used, should be recharged
or replaced before the machine resumes
operating. Fire extinguisher manufacturers
recommended service intervals should be
followed.
Allow machine to cool down by idling the
engine for a while before shut-down. Many
engine and transmission fires start
after
shut-down.
Before adding fuel, shut down the engine and
allow it to cool. Never smoke while handling
fuel or working on either the fuel or the
hydraulic system.
Do not use the machine in areas with explo-
sive dust or gases that can be ignited by
arcs, sparks, hot components, or exhaust
fumes.
Daily inspect the machine for flammable
debris, removing any twigs, leaves, straw,
rags, fluid spills or leaks, dirt or grime.
Pay special attention to areas such as the
engine, engine cooling system, exhaust sys-
tem, battery, electrical connections, brake
systems, transmission/drivetrain, fuel system
and hydraulic system. Clean as often as
necessary to help prevent overheating and
combustion.
The electrical system (battery, electrical
connections, etc.) can be a source of arcs or
sparks if damaged or incorrectly maintained.
Daily inspect all electrical wiring and connec-
tions for damage. Keep the battery terminals
clean and tight. Replace or repair any dam-
aged part. Use proper battery connection and
disconnection procedures.
Daily inspect all fuel and hydraulic oil tubes,
hoses, and fittings for damage and leakage.
Tighten or replace as necessary. Always
clean fluid spills.
Do not use ether or starting fluids on diesel
engines with glow plugs. These starting aids
can explode and injure bystanders.
Before doing welding of any kind, clean
machine and disconnect battery cables.
Cover rubber hoses, battery, and other flam
-
mable parts. Never ground an arc welder or
electrical accessories through turntable or
boom bearings as arcing may occur causing
bearing damage.
Do not weld on any structural member unless
specifically authorized by Barko
Hydraulics. Any unauthorized welding or
welding procedures will void the warranty, and
may cause structural damage.
Read the Engine Manual that comes with ev-
ery machine for complete engine operating
and engine safety instructions.
INSTALLATION OF FIRE EXTINGUISHER BRACKET
The cabs have an optional fire extinguisher mounting
plate that is welded to the outer shell of the cab.
1. Feel for the location of the plate through the
fabric, located below cup holder or on the
back wall (see drawing).
2. Place the bracket in the appropriate position
over the fabric ensuring both the top and
bottom hole fall within the mounting plate.
3. Using 3/4" long self tapping screws drill
through the fabric and the mounting plate. The
sound suppressant material has already been
removed.
NOTE: Using any screw over 3/4" will damage
outer shell of cab.
Fire Extinguisher
Mounting Plate
Summary of Contents for 495B - SE
Page 3: ...Introduction...
Page 15: ...Maintenance...
Page 18: ...Service Manual Last Updated 9 28 2016 495B SE S 18 SERVICE SCHEDULE...
Page 19: ...Service Manual 495B SE S 19 Last Updated 9 28 2016 SERVICE SCHEDULE CONTINUED...
Page 20: ...Service Manual Last Updated 9 28 2016 495B SE S 20 SERVICE SCHEDULE CONTINUED...
Page 21: ...Service Manual 495B SE S 21 Last Updated 9 28 2016 SERVICE SCHEDULE CONTINUED...
Page 22: ...Service Manual Last Updated 9 28 2016 495B SE S 22 SERVICE SCHEDULE CONTINUED...
Page 28: ...Hydraulic...
Page 29: ...Service Manual 495B SE S 29 Last Updated 9 28 2016 HYDRAULIC DRAWING 603 01594...
Page 30: ...Service Manual Last Updated 9 28 2016 495B SE S 30 HYDRAULIC SERVO DRAWING 603 01593...
Page 31: ...Service Manual 495B SE S 31 Last Updated 9 28 2016 HYDRAULIC SCHEMATIC 607 00185...
Page 32: ...Service Manual Last Updated 9 28 2016 495B SE S 32 HYDRAULIC DRAWING TANDEM 603 01574...
Page 33: ...Service Manual 495B SE S 33 Last Updated 9 28 2016 HYDRAULIC SERVO TANDEM 603 01573...
Page 34: ...Service Manual Last Updated 9 28 2016 495B SE S 34 HYDRAULIC SCHEMATIC TANDEM 607 00184...
Page 56: ...Electrical...
Page 71: ...Service Manual 495B SE S 71 Last Updated 9 28 2016 AIR CONDITIONER MAINTENANCE CONTINUED...
Page 72: ...Service Manual Last Updated 9 28 2016 495B SE S 72 AIR CONDITIONER MAINTENANCE CONTINUED...
Page 73: ...Service Manual 495B SE S 73 Last Updated 9 28 2016 AIR CONDITIONER MAINTENANCE CONTINUED...
Page 74: ...Service Manual Last Updated 9 28 2016 495B SE S 74 AIR CONDITIONER MAINTENANCE CONTINUED...
Page 78: ...Maintenance...
Page 88: ...Structural...
Page 93: ...Trouble Shooting...