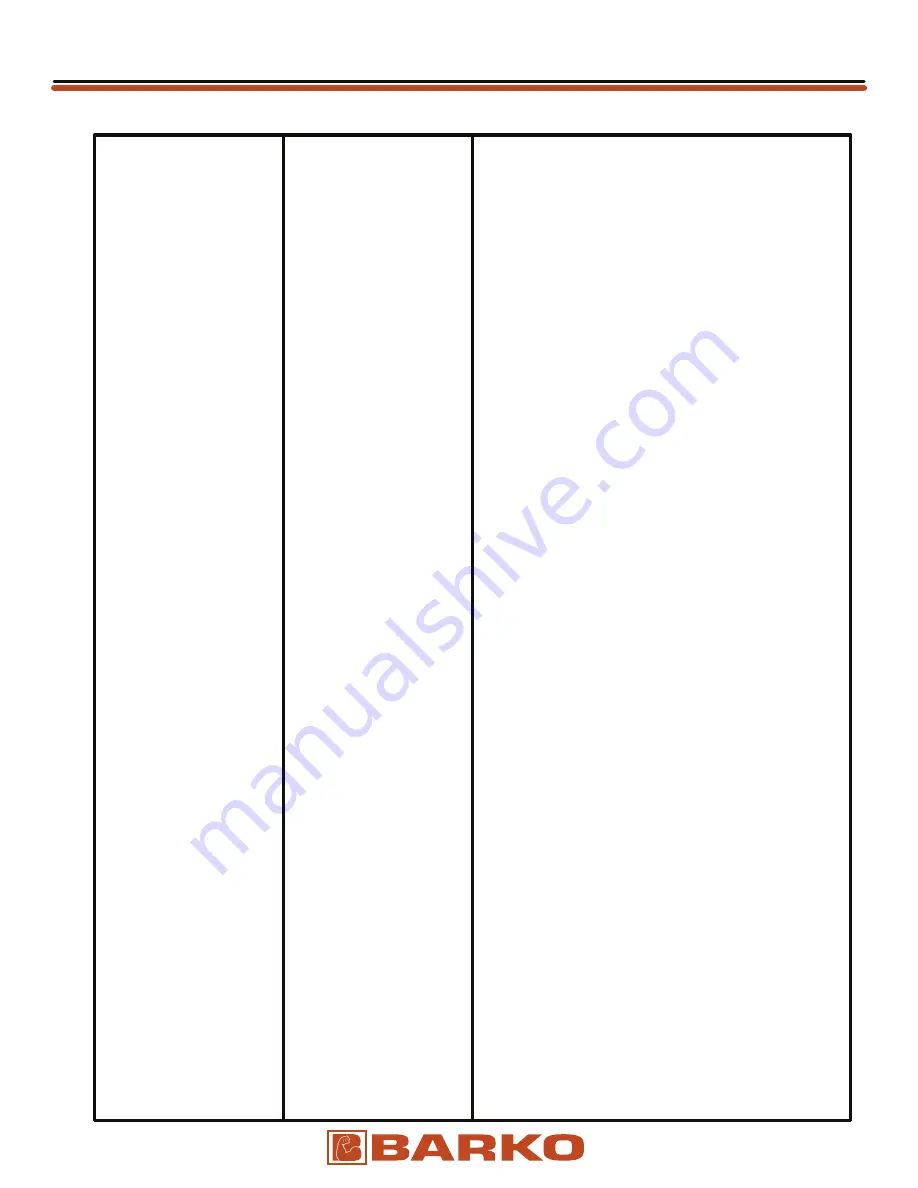
60-35
®
SERVICE- HYD PUMP T6, T7 VANE
(continued...)
3. TROUBLESHOOTING
2.
Not enough flow (or not
the flow required)
a) Are the components
OK?
b) Is the connection from
the tank to the pump
correct?
c) Is the tank design
correct?
d) Is the oil convenient?
c-4) Check if this inlet hose is not too close to the tank wall
or to the bottom of the tank and therefore limits the ''vein
flow''.
c-2) Check if the suction pipe is under the oil level during
the complete cycle of the machine.
b-2) Check if the inlet hose is convenient for the required
velocity (0,5 < V < 1,9 m/s).
c-8) Check if the tank is not fully tight, not allowing the
atmospheric pressure to apply.
c-3) Check if the inlet hose fitted in the tank is cut with an
angle wider than 45°.
a-6) Check if the cylinder inner seals are not ruined and
therefore allow internal leakage.
b-4) Check if the gate valve is not semi-open.
c-6) Check if baffles are required to allow correct
deareation of the fluid.
c-1) Check if the oil level is correct.
d-1) Check if the oil characteristics are not incompatible
with the pumps requirements.
d-2) Check if the viscosity is not too high, therefore
«sticking» some vanes in the rotor or blocking the vein
fluid.
b-3) Check if the pump is not too high compared to the oil
level or if the pump is not too far from the tank (check the
inlet absolute pressure with the catalog values).
c-5) Check if the suction hose is not located near the
return line and therefore sucking a lot of air coming from
these turbulences.
a-5) Check if the hydraulic motor is not leaking internally
due to a bad efficiency, low viscosity...
b-1) Check if there is no air intake between the pump and
the inlet pipe (bad seals for example).
d-3) Check if the high temperature does not destroy the
viscosity of the fluid. Doing so, the internal leakage will
«consume» the flow.
c-7) Check if the air filter is not clogged or undersized (not
well dimensioned).
b-5) Check if the inlet strainer is sized correctly (250 m
mesh mini.) or not clogged.
a-1) Check the displacement of the pump.
a-2) Check if the speed of the pump is not too low or too
high (E motor or thermic engine sized too small so
dropping the speed too low...).
a-3) Check if the main relief valve is not set at an
extremely low pressure and therefore venting some flow
back to the tank.
a-4) Check if in the directional valves the spools are not
sticking in a position that brings part of the flow back to the
tank.
06/05/2019
Updated
SERVICE
Summary of Contents for 830B
Page 4: ...THIS PAGE INTENTIONALLY BLANK SUPERIOR WI USA www barko com...
Page 42: ...THIS PAGE LEFT INTENTIONALLY BLANK...
Page 48: ...THIS PAGE LEFT INTENTIONALLY BLANK...
Page 50: ...THIS PAGE LEFT INTENTIONALLY BLANK...
Page 54: ...THIS PAGE LEFT INTENTIONALLY BLANK...
Page 60: ...THIS PAGE LEFT INTENTIONALLY BLANK...
Page 70: ...THIS PAGE LEFT INTENTIONALLY BLANK...
Page 94: ...THIS PAGE LEFT INTENTIONALLY BLANK...
Page 102: ...THIS PAGE LEFT INTENTIONALLY BLANK...
Page 104: ...THIS PAGE LEFT INTENTIONALLY BLANK...
Page 114: ...THIS PAGE LEFT INTENTIONALLY BLANK...
Page 118: ...THIS PAGE LEFT INTENTIONALLY BLANK...
Page 124: ...THIS PAGE LEFT INTENTIONALLY BLANK...
Page 133: ...THIS PAGE LEFT INTENTIONALLY BLANK...
Page 134: ...THIS PAGE LEFT INTENTIONALLY BLANK...
Page 138: ...THIS PAGE LEFT INTENTIONALLY BLANK...
Page 172: ...THIS PAGE LEFT INTENTIONALLY BLANK...
Page 181: ...THIS PAGE LEFT INTENTIONALLY BLANK...
Page 182: ...THIS PAGE LEFT INTENTIONALLY BLANK...
Page 184: ...THIS PAGE LEFT INTENTIONALLY BLANK...
Page 194: ...THIS PAGE LEFT INTENTIONALLY BLANK...
Page 207: ...THIS PAGE LEFT INTENTIONALLY BLANK...
Page 208: ...THIS PAGE LEFT INTENTIONALLY BLANK...
Page 210: ...THIS PAGE LEFT INTENTIONALLY BLANK...
Page 215: ...THIS PAGE LEFT INTENTIONALLY BLANK...
Page 216: ...THIS PAGE LEFT INTENTIONALLY BLANK...
Page 217: ...THIS PAGE LEFT INTENTIONALLY BLANK...