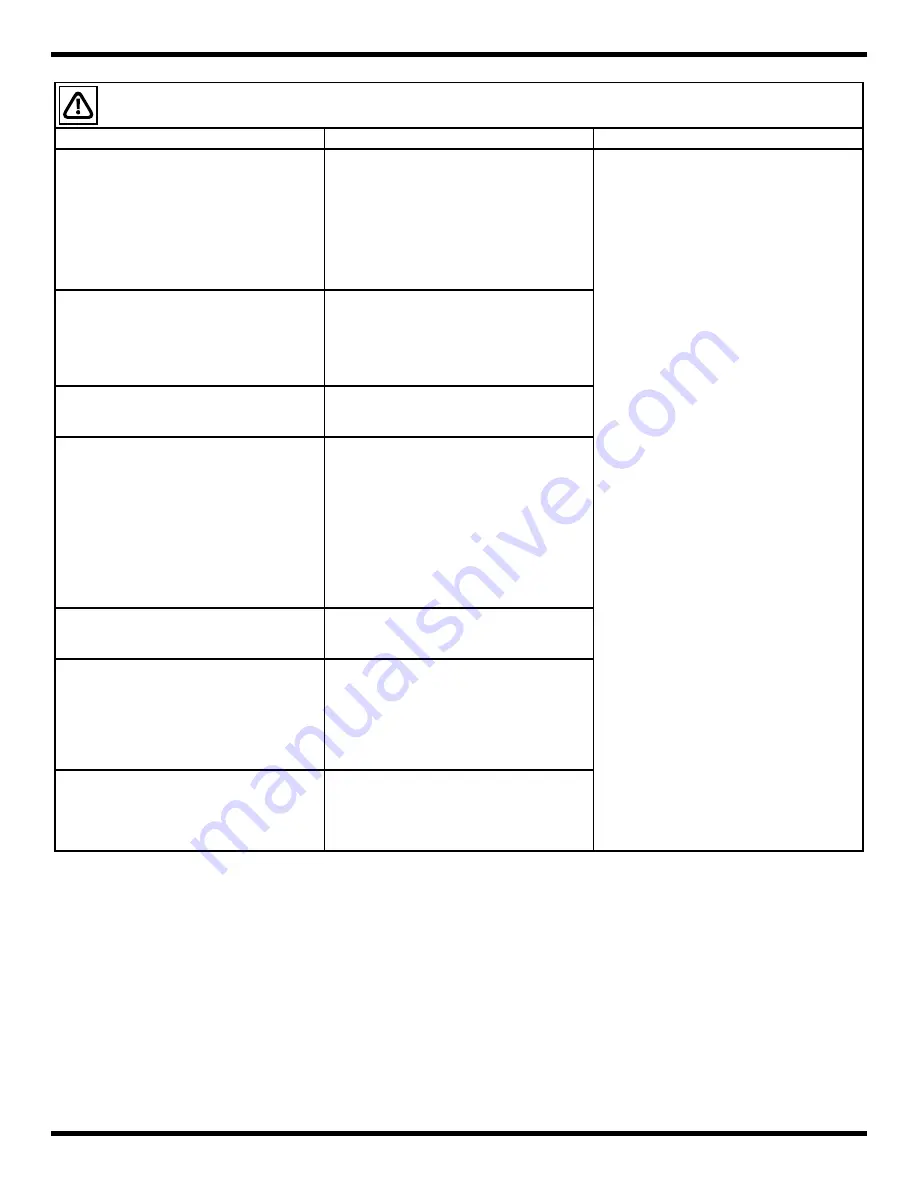
9
Risk of electric shock. Always disconnect the pump from the power source before handling inspections or repairs.
Symptom
Possible Cause(s)
Corrective Action
Pump will not run
1. Poor electrical connection, blown fuse, tripped
breaker or other interruption of power;
improper power supply
2. Motor or switch inoperative (go to manual
operation)
2a. Float movement restricted
2b. Switch will not activate pump or is defective
2c. Defective motor
3. Insuffi cient liquid level
1. Check all electrical connections for security.
Have electrician measure current in motor leads,
if current is within ± 20% of locked rotor Amps,
impeller is probably locked. If current is 0,
overload may be tripped. Remove power, allow
pump to cool, then re-check current.
2a. Reposition pump or clean basin as required to
provide adaquate clearance for float
2b. Disconnect level control. Set ohmmeter for a
low rang, such as 100 ohms full scale and
connect to level control leads. Actuate level
control manually and check to see that
ohmmeter shows zero ohms for closed switch
and full scale for open switch. (Float Switch)
2c. Check winding insulation (Megger Test) and
winding resistance. If check is outside of range,
dry and re-check. If still defective, replace per
service instructions.
3. Make sure liquid level is above the pump
4. Re-check all sizing calculations to determine
proper pump size.
5. Check discharge line for restrictions, including
ice if line passes through or into cold areas.
6. Remove and examine check valve for proper
installation and freedom of operation
7. Open valve
8. Check impeller for freedom of operation,
security and condition. Clean impeller cavity
and inlet of any obstruction
9. Loosen union slightly to allow trapped air to
escape. Verify that turn-off level of switch is set
so that the suction is always flooded. Clean vent
hole
10. Check rotation. If power supply is three phase,
reverse any two of three power supply leads to
ensure proper impeller rotation
11. Repair fixtures as required to eliminate leakage
12. Check pump temperature limits and fluid
temperature
13. Replace portion of discharge pipe with flexible
connector or tighten existing piping.
14. Turn to automatic position
15. Check for leaks around basin inlet and outlets
Pump will not turn off
2a. Float movement restricted
2b. Switch will not activate pump or is defective
4. Excessive inflow or pump not properly sized for
application
9. Pump may be air locked causing pump not to flow
14. H-O-A switch on panel is in "HAND" position
Pump hums but doesn’t run
1. Incorrect low voltage
8. Impeller jammed or loose on shaft, or inlet
plugged
Pump delivers insufficient capacity
1. Incorrect low voltage
4. Excessive inflow or pump not properly sized for
application
5. Discharge restricted
6. Check valve partially closed or installed backwards
7. Shut-off valve closed
8. Impeller jammed or loose on shaft, or inlet
plugged
9. Pump may be air locked causing pump not to flow
10. Piping fixtures leaking or discharge before the
nozzle
Pump cycles too frequently or runs periodically
when f ixtures are not in use
6. Check valve partially closed or installed backwards
11. Fixtures are leaking
15. Ground water entering basin
Pump shuts of f and turns on independent of
switch, (trips thermal overload protector).
CAUTION!
Pump may start unexpectedly.
Disconnect power supply.
1. Incorrect low voltage
4. Excessive inflow or pump not properly sized for
application
8. Impeller jammed or loose on shaft, or inlet
plugged
12. Excessive water temperature (internal
protection only)
Pump operates noisily or vibrates excessively
2c. Worn bearings, motor shaft bent
5. Debris in impeller cavity or broken impeller
10. Pump running backwards
13. Piping attachments to building structure too
loose or rigid
NOTE:
Barmesa Pumps assumes no responsibility for damage or injury due to disassembly in the field. Disassembly of the pumps or supplied accessories other
than at Barmesa Pumps or its authorized service centers, automatically voids warranty.
Troubleshooting Chart
barmesa.com
Summary of Contents for BPEV512 Series
Page 11: ...10 barmesa com...