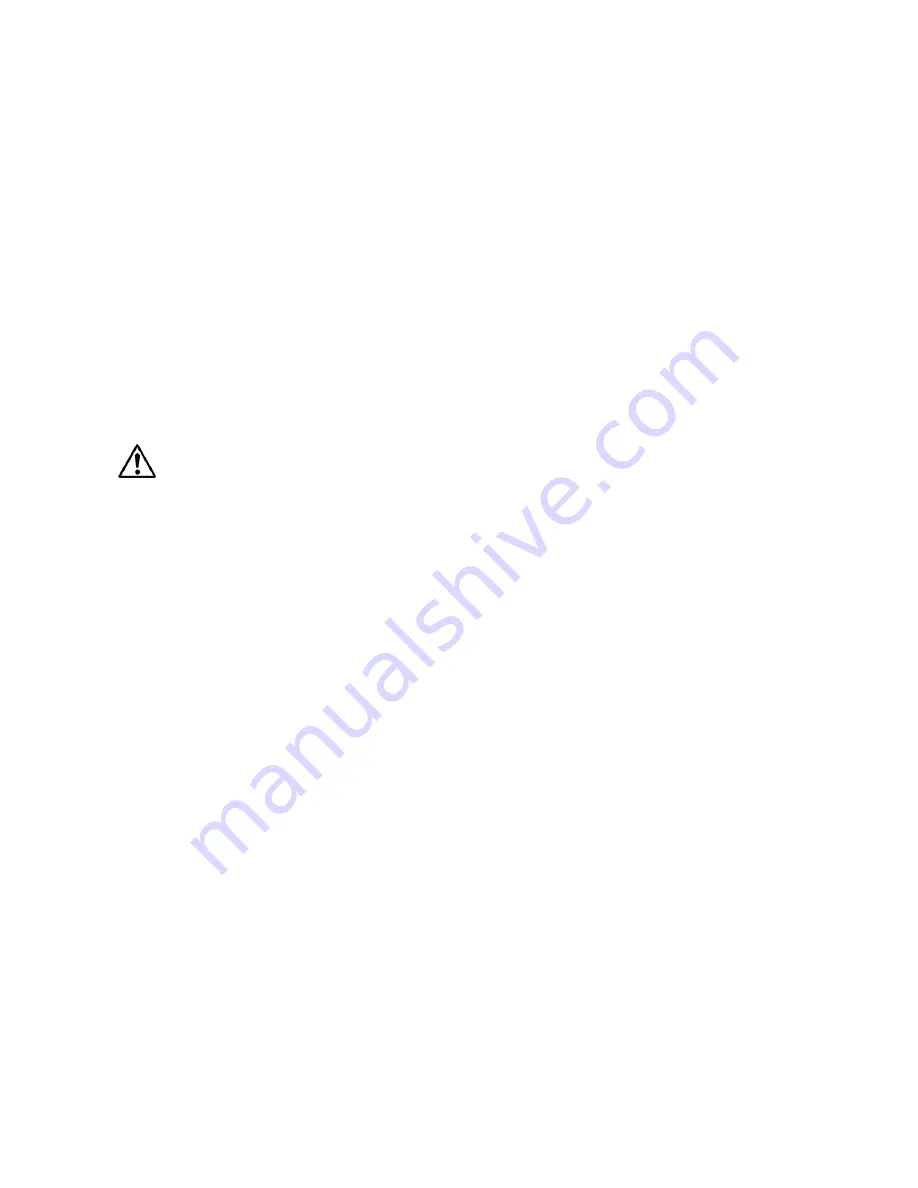
825TKL OWNER’S MANUAL 10/17/22 Page 17 of 22
BATTERY MAINTENANCE (continued)
BATTERY VOLTAGE LEVEL: Check the voltage level using an appropriate meter. Always keep
the battery fully charged and clean to help prolong battery life expectancy, especially when the
temperature is below 32°F (0°C). For off-season long-term storage, we recommend removing the
battery from the Track Loader and storing where the ambient temperature remains above freezing.
TO CHARGE THE BATTERY follow this procedure:
1.
Disconnect the battery cables, removing the negative cable first.
2.
Remove the battery from the machine.
3.
Clean the battery exterior with paper towels.
4.
If the battery posts and cable terminals are corroded, clean them with a wire brush cleaner tool. A
solution of four parts water and one part baking soda is helpful.
5.
Apply a light coating of grease to the battery terminals to prevent corrosion.
6.
Check the battery electrolyte level (see procedure above).
7.
Ensure that the battery caps tightly in place.
Do not charge the battery near flames or sparks, or while smoking.
WARNING
: Battery fumes are flammable and explosive. Avoid explosion hazard that could
blind and burn. Tools and jumper cable clamps can make sparks, so use them with care.
Shield eyes and face, and wear rubber gloves.
8.
Connect a 12-volt DC battery charger and charge at 3 to 4 amperes for 4 to 8 hours. Do not
overcharge.
9.
When the battery is fully charged, turn off and unplug the charger from the electrical outlet, then
disconnect the charger leads from the battery posts.
10.
Reinstall the battery securely into the Track Loader.
11.
Reconnect the cables. Attach the positive cable first, then the negative one.