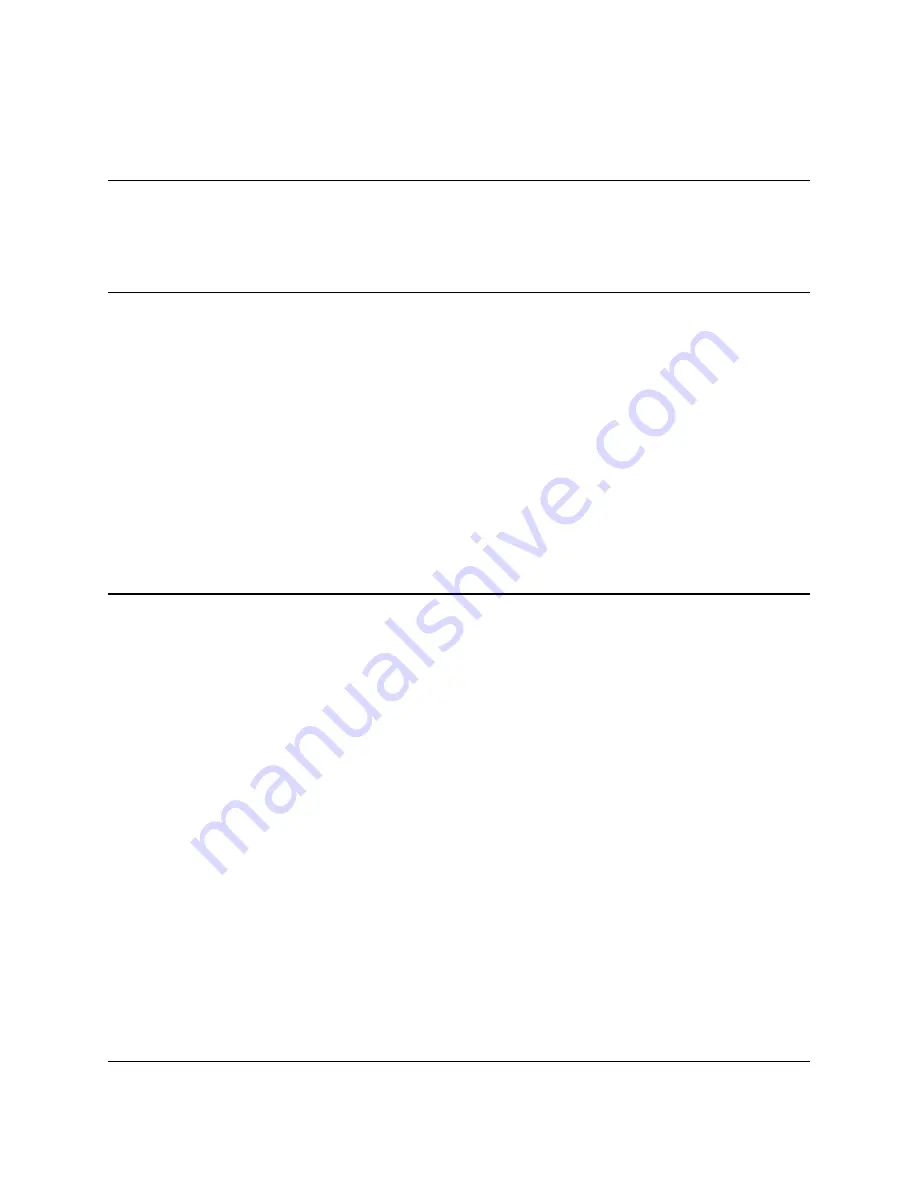
BE1-24 Testing
5-1
SECTION 5 • TESTING
GENERAL
In the event the relay is not to be installed immediately, store the relay in its original shipping carton. When
the relay is to be placed in service, it is recommended that the operational test procedure in this section be
performed prior to installation.
RELAY OPERATING PRECAUTIONS
Before installation or operation of the relay, note the following precautions:
1.
A minimum of 0.2 A in the output circuit is required to ensure operation of current operated
targets.
2.
The relay is a solid-state device. If a wiring insulation test is required, remove the
connection plugs and withdraw the cradle from its case.
3.
When the connection plugs are removed, the relay is disconnected from the operating circuit
and will not provide system protection. Always be sure that external operating (monitored)
conditions are stable before removing a relay for inspection, test, or service.
4.
Be sure the relay case is hard wired to earth ground using the ground terminal on the rear
of the unit. It is recommended to use a separate ground lead to the ground bus for each
relay.
BUILT-IN-TEST
The relay incorporates the BIT function as a convenient hardware test. This troubleshooting aid can verify
each indicator and output driver circuit for proper operation. To implement the BIT, proceed as follows.
Step 1.
With the unit in a power-up condition place switch S1 (on the logic board) to the TEST position.
Step 2.
Verify that the relay runs through its programmed sequence of events as follows.
a.)
Timed trip pickup LED turns ON.
b.)
Timing status display turns ON (each LED turns ON in ascending order, green to red).
c.)
Alarm pickup LED turns ON.
d.)
Instantaneous output relay energizes.
e.)
Alarm output relay energizes.
f.)
Timed trip output relay energizes.
If auxiliary output relays have been specified, they will energize simultaneously with the respective main
output relays.
Summary of Contents for BE1-24
Page 9: ...1 4 BE1 24 General Information Figure 1 1 Inverse Square vs Two Step...
Page 10: ...BE1 24 General Information 1 5 Figure 1 2 Protection Characteristics of the BE1 24...
Page 12: ...BE1 24 General Information 1 7 Figure 1 3 Style Number Identification Chart...
Page 16: ...BE1 24 General Information 1 11 Figure 1 4 Inverse Square Characteristic Curves...
Page 19: ...2 2 BE1 24 Human Machine Interface Figure 2 1 Location of Controls and Indicators...
Page 27: ...4 2 BE1 24 Installation Figure 4 1 M1 Case Outline Dimensions Front View...
Page 30: ...BE1 24 Installation 4 5 Figure 4 4 M1 Case Double Ended Panel Drilling Diagram Rear View...
Page 31: ...4 6 BE1 24 Installation Figure 4 5 M1 Case Panel Drilling Diagram...
Page 32: ...BE1 24 Installation 4 7 Figure 4 6 M1 Case Projection Mounting Outline Dimensions Rear View...
Page 34: ...BE1 24 Installation 4 9 Figure 4 7 Typical Internal Connections...