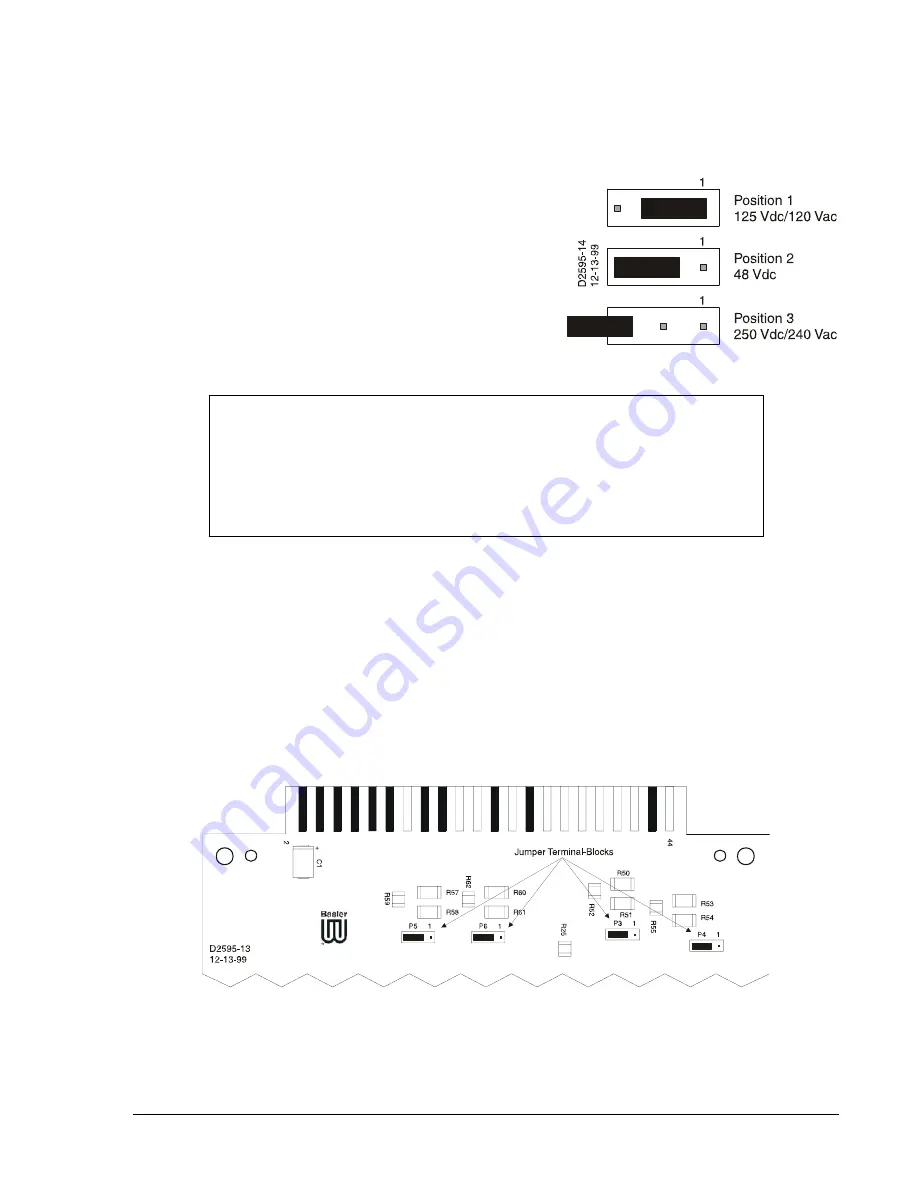
9310200990 Rev G
BE1-79A Installation and Configuration
5-7
Motor Voltage
No adjustment is required for the motor voltage applied at terminals 5 and 6. The applied voltage can
range from 120 to 240 Vac or 125 to 250 Vdc. These terminals serve as the input to the BE1-79A power
supply and control functions.
Contact Sensing Inputs
Energizing levels for contact sensing inputs V1 through
V4 are jumper selectable for operation at three nominal
voltage levels. Jumper P3 controls the operating voltage
for V1, P4 controls V2, P5 controls V3, and P6 controls
V4. Nominal voltage levels of 125 Vdc/120 Vac, 48 Vdc,
or 250 Vdc/240 Vac may be selected. Figure 5-6
illustrates the three possible jumper positions for P3
through P6. Input V5 is dedicated to monitoring the relay
power supply input and is not jumper selectable.
Figure 5-6. Contact Sensing Jumpers
The following paragraphs describe how to locate and change the position of the contact-sensing jumpers.
1. Remove the four Phillips screws from the front panel and separate the front panel from the relay
chassis.
2. Carefully grasp and remove the Digital circuit board (top circuit board) from the relay chassis. Take
care not to damage any of the circuit board components. Observe all electrostatic discharge (ESD)
precautions when handling the circuit board. Place the circuit board on an ESD-safe surface.
3. Locate the four jumper terminal blocks (P3 through P6) on the circuit board. The jumper terminal
blocks are located on the component side of the circuit board near the rear contact fingers (see
Figure 5-7). Each terminal block has three pins and each jumper is factory installed on pins 2 and 3.
Figure 5-6 illustrates each of the three jumper positions.
Figure 5-7. Contact Sensing Jumper Locations
4. To select operation at 125 Vdc or 120 Vac, remove the jumper from pins 2 and 3 and position it on
pins 1 and 2. To select operation at 250 Vdc or 240 Vac, remove the jumper from pins 2 and 3 and
position it on pin 3 for storage. (Only pin 3 of the terminal block should be covered.)
NOTE
In certain applications where 240 Vac control voltage is used, control circuit
feedback can occur through system inductive coupling. This feedback can result
in erroneous signals, causing relay operation. If there is a potential for control
circuit feedback, the jumper selectable voltage range should be changed from
the 48 Vdc factory default setting to a higher position. Selections are provided in
Table 3-1.
Summary of Contents for BE1-79A
Page 1: ...INSTRUCTION MANUAL FOR RECLOSING RELAY BE1 79A Publication 9310200990 Revision G 02 08...
Page 2: ......
Page 8: ...vi BE1 79A Introduction 9310200990 Rev G This page intentionally left blank...
Page 10: ...ii BE1 79A General Information 9310200990 Rev G This page intentionally left blank...
Page 16: ...ii BE1 79A Controls and Indicators 9310200990 Rev G This page intentionally left blank...
Page 20: ...2 4 BE1 79A Controls and Indicators 9310200990 Rev G This page intentionally left blank...
Page 22: ...ii BE1 79A Functional Description 9310200990 Rev G This page intentionally left blank...
Page 34: ...ii BE1 79A Communication Commands 9310200990 Rev G This page intentionally left blank...
Page 40: ...ii BE1 79A Installation and Configuration 9310200990 Rev G This page intentionally left blank...
Page 52: ...ii BE1 79A Testing 9310200990 Rev G This page intentionally left blank...
Page 58: ...6 6 BE1 79A Testing 9310200990 Rev G This page intentionally left blank...
Page 60: ...ii BE1 79A RS Contact Application 9310200990 Rev G This page intentionally left blank...
Page 66: ...ii BE1 79A Terminal Communication 9310200990 Rev G This page intentionally left blank...