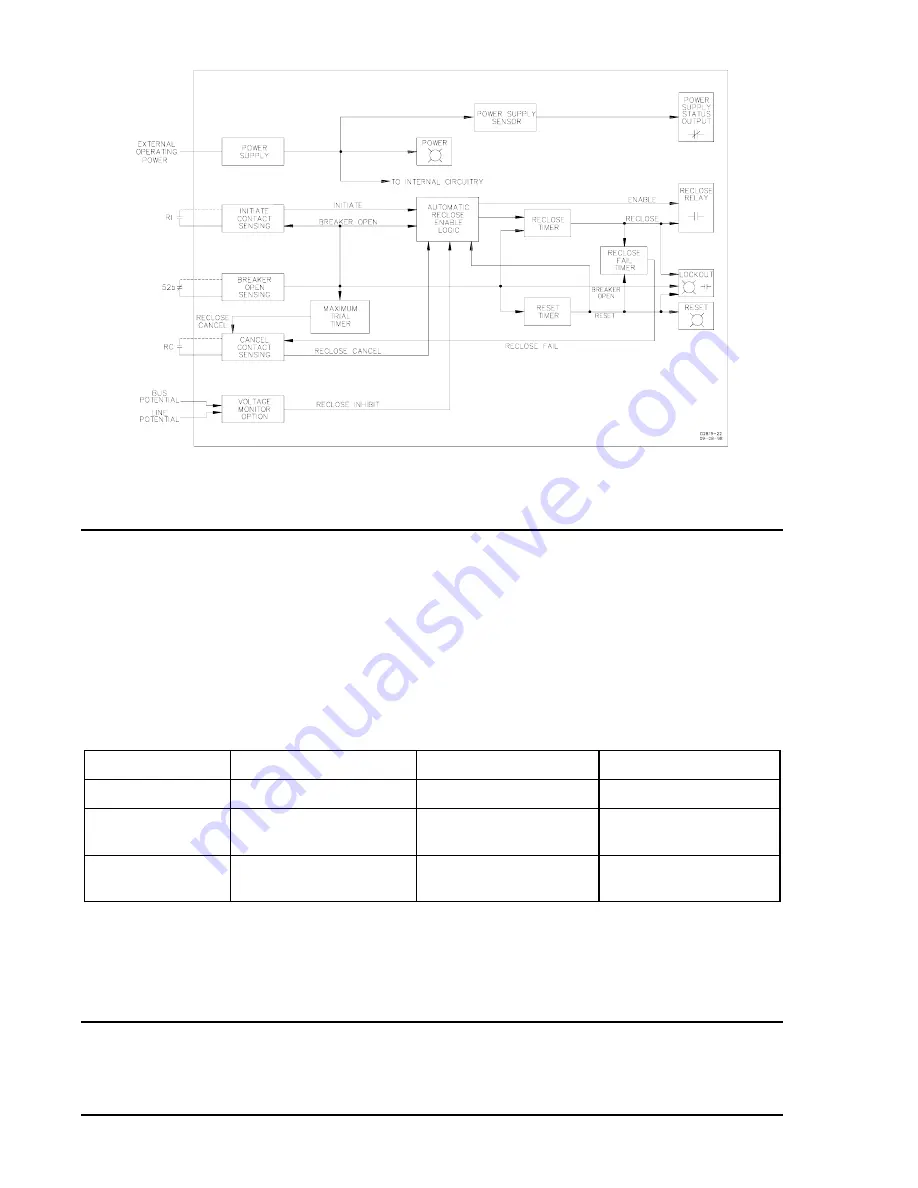
2-2
BE1-79S Functional Description
Figure 2-1. Functional Block Diagram
POWER SUPPLY
Basler Electric enhanced the power supply design for unit case relays. This new design created three, wide
range power supplies that replace the four previous power supplies. Style number identifiers for these
power supplies have not been changed so that customers may order the same style numbers that they
ordered previously. The first newly designed power supplies were installed in unit case relays with EIA date
codes 9638 (third week of September 1996). Relays with a serial number that consists of one alpha
character followed by eight numerical characters also have the wide range power supplies. A benefit of this
new design increases the power supply operating ranges such that the 48/125 volt selector is no longer
necessary. Specific voltage ranges for the three new power supplies and a cross reference to the style
number identifiers are shown in the following table.
Table 2-1. Wide Range Power Supply Voltage Ranges
Power Supply
Style Chart Identifiers
Nominal Voltage
Voltage Range
Low Range
D
24 Vdc
12† to 32 Vdc
Mid Range
B, C
48, 125 Vdc,
120 Vac
24 to 150 Vdc,
90 to 132 Vac
High Range
X
125, 250 Vdc,
120, 240 Vac
62 to 280 Vdc,
90 to 270 Vac
† 14 Vdc is required to start the power supply.
Relay operating power is developed by the wide range, isolated, low burden, flyback switching, solid state
power supply. Nominal ±12 Vdc is delivered to the relay internal circuitry. Input (source voltage) for the
power supply is not polarity sensitive. A red LED turns ON to indicate that the power supply is functioning
properly.
INITIATE CONTACT SENSING (RI)
When an external form A contact (RI) is closed (typically by a protective relay), the initiate contact sensing
circuit generates an INITIATE signal to the automatic reclose enable logic.
Summary of Contents for BE1-79S
Page 26: ...BE1 79S Installation 4 5 Figure 4 5 S1 Case Panel Drilling Diagram Semi Flush Mounting...
Page 28: ...BE1 79S Installation 4 7 Figure 4 8 Voltage Sensing Circuit Connections...
Page 29: ...4 8 BE1 79S Installation Figure 4 9 RI RC and 52b Sensing Circuit Connections...
Page 30: ...BE1 79S Installation 4 9 Figure 4 10 Internal Connection Diagram With Power Supply Status...